So you’ve decided to replace the exhaust clamps on your vehicle. Great idea—those clamps take a beating over the years and often need replacing. But before you dive under your car, wrench in hand, there are a few common mistakes to avoid. Installing exhaust clamps seems straightforward enough, but mess it up and you’ll end up with leaks, rattles, or worse.
We’ve been there, done that, and learned from experience. In this article, we’ll walk you through how to install exhaust clamps the right way. We’ll show you how to get the perfect fit, ensure maximum strength, and avoid damaging your exhaust pipes or muffler. With some handy tips and the right technique, replacing your exhaust clamps can be an easy DIY job. So grab your tools and let’s get to work—we’ll have you back on the road in no time with a solid exhaust system and a wallet still full of cash.
Common Exhaust Clamp Installation Mistakes to Avoid
The most common mistakes DIYers make when installing exhaust clamp are:
- Choosing the wrong clamp size. Make sure you have the right diameter clamp for your exhaust pipe. Clamps that are too small won’t seal properly and clamps too big won’t grip adequately.
- Not tightening the clamp enough. Those bolts need to be securely tightened so the clamp fits snugly around the pipe. Finger tightening isn’t going to cut it. Use a wrench to tighten the bolts in an alternating pattern until the clamp is firmly in place.
- Not positioning the clamp correctly. The clamp should be placed over the joint you’re connecting, with equal amounts of pipe on either side. Don’t place clamps too close to bends or at the very end of a pipe.
- Not re-tightening the clamp. After installing the clamp, start up the vehicle to heat up the exhaust system, then shut it off. Retighten the clamp bolts since the metal and gaskets will expand from the heat. This ensures a solid, leak-free connection as the exhaust cools back down.
- Using the wrong clamp type. V-band clamps, t-bolt clamps, and heavy-duty u-bolt clamps each have specific uses. Make sure you’re choosing a clamp style appropriate for your particular exhaust setup. The wrong style won’t work and will cause leaks.
By avoiding these common mistakes, you’ll ensure a secure installation of your exhaust clamps. Take your time and do it right the first time!
Proper Exhaust Clamp Positioning and Alignment
Proper positioning and alignment of your exhaust clamps is key to avoiding leaks and ensuring maximum performance.
First, install the clamps at least 6 to 8 inches away from the end of any exhaust component like your headers, catalytic converters or mufflers. This gives the clamp enough surface area to grip onto and helps prevent the pipe from slipping out.
Next, make sure the clamp is centered over the joint in the pipe. An off-center clamp can’t distribute pressure evenly and may not seal properly. For the best seal, the clamp should be placed squarely over the middle of the joint.
Double check clamp tightness
Once the clamps are positioned correctly, tighten them firmly to the specified torque using a torque wrench. But be careful not to overtighten, which can damage the clamp or pipe. As a rule of thumb, tighten the clamp so it’s snug but you can still slide a fingernail under it. Then give it a final check after a few heat cycles to ensure it’s still tight.
Lastly, inspect all your clamps regularly and replace any that are damaged or rusty. Faulty or corroded clamps won’t grip securely and need to be swapped out to avoid exhaust leaks and maintain safe exhaust flow.
By carefully positioning, aligning and tightening your exhaust clamps, you’ll avoid many common installation mistakes. Be meticulous during the initial install and keep an eye on clamps over time. Your ride will remain leak-free and high-performing for years to come.
What is oil catch can kit?
An oil catch can kit is an aftermarket automotive component designed to help prevent the buildup of oil and contaminants in the intake system of an internal combustion engine. It consists of a specialized container, hoses, and fittings.
Here’s how it works:
Collection Chamber: The primary component of the kit is the catch can itself. It is a small, sealed container with an inlet and an outlet. Inside the catch can, there is typically a baffle system or other means to trap oil and separate it from the air.
Hoses and Fittings: The catch can is connected to the engine’s crankcase ventilation system using hoses and fittings. One hose is typically connected to the crankcase or valve cover, and another to the intake system.
Function: The catch can is installed in the path of the crankcase ventilation system. As the engine runs, blow-by gases, which contain oil vapors and contaminants, are generated in the crankcase. These gases are normally vented back into the intake system to be burned in the combustion process. However, they can carry oil mist with them.
The catch can intercepts these gases before they reach the intake manifold. Inside the catch can, the baffle system or other design element slows down the flow of air, allowing the oil mist to condense and collect at the bottom of the can.
Maintenance: Periodically, the catch can should be checked and emptied of the collected oil and contaminants to ensure it continues to function effectively.
The benefits of using an oil catch can kit include:
Reduced Carbon Buildup: By preventing oil and contaminants from entering the intake system, a catch can can help reduce carbon deposits on valves and other components.
Improved Engine Performance: A cleaner intake system can lead to better airflow and potentially improved engine performance.
Extended Engine Life: By reducing the amount of contaminants circulating through the engine, a catch can may help extend the lifespan of various engine components.
It’s worth noting that the effectiveness of an oil catch can can vary depending on the specific engine, driving conditions, and other factors. Additionally, some catch cans may require periodic maintenance to ensure optimal performance. When installing an oil catch can kit, it’s important to follow manufacturer recommendations and ensure it complies with any applicable local regulations or emissions standards.
Recommended Torque Specifications for Exhaust Clamps
When installing exhaust clamps, it’s important to use the recommended torque specifications to ensure a secure fit without causing damage.
The typical range for exhaust clamps is 45 to 90 inch-pounds. This means applying 45 to 90 pounds of pressure for every inch of the clamp bolt. As a general rule of thumb, start at the lower end of the range, around 50 to 60 inch-pounds, and check that the clamp is secure but still allows some movement in the pipe. If it’s too loose, gradually increase the torque in small increments, rechecking as you go. It’s best to be cautious, since over-tightening the clamp can lead to cracked manifolds or gaskets.
For specific vehicles and clamp sizes, refer to the guidelines in your owner’s manual or repair guide. If that information isn’t available, you can find recommended torque specs on automotive repair websites and forums. When in doubt, it’s better to under-tighten the clamp slightly. You can then start the vehicle, check for any exhaust leaks using a stethoscope or by listening, and re-tighten as needed.
Double check all clamps after installation and retighten as necessary. Exhaust systems heat up and cool down with each use of the vehicle, which can cause clamps and pipes to shift or loosen over time. Re-tightening the clamps, especially after the first 50 to 100 miles of driving, will help ensure maximum performance and safety.
Keeping these best practices in mind will allow you to confidently install your exhaust clamps to the proper specifications. Taking the time to do it right the first time will save you from hassles down the road.
Conclusion
So there you have it, the keys to avoiding frustration and getting the job done right when installing exhaust clamps. Take your time, do some test fitting, have the right tools on hand, and don’t overtighten. If you follow these tips, you’ll be cruising down the road with a solid exhaust system in no time. And when you hear that satisfying rumble from your tailpipe, you’ll know you did good work avoiding the common mistakes. Now get out there and get clamping – the open road is waiting!
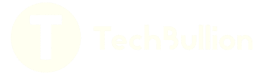