In recent times, CNC aluminum machining services have enabled customers to purchase pre-engineered products quickly and cost-effectively. Furthermore, the use of CNC (Computer Numerical Control) enables consumers to make an order of parts that are designed with precision. Due to its superb characteristics in machining, aluminum is one of the most widely employed metals by many businesses, including automotive and major industrial machinery manufacturing.
For more in-depth information you should view from Aluminum CNC Machining Service – ETCN
What is Aluminum CNC Machining Service?
Understanding the CNC Machining Process
The CNC aluminum machining process employs the use of CNC automations in the manufacture of components out of aluminum alloys. The first step in this manufacturing practice is preparing a computer-aided design (CAD); this blueprint is subsequently transformed into G-code. This transformation is essential because it provides the CNC machines with explicit instruction on how to operate when molding aluminum alloys for particular end products. In addition, while adhering to strict ratio parameters and tolerances, these machines greatly minimize the amount of time necessary to create intricate components as opposed to traditional methods.
View Aluminum CNC Machining Service – ETCN for More Details
Advantages of Using Aluminum in CNC Machining Processes
Aluminum remains one of the most common materials in CNC machining owing to the unique characteristics it has. It has low density which makes it more suitable for usage in conditions where reduction of weight is important. At the same time, aluminum has excellent corrosion resistance properties which increase the durability of the machined parts. Aluminum alloy can be shaped to any form with a high level of accuracy and even finer details making it appropriate for use in both prototypes and mass production components. Also, because aluminum has good thermal and electrical properties, it finds many uses in dissipaters and other electronic parts, widening the range of custom CNC machining capabilities greatly.
Typical Uses of Aluminum in CNC Machining Services
The nature of aluminum machining services is wide ranging, hence its application in various fields. In the aerospace sector, parts made out of aluminum are critical in the manufacture of light weight aircraft structures that assist in lowering fuel burn and improving efficiencies of the aircraft. Apart from this, aluminum is widely used in the manufacture of engine parts and body panels in the automotive sector which add strength and decreases the weight of the vehicle. Furthermore, aluminum is utilized by electronic industries in the production of heat sinks and casings due to its good thermal features. Other industries for example medical devices and consumer products as well leverage the aluminum CNC machining services due to accuracy and efficiency it brings.
How Step by Step Aluminum CNC machining takes place?
CNC Machining of aluminum involves different stages that can be divided into a few key components. To start with, the designs of the parts to be manufactured are fully committed into a CAD program whence the designs are to be altered to create a G code language that will be understood by the machines. There are several steps that follow, which include hardening the blocks, choosing cutting tools and the setup of the CNC machine. As soon as the machine gets set up, relevant programs are uploaded which control how the machining will take place, all other milling materials and operations are done to achieve the end product. Lastly, the tests to define the quality of the finished manufactured elements of aluminum are performed to check whether the established parameters are satisfied.
Different Types of CNC Machines Used for Aluminum
CNC machining has a number of methods of working with aluminum and a few aluminum CNC machine tools serve various purposes. For example, a CNC mill is among the most common machines which is equipped with rotating cutting tools and is designed to remove material from a workpiece. More complex shapes can be made using 5 axis CNC machines because they can be used to machine many dimensions at once. In terms of CNC turning, CNC lathes cut cylindrical shapes by spinning the workpiece against a cutting tool that is held still. Each type of CNC machine works effectively in making precision aluminum parts according to the specification of the engineering designs for different machining projects.
Factors Affecting CNC Machining Capabilities
There are a number of factors that affect aluminum CNC machining services when working with aluminum. The causal relationship between the aluminum material properties and the selection of cutting tools is important since every material may call for a certain geometry and coating of a tool. The quality of the finished parts, especially the surface finish and machining efficiency, will depend on the feed rate and spindle speed. What is more, the kind of aluminum alloy selected will affect the machining process where harder alloys have a tougher working environment. If custom aluminum machining is to give the desired results, it is relevant to consider these factors.
What Are the Different Types of Aluminum Alloys Used in CNC Machining?
Aluminum 6061 vs. 7075 vs. 5052
CNC machining is one of the most important manufacturing processes for modern diverse industrial businesses. Most industries still rely on aluminum alloys because of their unique properties, and these alloys are further classified depending on their unique properties. For instance, Aluminum 6061, Aluminum 7075, and Aluminum 5052 alloys are three of the most commonly used alloys during CNC machining. While discussing aluminum alloys and their applications, the use of Aluminum 6061 becomes essential as this alloy is used for its corrosion resistance and other mechanical properties to produce a wide range of industrial components. Aluminum 7075, on the other hand, has a fair amount of strengths, which means it’s perfect for parts of aircraft when strength is crucial. Lastly, marine components are mostly made of Aluminum 5052, which has excellent strength to weight ratio and is easy to weld and cast. Each alloy possess distinct characteristics which makes it fit to be used in machining for specific projects thus they have to be carefully selected based on the requirement of the application.
Selecting the Right Aluminum Alloy for the Work
When considering the welding or machining of an aluminum alloy, it is important to select the aluminium alloy carefully. Different aluminium alloys would serve different purposes thus it is vital to select the right aluminum alloy. Such considerations would include strength, exposure and environment and how the parts are designed. In situations where strong and light components are required, then Aluminum 7075 would be recommended. On the other hand, if corrosion resistance is more to focus point then aluminum 5052 would be appropriate. There are several machining service providers who can provide valuable information and advice which is essential to the aluminium project.
Qualities of Aluminum Alloys in Cnc Machining
Aluminium alloys have distinct features that determine how effective they will perform on the CNC machining process. The ability for aluminum to be thick or cut down into an alloy is different each time because each alloy is made differently. This aluminum 6061 is also good for machining as detailed and tight fittings may be required. In such cases, stronger aluminum alloys such as 7075 might need special cutting techniques and tools in order to achieve the desired effect. Machining also causes heat to build up which is dissipated by the aluminum alloys which further reacted with the tooling of the part, thus impacting quality. That is why it is vital to understand these features in order for AMDUL to successfully complete aluminum projects.
Which Steps Should One Take in Invoking an Marshall CNC Machining Service for Instant PricingQuote.
Which Steps Should One Follow in Making Orders for Custom Aluminum Through CNC Machining Service Providers.
Getting an instant pricing quote from a CNC machining service firm is made likely possible due to improvement in technology. This is achieved after submitting the CAD design files to the machine service provider. Most systems have instant estimating systems which allow users to get an estimate of how much the cost will be based on the designing parameters that the users have filled in. Usually, this duration does not exceed five minutes giving the client the necessary answer to how much the product goes for and the time it is likely to take for delivery. After being given a price quote, an order may be completed with custom instructions about the intended machining project or after the desired requirements are added.
What Kind of Information Should Be Given While Placing Order for CNC Machined Parts?
In terms of placing the CNC machined parts ordering in the most effective way possible, then certain information will need to be provided for it to be smooth. This includes detailed CAD drawings of the custom parts in terms of height, length, width, tolerances and even the surface finishes needed. As well as it is equally important to mention what type of aluminum alloy goes with the project or whether a CNC milling or CNC turning will be employed. Providing all this information during the initial interaction makes sure that those who provide machining services are not only able to quote but also able to manufacture parts that meet the given dimensional parameters and specifications.
A Guide to Production Lead Times and Scheduling
For instance, CNC machining lead times generally depend upon the parts’ complexity, the number of components required, and available capacity at the machining center. Generally, custom aluminum parts have a lead time of days which makes CNC machining effective for companies which require quick prototyping or parts in bulk. It is important to note the production schedule and estimated lead times for the purpose of planning the project and controlling inventory. This can also facilitate the communication and engagement with the sourcing machining service provider in order to understand and maintain deadlines.
What Are the Common FAQs About CNC Aluminum Parts Fabrication Services?
What Is the Fundamental Difference Between CNC Turning And CNC Milling?
Turning and milling are two distinct operations in CNC machining, in this case, Optical Lens that play different roles, however both are corporeal in aluminum CNC machining. CNC Turning involves the rotary motion of the raw material while it is being held by a polar shaft which has a fixed place, the tool that cuts raw aluminum and forms cylindrical shapes. On the other hand, CNC milling machines cut and shape materials using rotary tools. Deputized to perform a wide variety of tasks, the tools can create features ranging from holes and grooves to complex three-dimensional shapes. These differences should also be well appreciated when one is making the choice as to what machining process should be followed based on the geometry of the part to be manufactured.
How do you achieve quality in CNC machined products?
The preparation of the constituent parts with a view to using them in assembling CNC machined products would comprise of effectively controlled machining processes and proper quality control. Good cutting tools and good machining conditions is an effective step towards enhancing the accuracy and finish of a part. Other processes that could be employed include inspection where dimensional and surface roughness measurements are done during and after machining to find whether there has been any deviation from the specifications. Finding high precision CNC machining service providers to manufacture aluminum machined parts can give the desired low-cost assurance of its products being made to a high-end quality standard.
How Much Does It Cost To Use CNC Machining Services?
There are instances where part costs may only be marginally warped due to the design’s complexity, the aluminum alloy in utilization, that is, the specific part, and the times its required. As a rule of thumb, the lower the order the more complex the order, therefore, the complexity of the part further pushes the cost upwards. Furthermore, we have pricing for aluminum alloys which are also factors. CNC machining services are recommended to provide at least three different bids in processing in order to better understand the value for money brought to the machining project you are working on.
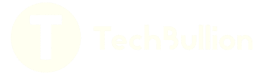