Warehousing environments are becoming more and more challenging. The main reason is fairly straightforward: unprecedented volumes of global trade have made warehouses busier than ever. Other reasons are not quite so obvious. For one thing, warehouse real estate has become increasingly more expensive in many regions, forcing businesses to make do with smaller warehouses with tighter spaces. A lot of older equipment also continues to be used, further slowing down potential throughput as warehouses become busier.
Fortunately, a few strategic upgrades can help struggling warehouses enjoy better performance without businesses needing to spend on expensive real estate investments. Look through these options to boost material flow, efficiency, and scalability in your warehouse.
- Move More with Tow Trucks
Tow trucks, or tow tractors, are one of the most effective ways to move large volumes of materials across warehouse floors or between designated stockpile zones. Rather than moving single loads, these machines pull multiple trolleys or trailers in one trip, reducing the need for multiple trips by forklifts and minimising inefficient manual handling. This means less fuel or energy used per unit of merchandise moved and fewer opportunities for traffic snarls and accidents.
Tow tractorss higher hauling potential also makes them particularly well-suited for just-in-time or batch-picking operations. Electric and internal combustion engine (ICE) models are also available, making these machines viable in a variety of operational scenarios.
- Hybrid or Electric Machinery for Cleaner, Safer Operations
Heavy machinery is a necessary investment for many warehouses, but the noise and air pollution produced by traditional ICE models can impact safety and reduce their usefulness for handling sensitive items. New electric models offer low-noise operation and no emissions, making them ideal for use in indoor environments.
If your team frequently moves palletised goods over medium distances, switching to electric or hybrid machinery will save time and lower long-term health risks. Operators may also be less fatigued when using these newer forklifts, minimising the chances of mistakes during long shifts. Some advanced models even come with smart diagnostics and other features that further enhance productivity and energy efficiency.
- Ergonomic Vehicles, Lift Tables, and Workbenches
Ergonomic equipment offers multiple advantages over less human-centric designs. First, it’s significantly easier to onboard new staff if the equipment they use is intuitively designed. Next, ergonomic design speeds up the time it takes to safely complete picking, packing, assembly, and other warehousing activities, making them more efficient. Lastly, these improvements also avoid fatigue and repetitive stress injuries, keeping workers healthy and avoiding insurance and healthcare costs.
- Fleet Management Software and Sensors
Fleet management software and integrated sensors can collect real-time data across an entire warehousing operation, enabling consistently optimised workflows and reduced idle times. They can also be set up to optimise employee rosters and predict equipment maintenance needs before issues occur. If your warehouse needs to add shifts, invest in new equipment, or handle extra volume, these updates are a must-have.
- Conveyor Belt Systems
While more often seen in manufacturing operations, conveyor belt systems also offer plenty of utility for warehouses, streamlining the flow of materials between picking, sorting, and packing zones. Conveyor belt systems run the gamut from simple setups just meant for moving items between zones to smart systems capable of tracking and sorting items automatically. Regardless of type, conveyors cut labour time as well as the risk of product damage, making them key to faster and more accurate order fulfilment.
- High-Capacity Racking
In many older facilities, rack storage is effectively limited to a certain height due to safety and technical concerns. If a larger warehouse is out of the question, upgrading your racking system to accommodate higher stacking effectively multiplies usable floor space. Pairing this upgrade with equipment like narrow-aisle forklifts allows you to take full advantage of vertical storage without sacrificing speed, access, or worker safety.
- Automated Storage and Retrieval Systems (AS/RS)
These game-changing systems are a step above typical high-capacity racks, integrating robotics and software to store and retrieve goods with precision and speed. They dramatically reduce the need for human pickers to access goods on higher racks and allow for the total maximisation of available vertical space.
Lay the Groundwork for Smarter Warehousing, One Step at a Time
While most of these updates require time to implement, they can significantly improve throughput and inject resilience into your warehousing operations. With labour and real estate costs expected to continue rising amidst record global trade volumes, it would be wise to consider the benefits these tech updates bring to the table.
Once you’re ready to modernise your warehouse, start engaging with your floor managers to find out which updates they really need. Check how their current pain points relate to your growth goals and begin prioritising the upgrades that best fit with everyone’s needs. While you don’t have to do all the recommended fixes at once, acting today will help keep your warehousing operations from being overwhelmed tomorrow.
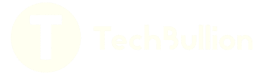