Whether it’s about the preparation of inductors, transformers, electromagnets, or medical sensors, micro-coils are the essential components of these devices. Where there is an interaction between the magnetic field and electric current, you will find the applications of electromagnetic coils or micro-coils. The magnetic field and the electric current interact with each other in two different ways- i) when an electric current passes through an electric conductor, it can generate a magnetic field, ii) on the other hand, when an external magnetic field passes through the inner surface of an electromagnetic coil, it generates an electric current.
The winding process is a major part of the micro-coil preparation process and in this process, the manufacturers shape the wire into a coil, spiral, or helix. Manufacturers provide different dimensions and shapes to the micro-coils depending on the purpose of use. Required resistance, magnetic field strength, and inductance are some crucial parameters to influence the shape and size of the coils. Apart from the difference in tiny shape, the micro-coils are quite similar to the regular coils. Manufacturing of the micro-coils involves magnifying glass or microscope due to the tiny size of the micro-coils.
Miniaturized Size Challenges:
Manufacturers need to fit the micro-coils into the small medical devices or other devices and this physical size constraint is the main challenge for the manufacturers. In order to get rid of this size constraint, the need for manufacturing tiny micro-coils is increasing. The necessity to prepare the micro-coils of a smaller cross-sectional area than a needle is rising in order to fulfill the requirement of microscopic parts for the transducers and sensors.
Manufacturing Challenges:
The micro-coils should be manufactured with ultra-fine wires of less than nine microns in diameter to maintain the tiny size of the coils. Therefore, manufacturers need to wind and connect the ultra-fine wires and these processes are challenging.
How to Connect Two Ultra-Fine Wires?
You can not be able to connect and wind the ultra-fine wires with the help of traditional methods. Modern manufacturers mostly use thermal compression bonding technology for connecting two ultra-fine wires. Whether the two wires are of similar material and diameter or of different material and diameter, this technology is useful for both cases. You can highly rely on this technology to have strain-free and corrosion-free connections and to ensure the longevity of the coil. Therefore, when it comes to the preparation of disposable products or long-life products, such as medical implants, thermo-compression bonding technology is the most suitable and efficient technology.
How to Wind Two Ultra-Fine Wires?
Through the micro-coil winding process, manufacturers twist the ultra-fine wires or other electrical conductors around a core so that it produces the shape of a helix, spiral, or coil. However, the manufacturers should use the built-in-house winding machinery to offer tight tolerances and quality standards to the micro-coils.
Applications:
Among multiple applications, the major applications of the micro-coils are in the electronics and medical field, such as deep brain stimulation components, pain management devices, electricity-based ablations, pace-makers, orientation and navigation sensors, electrophysiology treatments, dental and orthopedic treatments.
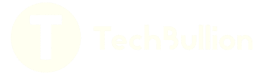