As fulfillment pressures mount and inventory complexity grows, automated storage and retrieval systems are emerging as essential components of modern warehouse automation. These systems dramatically improve space utilization, increase picking speed, and reduce labor dependency, making them a powerful lever for operational scalability.
Whether automating for the first time or scaling up, automated storage and retrieval systems (ASRS) can be the foundation of a faster, more intelligent warehouse and the solution you need to achieve next-level performance.
Let’s explore the basics of an automated storage and retrieval system, its many benefits across different industries, and how it can be integrated with broader warehouse technologies such as warehouse management systems for a transformative level of efficiency, accuracy, and optimization. This will help you decide if ASRS is the right solution for you.
An Overview of ASRS
ASRS may go by other names, such as goods-to-person picking technology, high-density storage and retrieval systems, or a dynamic storage system. Whatever you call it, ASRS delivers improved accuracy, efficiency, and space utilization compared to manual systems.
Imagine walking into a vast library filled from floor to ceiling with books. If you’re looking for one specific book, it could be daunting and time-consuming to locate and retrieve it independently, from pinpointing its location to scaling a ladder to fetch it. An automated library system, however, could identify the book in seconds and deliver it right into your hands.
This is the idea behind ASRS for warehouses. Instead of workers walking the warehouse floor, locating and manually retrieving items with forklifts or other equipment, ASRS solutions rely on computers and automated machinery to store or retrieve inventory. An automated system delivers the item to a manned station, where it can be prepped for shipping. Inventory can be densely stored from floor to ceiling to maximize space since items can be easily and safely retrieved in much less time.
There are many options for setting up automated storage and retrieval systems to suit your needs and requirements. Some of these include:
- Unit-load ASRS: This system is designed to handle heavy loads, such as pallets, and uses cranes, stacker cranes, or shuttles.
- Mini-load ASRS: As the name suggests, this system is suited for smaller items, such as bins and cartons.
- Carousel Modules: This storage system uses rotating shelves or carriers around a central axis. The shelves or carriers can be vertical or horizontal.
- Shuttles: A shuttle system accesses high-density, multi-level racking systems to retrieve goods.
- Floor robots: Instead of an operator walking a warehouse to retrieve goods, floor robots transport items to different warehouse locations.
- Vertical Lift Modules: Also called “columns of trays,” this system stores items vertically in stacked trays.
- Vertical Buffer Modules: This type of system uses vertical space and involves retrieving a bin or tote using a gripper or other mechanism.
- Single Aisle: These systems use narrow aisles with a single crane or shuttle to maximize space, making them useful for large inventory volumes.
These options offer flexible, adaptable ways to integrate ASRS within your warehouse.
Benefits of ASRS
Modern warehouses face many challenges, such as labor shortages, time-consuming manual processes, market unpredictability, and increasing demands for inventory with limited space. ASRS helps you overcome these challenges and optimize operations to continue expanding.
As the backbone of flexible and scalable warehouse automation, ASRS offers many benefits:
- Maximized space. Especially for high-density warehouses, ASRS optimizes space use by using floor-to-ceiling capabilities within a warehouse. Its compact footprint allows businesses more options in how they use available space, such as expanding their manufacturing capabilities, adding more inventory, or even renting out space for additional revenue.
- Reduced labor needs. Workers may walk miles during their shift; with automation, that time is no longer needed and can be shifted to increased productivity. Workers can spend their time on more productive tasks.
- Improved accuracy. Relying on computers and robotics reduces human errors and improves accuracy, which leads to more efficient operations.
- Efficient use of time. In manual operations, time is spent locating an item, searching shelves, and manually retrieving it. With automation, workers can remain at stations and have items picked and delivered to them, reducing worker fatigue. That means more time is spent picking.
- Better ergonomics. ASRS improves ergonomics and increases worker safety by reducing the need for workers to bend down or reach upward to retrieve items continually. This can lead to fewer injuries and a more comfortable work environment, increasing worker satisfaction and retention.
- Scalability for growth. ASRS’s flexibility means it can easily be tailored to different business needs and allows for scalability. As such, it is an ideal solution for optimizing space and increasing inventory for future growth.
ASRS does have some potential downsides. For one, it requires a significant upfront investment. Businesses investing in ASRS must cover the system, installation, and possible upgrades. The system will need ongoing maintenance, incurring additional costs. You may also need to train or upskill staff on using the new system, which will take extra time. Troubleshooting and maintenance may require specialized expertise due to the system’s complexity.
While most companies consider the upfront cost the most significant downside, that initial investment will lead to a safer workplace, smoother operations, and scalability. For many, these benefits will outweigh potential disadvantages.
Integration Across Your Warehouse
Another critical advantage of ASRS is its ability to enhance your existing systems.
ASRS can easily integrate with existing warehouse technologies for greater improvements in efficiency, speed, and scalability. This is where you can start to see next-level performance with automation.
For instance, ASRS can work alongside an advanced palletizing system to streamline loading and unloading pallets. This means more inventory can be processed more quickly and with less manual labor. Automated palletizing can further enhance ASRS’s high-density storage capabilities.
ASRS can be integrated with your warehouse management system for accurate and efficient processes. Integration allows you to use your ASRS to its full potential for streamlined inventory management and decreased labor costs. Think of your WMS as the brain of your warehouse, directing your ASRS to retrieve specific inventory quickly and accurately.
Is ASRS Right for You?
ASRS can transform your operations and help you achieve seamless warehouse automation. But is it the best option for your needs?
ASRS could be the right solution for your warehouse if:
- You want to optimize space to increase your inventory and grow your business. ASRS maximizes the space you already have and supports high-density storage and inventory.
- Your warehouse includes many routine tasks that must be completed manually. With ASRS, you can use automation to save time and keep the systems running 24/7. This frees up labor for more productive work and improves workplace safety and ergonomics.
- You want to scale up to meet rising demands without additional labor costs. ASRS is flexible, adaptable, and scalable.
- You want to make a long-term investment in efficiency. While the up-front costs may be higher than investing more in manual labor, the long-term benefits will reduce costs.
With its multiple benefits for companies looking to save space, save money, and continue to grow, ASRS offers excellent solutions for modern warehouses. It provides efficient, fast storage and retrieval, ready to keep pace with today’s growing demands.
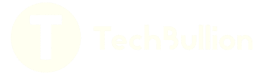