CNC or computer numerical control machines offer accurate, repeatable processes to create prototypes and allow production runs for parts. Using pre-programmed instructions and special tooling, these machines cut solid pieces of material into usable parts. It’s a versatile process, which makes it perfect for a range of applications. While it’s adaptable, users must start with the proper materials for every job. Here, we’ll delve into the usage and selection of materials for CNC projects.
Choosing Materials
It’s often tough to choose the right materials for a project, especially for those new to the world of CNC. To ensure that the materials suit the project, read full guide here and follow these steps.
- Determine material requirements. The selection of CNC materials starts with an assessment of the project’s requirements. Think of factors like part sizes, environmental conditions, mechanical properties, budgets, and cosmetic preferences when choosing materials for a CNC project.
- Make a short list. Once the project’s material requirements have been defined, narrow the field to a few materials that are most likely to meet those needs.
- Choose the best material for the project. After making a short list of likely candidates, it’s time to make some decisions. It’s rare to find a material that meets every requirement, so some compromises may need to be made.
Now that we’ve given a few tips on material selection, let’s go over some of the most common materials used in CNC fabrication.
Common Materials Used for CNC Machining
Choosing materials for a machining project is a challenging process, and it may help to seek expert advice. CNC specialists understand these projects and their requirements, so they’re able to suggest the best materials for optimal results.
Some materials commonly used in CNC fabrication include:
- Aluminum. Aluminum is a versatile and cost-effective material that’s easy to machine, which makes it ideal for a range of projects. With its superior weight-to-strength ratio, aluminum is much simpler and faster to machine parts from than some other materials. Although it’s not as strong as steel, anodizing adds a protective, strengthening layer.
- Brass. Because of its polished good looks that imitate those of gold, brass is often used in architectural applications. Its low strength and high stability make it a popular choice for CNC machining, while its heat conductivity lends itself to low-friction applications.
- Copper. Known as one of the world’s best electrical conductors, copper is ideal for heat exchangers and automotive applications. It’s highly resistant to corrosion, and its conductivity makes it easy to shape during the machining process.
- Carbon steel. Regarded as a mild grade, carbon steel is tougher, stronger, and less expensive than stainless steel. It’s easy to weld and machine, making it a common choice in applications requiring durability and strength. When carbon steel is heat treated, its hardness increases.
- Nickel. Machining nickel can be tough, as its strength offers resistance, and its other properties produce enormous heat when the metal is cut. Nickel is a desirable material, however, because it is strong and corrosion resistant.
- Titanium. With its high melting point, titanium is often used in the medical and aerospace industries. This light but strong metal conducts heat well, and its resistance to corrosion protects it from water and salt.
- Stainless steel. Available in numerous grades, stainless steel offers high strength, resistance to wear and corrosion, and excellent ductility. It’s easy to machine, weld, and polish stainless steel, which makes the metal a popular choice for automotive and aerospace applications.
Get Expert Advice
This list is by no means exhaustive, but it shows the versatility of the CNC manufacturing process. With an in-depth evaluation of project requirements, users can choose the best materials for their chosen parts while striking a balance between time, quality, and cost. With trusted help from Machinist Guides, fabricators can increase their chances of success.
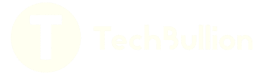