There’s no room for failures or malfunctions in the automotive industry. That’s why carmakers are incredibly demanding regarding the parts they use in their vehicles.
In this context, becoming a global leader in fastening solutions for automakers is by no means an accident. Agrati produces fasteners for more than 40 million vehicles around the world. Unsurprisingly, it became the prime option for carmakers, OEMs, and Tier 1 clients.
Here’s how Agrati’s fasteners hold your vehicle together, even in the most testing situations.
Built to Last
Agrati has a wide portfolio of nuts, high-strength bolts, licenced screws, and components with complex geometry. The company uses cold forging technologies and heat treatments to create extremely resistant screws. These fasteners are used pretty much everywhere around the vehicle: seats, bodies, chassis, powertrains, batteries, and safety systems.
Agrati’s production line relies on cutting-edge technologies to deliver excellence at every turn. In fact, most of the processes involved in production, such as wire drawing, tooling, and different forging techniques, are handled inside the factory. It ensures not only quality but also a high level of customisation of each component. The company’s daily production of screws and bolts is massive, putting out over 5 million parts.
Agrati is also famous for its portfolio of weld, cage, and single nuts, which produce over 2 million parts monthly. More impressive still is the quality standard of these parts: zero defects. It makes a huge difference for any vehicle’s safety, as these nuts are used on braking systems, shocks, and chassis.
Undoubtedly, Agrati goes the extra mile for its Tier 1 and OEM customers. All items, including cups, flat washers, and wheel nuts, have features that speed up assembly in the production line. Bolts and screws are forged using cold forging techniques that improve their performance in different situations, plus anti-unscrewing features that enhance safety.
Special and Exclusive Solutions
Agrati’s products can be enhanced on-demand with special coatings, co-moulding, plastic, and hybrid metal-plastic parts. The licenced screws has superior friction coefficient, corrosion resistance, and self-locking features. They’re also lighter than most screws but provide the same level of safety and reliability.
Naturally, an innovative company like Agrati also has patent solutions that clients won’t find anywhere else. The Panoplast, for instance, is a plastic screw that combines features from PT screws and Plastite. Ring-collar screws are also plastic-based.
They can come with different coatings and allow for automated assembly. Screws with captive sleeves are made with cold forging. The low-carbon steel sleeve is also cold-forged, providing superior strength and resistance.
Infrastructure
Agrati invests heavily and wisely in its infrastructure. What started as a garage factory with only 20 employees now has 12 production plants on three continents, five logistic centres, and a workforce of over 2,400 professionals. Additionally, it invests 8% of its revenue in Technology and Innovation, ensuring that this 85-year-old company will never stop and keep innovating as time passes.
Agrati’s infrastructure is large enough to produce 8 billion fasteners yearly while creating 850 new parts. Such large productivity requires more than 160,000 tons of steel and an incredibly efficient distribution system. Agrati has also made its own tooling company, Attrezerie Asda, which provides tooling for all plants.
Clients from the automotive sector can also take advantage of Agrati know how. The Co-Design service uses a dedicated team and the company’s best resources to collaborate on the development of bespoke solutions. The service includes access to the best labs in the industry, as well as professionals who can turn blueprints into licensed and validated components.
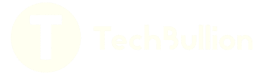