Workplace accidents are fairly common, but they can be far more serious overall as there tend to be more risks in workplaces. Employees work in dangerous conditions and circumstances, especially those working in the construction and industrial sectors, dealing with heavy machinery and chemicals.
Businesses need to take the proper safety measures for preventing accidents and be prepared for when they occur.
Here are some of the most common injuries at the workplace, and the reasons why they occur.
Slips, Trips, and Falls
Slips and trips are the most common injury to occur in workplaces across the US and UK. The UK’s Health and Safety Executive (HSE) shows that 33% of workplace injuries are slips and trips. Comparatively, slips and trips account for 27% of workplace accidents in the US.
The causes for slips and trips that significantly increase the risk of an accident occurring are mostly an oversight of the safety rules and regulations. Slips and trips from slippery surfaces, wet floors, or even falling from heights can fall into this category.
In a construction setting, for example, obstructions alongside walkways can cause people to trip and fall, resulting in fatal and nonfatal injuries. Scaffoldings also rely on safety harnesses and other equipment to mitigate the risk of using them, and ignoring these rules can result in serious accidents.
Musculoskeletal Disorders (MSDs)
Musculoskeletal Disorders, or MSDs, not only affect an individual’s ability to work, but can also have significant and negative effects outside of the workplace as well. As these disorders can potentially limit a person’s mobility and physical ability, they can even result in the individual relying on assisted living arrangements.
MSDs are especially prevalent in manual labor-intensive tasks, but can also occur in sedentary, office-based work. As MSDs are mostly caused by excessive physical strain, stretching of the muscles, bad posture, and heavy lifting, avoiding MSDs is extremely dependent on the job itself and the employer’s policies.
As regular muscle strains and stretches are a clear risk, avoiding them is the issue. However, the duty falls to the employer to ensure that the employees have all the tools, practices, and policies to prevent the development of MSDs.
One particular thing of note here is that MSDs can also be developed from a bad posture when sitting, or by not using electronic equipment with the proper safety protocols. These might seem like trivial factors to both employers and employees, but they can lead to serious long-term ill health later on for workers. Musculoskeletal disorders affect more than 1.7 billion people across the globe, both workers and non-workers, according to the World Health Organization (WHO).
As a general rule, any work with a high-risk potential should be avoided unless necessary.
Falling Objects
In a construction site, a falling object could be a brick or a steel beam. In an office environment, a falling object can be a binder or a stack of files. In a warehouse, a falling object could be a heavily stored item.
All three of these instances are dangerous and should be treated seriously. These can range from a mild gash to a broken bone or even severe, or permanent injury that can leave a worker disabled.
In certain areas with overhead work or storage, such as construction sites or warehouses, hard hats are a minimum safety requirement, along with proper shelving, safety nets, and protective awnings against falling objects if applicable.
Vehicle Accidents
Workplace vehicle accidents can be for employees traveling for work, meaning they are within the general traffic, or more specialized heavy vehicles, such as trucks, forklifts, and flatbeds.
For workers traveling for work, promoting traffic safety and safe driving within the company has a positive effect, according to a document published by OSHA and other institutions.
Workplace traffic accidents are the leading cause of worker fatalities in the US, accounting for almost 37% of worker deaths across all US workplaces.
Most vehicle accidents are preventable and require safety from the driver on the road, and all personnel in a workplace, such as with a truck or a forklift.
Hazardous and Toxic Substances
Chemicals and other hazardous substances require the utmost precautions and safety measures to work with, especially when the material is highly toxic and can lead to serious health consequences. Employers need to provide proper safety equipment for these tasks as well as practice certain precautions, such as:
- Personal Protective Equipment (PPE)
- Safety goggles
- Proper storage for chemicals and toxic substances
- Isolation from other non-harmful materials
- Proper ventilation for storage areas with hazardous substances
- Enhanced fire-resistant shelving, storage compartments, and more
When it comes to these dangerous substances, employers need to ensure that accidents do not lead to anything worse. A flammable chemical, for example, should not be stored near an ignition source that can produce a flame, and proper fire protection and prevention equipment should always be nearby.
Other Things Worth Noting
Accidents happen, but that does not mean they always have to happen. Most accidents are preventable, and workplace accidents not only have the consequences of having to deal with injuries and lost time but also can have the employer liable for much more.
That is why training is so important, as well as being informed about the various accident and their causes. Most accidents can be prevented with better risk-averse strategies, such as providing manual handling training for blue-collar jobs and focusing on posture training for office-based work.
Other vital training courses include COSHH training, slips, trips, and falls training, vehicle training, lifting operations training, and other relevant courses.
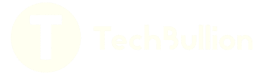