The smooth functioning of printing processes relies on various factors, and one crucial element is the cleanliness of anilox rolls. Anilox rolls, also known as ink metering rolls, play a pivotal role in flexographic and gravure printing by transferring a precise amount of ink to the printing plate. Over time, these rolls can accumulate ink residues, affecting print quality and overall performance. To ensure optimal print results, it is essential to regularly clean anilox rolls using effective cleaning solutions and techniques.
Importance of Anilox Roll Cleaning
Anilox roll cleaning is critical for maintaining consistent print quality. As ink residues build up on the cells of the roll’s surface, they can clog the cells and impede the transfer of ink. This leads to uneven ink distribution, resulting in undesirable print defects such as streaks, color variations, and reduced image clarity. By cleaning anilox rolls regularly, printers can prevent these issues and achieve sharp, vibrant, and high-resolution prints.
Different Types of Anilox Roll Cleaners
Several methods and technologies are available for cleaning anilox rolls. The choice of cleaner depends on factors such as the type of ink used, the level of residue buildup, and the printing environment. Here are three common types of anilox roll cleaners:
- Brush Cleaners: Brush cleaners utilize rotating brushes to scrub the surface of the anilox rolls. They are effective for removing moderate ink deposits but may not be suitable for heavy accumulations. Brush cleaners are often manual or semi-automatic and require operators to perform the cleaning process.
- Ultrasonic Cleaners: Ultrasonic cleaners employ high-frequency sound waves to create microscopic bubbles in a cleaning solution. These bubbles implode near the surface of the anilox roll, dislodging ink residues. Ultrasonic cleaning is particularly useful for removing stubborn and hardened ink deposits, ensuring a thorough clean.
- Laser Cleaners: Laser cleaners utilize laser energy to vaporize ink residues from the anilox roll’s surface. This method is highly precise and effective, even for microscopic deposits. Laser cleaning is a non-contact process, minimizing the risk of damaging the roll’s surface. However, it requires specialized equipment and expertise.
Choosing the Right Anilox Roll Cleaner
When selecting an anilox roll cleaner, several factors should be considered to ensure optimal cleaning effectiveness, compatibility, and environmental impact.
- Considerations for Cleaning Effectiveness: The cleaner should be capable of removing ink residues effectively without damaging the roll’s surface. It should penetrate the cells and dislodge the deposits, restoring the roll’s ink metering capability.
- Compatibility with Different Ink Types: Different inks have varying compositions, including water-based, solvent-based, and UV-curable inks. The cleaner should be compatible with the specific ink type used in the printing process to achieve optimal cleaning results.
- Environmental Impact: With increasing environmental awareness, it is crucial to choose anilox roll cleaners that are environmentally friendly. Look for cleaners that are biodegradable, non-toxic, and free from harmful chemicals to minimize the ecological footprint.
Steps to Clean Anilox Rolls
Cleaning anilox rolls involves a systematic process to ensure thorough and effective removal of ink residues. Follow these steps for successful cleaning:
- Preparing the Cleaning Solution: Prepare the appropriate cleaning solution based on the type of cleaner being used. Some cleaners come with pre-mixed solutions, while others require dilution. Follow the manufacturer’s instructions for the correct cleaning solution concentration.
- Applying the Cleaner to the Rolls: Apply the cleaning solution evenly onto the surface of the anilox roll. Use a brush, spray, or other applicators as recommended by the cleaner’s instructions. Ensure that the solution covers the entire roll surface, including the cells.
- Scrubbing and Rinsing the Rolls: Depending on the cleaner’s instructions, scrub the roll’s surface gently using a brush, sponge, or other recommended tools. This helps to dislodge ink residues. Rinse the roll thoroughly with water or use a high-pressure cleaning system to remove loosened deposits.
Best Practices for Anilox Roll Cleaning
To maintain optimal print quality and prolong the lifespan of anilox rolls, follow these best practices:
- Regular Maintenance Schedule: Establish a regular cleaning and maintenance schedule for anilox rolls based on the printing volume and ink type. Regular cleaning prevents ink residues from accumulating excessively and becoming harder to remove.
- Proper Handling and Storage of Rolls: Handle anilox rolls with care to avoid damage to their surfaces. Avoid dropping or impacting the rolls during transportation or storage. Store them in a clean and dry environment, away from excessive heat or humidity.
- Monitoring and Inspection: Periodically inspect the anilox rolls for any signs of wear, damage, or excessive buildup of ink residues. Monitoring the condition of the rolls allows for timely cleaning or maintenance, reducing the risk of print defects and costly downtime.
Benefits of Using Anilox Roll Cleaners
The use of effective anilox roll cleaners offers several advantages for print quality, productivity, and cost savings:
- Improved Print Quality: Clean anilox rolls ensure consistent ink distribution, resulting in high-quality prints with vibrant colors, sharp images, and precise details. The absence of ink-related defects enhances the overall print appearance.
- Extended Roll Lifespan: Regular cleaning prevents the accumulation of hardened ink residues, which can cause long-term damage to the roll’s surface. By extending the roll’s lifespan, printers can avoid frequent replacements, saving costs in the long run.
- Reduced Downtime and Costs: Clean anilox rolls minimize the occurrence of print defects, reducing the need for reprints and the associated costs. Additionally, preventive maintenance and regular cleaning can help avoid unplanned downtime caused by roll-related issues.
Conclusion
Maintaining clean anilox rolls is crucial for achieving optimum print quality in flexographic and gravure printing. By choosing the right anilox roll cleaner, following proper cleaning techniques, and implementing best practices, printers can ensure consistent and vibrant prints while prolonging the lifespan of their anilox rolls. Regular cleaning, monitoring, and adherence to maintenance schedules are essential for long-term success and cost savings in the printing industry.
FAQs
- How often should I clean my anilox rolls? The frequency of cleaning depends on various factors, including ink type, printing volume, and environmental conditions. It is recommended to establish a regular cleaning schedule based on these factors to prevent excessive buildup of ink residues.
- Can I use regular cleaning agents for anilox roll cleaning? It is not advisable to use regular cleaning agents as they may not effectively remove ink residues from the microscopic cells of anilox rolls. Specialized anilox roll cleaners formulated for this purpose provide more effective and thorough cleaning.
- What safety precautions should I take when using anilox roll cleaners? Follow the manufacturer’s instructions and safety guidelines when using anilox roll cleaners. Wear appropriate protective gear such as gloves and goggles. Ensure proper ventilation in the cleaning area, especially when using cleaners with strong odors or fumes.
- Is it necessary to use different cleaners for water-based and solvent-based inks? Yes, different inks have different compositions, and their residues may require specific cleaning agents for effective removal. Consult the manufacturer’s recommendations or seek expert advice to choose the right cleaner for the ink type used.
- Can anilox roll cleaners remove stubborn ink deposits? Yes, anilox roll cleaners, particularly ultrasonic cleaners and laser cleaners, are designed to remove even stubborn and hardened ink deposits. These advanced cleaning methods offer a high level of precision and effectiveness in restoring the roll’s cleanliness.
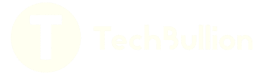