Workplace safety remains a critical issue in Australia today. Australian workplaces recorded numerous fatalities in 2022, with transport and warehousing sectors showing higher injury rates than national averages. In warehouse environments, a properly certified forklift safety cage is essential for protecting workers during elevated work.
Worker safety and company productivity face substantial risks from hazards like slips, falls, and machinery accidents. Work-related injuries and illnesses create significant costs for Australian businesses through medical expenses, lost productivity, and workers’ compensation claims. These impacts underscore the vital importance of maintaining safe work practices across warehouses and construction sites.
This guide outlines essential information about safety measures, workplace hazards, and strategies to create a safer work environment in Australia. You’ll learn how to implement safety protocols that protect your workers while maintaining operational efficiency, all while ensuring compliance with Work Health and Safety (WHS) regulations.
Common Safety Hazards in Work Sites
Safety at work needs constant focus due to many hazards in warehouses and construction sites. Forklifts cause between 35,000 and 62,000 injuries every year. This is a big deal as it means that mechanical hazards are a major risk. Moving vehicles and objects also create ongoing dangers that need strict traffic rules and separate paths.
These work environments face several key hazards:
-
Moving machinery and equipment hazards
-
Hazardous chemicals and substances
-
Working at heights risks
-
Electrical hazards
-
Noise and vibration exposure
-
Manual handling and ergonomic risks
Height-related accidents remain the top cause of deaths at work. They make up about a quarter of all worker fatalities. Workers need proper fall protection systems and stable platforms when working above ground level.
Non-mechanical hazards pose serious risks too. Workers face dangers from harmful emissions, pressurised fluids, and chemical by-products. Noise levels at these sites often go beyond safe limits. Without proper controls, workers could suffer permanent hearing damage.
Workers need extra safety measures when doing maintenance, repairs, or cleaning tasks. These jobs often involve confined spaces or high places. This means detailed safety rules and the right protective gear are crucial.
Essential Safety Equipment and Tools
Safety equipment acts as the final defence against workplace hazards. We selected Personal Protective Equipment (PPE) based on workplace risks and specific tasks.
A warehouse and construction site’s essential PPE has:
-
Hard hats to protect against falling objects
-
Safety goggles to shield eyes from debris and chemicals
-
Respiratory protection to work in hazardous environments
-
High-visibility clothing with reflective strips
-
Safety boots with non-slip soles
-
Protective gloves that match specific tasks
-
Hearing protection devices
Companies must give workers their PPE free of charge. The equipment should fit well, feel comfortable, and work with other protective gear.
Workers need good training about PPE’s use, upkeep, and storage. They should know how to check their equipment before use, keep it clean, and spot when it needs replacement.
Workers have clear duties with their PPE. They should use it as trained and report any damage or maintenance needs quickly. Intentional damage is not allowed. Breaking these rules could lead to discipline or legal action.
PPE’s success depends on choosing and maintaining it correctly. Teams should check equipment regularly to make sure it still protects workers well. Site visitors must get proper protective gear along with clear instructions about its use.
Building a Safety-First Culture
A resilient safety culture starts with steadfast dedication from senior leaders. Research shows that workers who participate are more aware of their surroundings and safety best practises. These workers take more steps to protect their colleagues.
Leadership must show safety values through actions rather than just policy statements. Senior managers should join safety inspections, assess risks regularly, and lead toolbox talks. Companies that encourage managers to challenge unsafe behaviours while recognising positive safety attitudes create an environment where safety becomes natural.
Workers need clear roles and objectives. Those who understand their company’s safety goals and their role in achieving them show higher engagement levels. Professional development and ongoing training are vital since data shows only about one-third of the workforce actively participates.
Communication shapes a safety-first mindset. Workers must feel comfortable voicing concerns to approachable and trustworthy managers without fear of consequences. Regular safety meetings work best when they encourage open dialogue and suggestions for improvement.
Recognising safe behaviour strengthens positive practises. But incentive programmes should celebrate team safety achievements instead of individual rewards because individual focus might discourage incident reporting. Organisations that consistently apply these principles build a culture where safety guides every operational decision and workplace interaction.
Conclusion
Safe work practises are the life-blood of warehouse and construction site management. Our exploration of workplace hazards, safety equipment requirements, and cultural considerations shows that worker protection just needs a complete approach.
Workplace accidents cost both lives and resources – the statistics make this clear. Organisations must prioritise safety through proper hazard identification, appropriate PPE provision, and strong leadership commitment. Companies that accept these principles see measurable improvements in worker participation and operational efficiency.
Safety protocols must be applied consistently with regular training and open communication channels to succeed. Note that safety culture evolves gradually. This evolution requires sustained effort and dedication from all organisational levels.
The long-term benefits are nowhere near the investment needed to implement resilient safety measures. Lower accident rates, better worker morale, and improved productivity prove the value of making workplace safety a priority. Companies that focus on safety create environments where workers thrive and operations flourish.
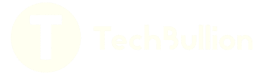