Introduction
In industries like telecommunications, healthcare, and manufacturing, the availability of service parts is mission-critical. Delays in obtaining essential components can lead to operational downtime, increased costs, and dissatisfied customers. Traditional forecasting models—often based on statistical analysis and time-series data—struggle to account for the complex interdependencies between parts, maintenance schedules, and external factors.
Enter Graph Neural Networks (GNNs)—a cutting-edge machine learning approach designed to capture relationships between interconnected entities. By modeling service parts, equipment, and maintenance activities as nodes in a graph, GNNs enhance forecasting accuracy, adaptability, and operational efficiency. This article explores how GNNs revolutionize service parts demand forecasting, providing a competitive advantage in field service management.
The Limitations of Traditional Forecasting Models
Service parts demand forecasting has long relied on conventional statistical techniques, such as:
- Linear Regression Models: Projecting future demand based on historical consumption trends.
- Historical Consumption Patterns: Analyzing past data to anticipate future needs.
- Probabilistic Approaches: Using probability distributions to estimate demand variations.
While these methods establish a baseline, they fail to address key industry challenges:
- Interdependent Demand: Service parts do not operate in isolation; failure of one component often impacts others. Traditional models struggle to capture these intricate relationships.
- Sparse Data & Cold Start Problems: New equipment models or rarely used service parts lack sufficient historical data, leading to inaccurate forecasts.
- Supply Chain Uncertainty: Delays in supplier lead times and logistics constraints require adaptive forecasting mechanisms.
- Real-Time Adaptation: Traditional models lack the agility to incorporate new failure reports, technician feedback, or sensor data in real-time.
How GNNs Revolutionize Service Parts Forecasting
Graph Neural Networks (GNNs) introduce a paradigm shift by representing service parts and their dependencies through a structured graph model. In this framework:
- Nodes represent service parts, equipment, or maintenance events.
- Edges define the relationships between them, such as failure correlations or replacement cycles.
Key Advantages of GNNs in Service Parts Forecasting
- Enhanced Predictive Accuracy: By capturing interdependencies, GNNs provide more precise demand forecasts than traditional models.
- Real-Time Adaptability: GNNs continuously update predictions based on incoming failure reports and technician insights.
- Supply Chain Optimization: Proactively identifies potential part shortages and suggests alternative solutions, mitigating operational risks.
- Dynamic Learning: Unlike static models, GNNs evolve with changing maintenance patterns and environmental factors.
With over 15 years of experience in Salesforce and Service Cloud, Balasubramanian has worked extensively in field service management, witnessing the critical role service parts forecasting plays in minimizing downtime and operational costs. Traditional forecasting models often fail to account for complex interdependencies, which is why I advocate for the adoption of Graph Neural Networks (GNNs) to enhance forecasting accuracy and adaptability.
Implementing GNNs for Service Parts Forecasting
To successfully integrate GNNs, organizations should follow a structured approach:
- Data Preparation: Construct a graph-based representation of service parts, maintenance schedules, and failure relationships.
- Nodes represent individual parts, equipment, or maintenance events.
- Edges define dependencies such as co-failure tendencies, replacement sequences, and operational interactions.
- Model Training: Train the GNN using historical data, ensuring that it captures dependencies and external variables.
- The model learns patterns by analyzing service records, environmental factors, and failure trends.
- It develops a predictive framework to understand how various parts interact over time.
- Real-Time Forecasting: Continuously refine predictions with new service records and operational changes.
- The GNN dynamically adapts to new data, incorporating technician insights, sensor outputs, and unexpected failures.
- This ensures that forecasting remains relevant and accurate in fast-changing service environments.
- Integration with Field Operations: Deploy the model within maintenance workflows, enabling predictive alerts and inventory adjustments.
- Organizations can automate inventory restocking based on anticipated demand.
- Maintenance teams receive proactive alerts for potential failures, enabling timely interventions.
- Supply chain inefficiencies are minimized through intelligent demand-supply balancing.
Conclusion: The Future of AI-Driven Service Parts Management
Graph Neural Networks offer a transformative approach to service parts forecasting, delivering greater precision, adaptability, and efficiency. By leveraging the interconnected nature of service components, organizations can reduce downtime, optimize inventory, and improve overall resource allocation. As industries increasingly adopt AI-driven solutions, GNNs will play a pivotal role in shaping the future of predictive maintenance and service logistics.
About the Author:
Bala Subramanian, a Salesforce and Service Cloud expert, specializes in building scalable applications for field service management. This article underscores his deep insights into service parts forecasting and the potential of AI-driven methodologies like GNNs. Future discussions will explore real-world implementations and best practices for deploying GNN-based forecasting models in field service operations.
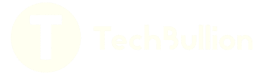