This article describes the methods, tools, environments, and challenges related to aluminum cnc machining and its typical alloys. It focuses on aluminum properties, the usual alloys used in machining, and their applications in different fields.
In particular, aluminum is a second metal used more frequently than other materials apart from steel. The high demand for aluminum is because of its due tong characteristics, and machining and ease of machiningtal, aluminum is relatively low dense, malleable, easily formed, nonmagnetic, lustrous, and silvery-white. Aluminum is usually alloyed with elements like manganese, copper, and magnesium with improved characteristics.
Benefits of Aluminum CNC Machining
Typically, custom CNC aluminum features the following benefits.
Strength-to-Weight Ratio
Aluminum is about one-third the density of steel. Even with low density, it features high tensile strength, making it ideal for automobile and aircraft industries.
Machinability
Aluminum alloys are easy to machine compared to other types of metals. They are also machined fast and with minimum power supply. Because they are relatively soft hence reducing the costs of machining and power. This machining ability avoids deformation and guarantees precise tolerances.
Corrosion Resistance
Aluminum has a natural corrosion resistance in different conditions. Anodizing further enhances this resistance. The majority of the used aluminum grades possess high protection against corrosion and, thus can be used in various applications.
Electrical Conductivity
Aluminum, the purest form, has a conductivity of electric current of 37.7 x 106 S/m at 20 degree Celsius. Aluminum alloys have low conductivity. However, they remain suitable for electrical applications when high conductivity is not critical.
Custom Finishing
Aluminum machined components can be anodized, powder coated, or painted to suit project requirements.
Recyclability
Aluminum is recognized as a recyclable material as the process costs low energy and is cheap. This property not only minimizes wastage but also assists manufacturers in making an effort to regain their costs while encouraging sustainable practices.
Common Grades of Aluminum For CNC Machining
A table with key features and specific applications for various aluminum grades used in aluminum cnc machining is given below:
Series | Alloying Element | Key Features | Common Applications |
1000 | 99% or higher aluminum | Excellent corrosion resistance and thermal conductivity; highly ductile. | Electrical connectors, heat sinks, and chemical equipment. |
2000 | Copper | High strength-to-weight ratio; good machinability; reduced corrosion resistance. | Aircraft fuselage, aerospace components, and truck body frames. |
3000 | Manganese | Good workability and moderate strength; excellent formability. | Beverage cans, cooking utensils, and roofing sheets. |
4000 | Silicon | Low expansion; excellent wear resistance; suitable for welding. | Automotive engine components, welding wires, and die-casting molds. |
5000 | Magnesium | Superior corrosion resistance; good weldability; and excellent fatigue strength. | Marine environments (boat hulls), pressure vessels, and tankers. |
6000 | Magnesium & Silicon | Good corrosion resistance and medium strength; versatile machining properties. | Structural components, automotive chassis, and architectural applications. |
7000 | Zinc | High strength; often used in heat-treated forms; lower corrosion resistance. | Sports equipment (bicycles, baseball bats), military aircraft, and high-stress components. |
Design Tools for CNC Milling Aluminum
Choosing the appropriate tool for machining aluminum through Computer Numerical Control is a question of certain important factors.
Tool Design
Tool geometry plays an important role in machining performance. The number of flutes is a crucial design factor. Cutting tools intended for aluminum should have 2-3 flutes for efficient chip removal at high spindle speeds. An increased number of flutes can cause thinner chip valleys, and large aluminum chips can be trapped. Employ 2 flutes, when cutting forces are minimum, and chip clearance is crucial. To achieve a good compromise between the chip clearance and the tool strength, 3 flutes are recommended.
Helix Angle
Helix Angle
The helix angle is defined as an angle made between the tool centerline and a normal to the cutting edge. This angle has a significant contribution to the cutting performance. The helix angle of greater value provides great chip removal but increases the friction and heat. There’s a possibility of having the weld between the chip and tool surface during the high-speed cutting operation. While smaller helix angles may lower heat. They may also decrease chip removal effectiveness. In aluminum machining, the helix angle recommended for use when performing roughing operations is 35° to 40° while for finishing 45° is appropriate.
Clearance Angle
The clearance angle is critical to the functionality of a tool. Excessive clearance can cause the tool to dig into the workpiece. This may lead to chatter during machining. On the other hand, the angle of approach may be so small that it leads to unnecessary friction. The clearance angles should range between 6° and 10° for aluminum parts in CNC machining.
Tool Material
Carbide is more frequently used than any other material in cutting tools for aluminum machining. As aluminum is a relatively soft material, the key factor should be to have a sharp cutting edge rather than a hard one. The ability of carbide tools to maintain an edge is determined by grain size and binder ratio. These latter characteristics relate to grain size, where large grain sizes produce hard materials but small grains result in toughness and impact strength – both desirable in machining applications. The cobalt content in carbide should be controlled at 2-20%, to avoid negative interactions with aluminum at elevated temperatures.
Tool coating
Tool Coating
Tool coating also improves cutting performance. Protection for aluminum machining entails using Zirconium Nitride (ZrN), Titanium Diboride (TiB2), and diamond-like coatings.
Feeds and Speeds
Feed rate refers to the travel amount of a workpiece or a tool translated in a given revolution. This feed rate depends on the required surface finish, strength, and stiffness of the workpiece. The feed rate for the rough cut is between 0.15 to 2.03 mm/rev corresponding to the finishing cut of 0.05 to 0.15 mm/rev.
Cutting Fluid
Aluminum, although easily machined, should not be fabricated without coolant. This can lead to a built-up edge on the tool. There are soluble oil emulsions and mineral oils as the cutting fluids for aluminum machining. Do not use water with chlorine or active sulfur as this tends to stain aluminum.
Uses of Machined Aluminum Parts
Aluminum on its own is a great material, and when properly alloyed, it adds more to the material’s flexibility. Here are key industries that benefit from aluminum CNC machining.
Aerospace
Aluminum’s low density allows it to be used in critical places like landing gear and torque links which increases aircraft efficiency.
Automotive
The automotive industry is increasing its demand for aluminum. It’s used in parts like electric vehicle castings, engine parts, and body panels leading to improved fuel efficiency and performance.
Electrical
For electrical conductivity, aluminum is highly appreciated. In general, it’s used in machined aluminum parts such as PCB housing and smartphone frames for proper functionality.
Drug and Food Manufacturing
Aluminum is safe to use in the pharma and food industries because it’s a non-reactional material. It’s widely employed in food processing machinery, instruments, and medical equipment.
Consumer Electronics
In the field of consumer electronics aluminum’s heat dissipation properties make it ideal for heat sinks where it dissipates heat from different gadgets to evaluate ultimate performance.
Steel Versus Aluminum CNC Machining
Aluminum and steel are the most adopted in CNC Machining Service.
Let’s identify five criteria that influence the selection of the right material.
Cost
Carbon and mild steel are cheaper than aluminum in most cases. Stainless steel is normally more expensive than the two mentioned above. The metal prices are highly sensitive to the world market requirements of the specific category. Both initial costs and the long-term durability of the material selection should also be focused.
Weight
Aluminum is lighter than steel; it is about 2 to 3 times lighter than steel. Manufacturers are inclined to use lighter materials in their products to improve performance. This trend results in replacing some steel components with aluminum counterparts.
Strength
Steel’s density makes it more durable than aluminum. Although, steel does not bend when exposed to heat or when pressure is applied to it. Still, aluminum is much more vulnerable to such defects as scratches and dents in comparison with steel.
Machinability
Aluminum is easier to machine because it is lighter than steel and normally takes less time to machine. It cools faster than steel, thus the machining cycle is short, saving time and cost. Lower coolant volumes are also required for the aluminum parts processing.
Post-Finishing Techniques For Custom CNC Aluminum Milling
- Bead Blasting
- Sand Blasting
- Coating
- Anodizing
- Powder Coating
- Heat Treatment
Limitations of Aluminum CNC Machining
- Scratch Vulnerability: Aluminium surfaces are susceptible to scratching. This may in turn make some parts of an object less visually appealing.
- Lower Strength: Aluminum is not as strong as steel in general. This puts its use in high-stress applications in a compromise.
- Galvanic Corrosion Risk: Aluminum is an easily corroded metal and should not be in contact with dissimilar metals. This is especially true in electrolytic conditions like seawater.
- Machinability Issues: Aluminum is relatively soft and hard to machine. There may also be problems in obtaining high precision, especially within close tolerances.
Final Thoughts
Aluminum CNC Machining is a common process of fabricating unique products due to the outstanding characteristics of aluminum alloys. These alloys build on aluminum’s inherent properties, so CNC machining is a perfect fit for a wide range of uses.
In this guide, the most popular aluminum grades used in CNC machining are explained. However, to make the best use of aluminum, it’s crucial to understand the basic process of CNC aluminum machining and choose a reliable aluminum cnc service for your project.
Read More From Techbullion
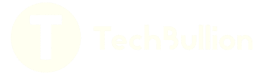