Milling machines are an essential tool in the manufacturing sector, playing a pivotal role in the creation of various components. Their primary function revolves around the removal of material from a workpiece, using rotary cutters to achieve the desired shape. As diverse as the industries they serve, milling machines have established themselves as foundational assets in sectors ranging from aerospace to automotive.
1. Defining the Milling Machine: Basics and Operation
Some good options can be found on Knuth’s milling machines page.
Milling machines are devices designed to machine solid materials, predominantly metals. They work by moving the workpiece into a rotating cutting tool, which then removes material. Guided by computer software, these machines provide impeccable precision, enabling the creation of intricate components with ease.
2. Delving into the Different Types of Milling Machines
Vertical Milling Machines: The spindle, equipped with cutting tools, is aligned vertically. The workpiece is typically fixed on a horizontal table that moves up and down.
Horizontal Milling Machines: Here, the spindle’s orientation is horizontal. These machines are ideal for jobs requiring deep cuts or grooves.
Universal Milling Machines: Combining the capabilities of both vertical and horizontal milling, these machines offer flexibility and are known for their versatility.
CNC Milling Machines: Modern and automated, CNC (Computer Numerical Control) milling machines are guided by computer programs, ensuring unparalleled precision and repeatability.
3. Materials and Their Compatibility with Milling
Milling machines can process a wide array of materials, from metals like aluminum, steel, and brass to non-metals such as plastics and ceramics. The choice of material significantly affects the milling process, tooling requirements, and parameters like speed and feed.
4. Ensuring Longevity and Efficiency in Milling
Routine Maintenance: Regular inspection and maintenance of the machine are paramount. This includes cleaning, lubricating moving parts, and checking for wear and tear.
Calibration: Periodic calibration ensures the milling machine continues to operate with precision.
Tool Quality: The quality and sharpness of the cutting tools directly impact the machine’s performance. Regularly checking and replacing worn tools is essential.
5. Safety Practices in Milling Operations
Training: Operators must be adequately trained to understand the machine’s workings, safety protocols, and emergency measures.
Personal Protective Equipment (PPE): Safety glasses, gloves, and ear protection are crucial to safeguard operators from potential hazards.
Workspace Cleanliness: Keeping the workspace clean and free from debris prevents accidents and ensures efficient operation.
6. Factors to Consider When Purchasing a Milling Machine
Operational Needs: Determine the size and type of materials you’ll be working with, the intricacy of the tasks, and the volume of production.
Budgetary Constraints: While it’s tempting to go for advanced models, it’s essential to strike a balance between needs and budget.
Space and Setup: The machine size should be compatible with the available space, ensuring ease of operation and maintenance.
Manufacturer’s Reputation: Research the manufacturer’s track record, after-sales service, and the availability of spare parts.
In Conclusion
Milling machines, in their varied forms and capabilities, continue to be invaluable assets in the world of manufacturing. Their evolving technology promises even more significant advances, paving the way for a future where precision and efficiency reach new heights.
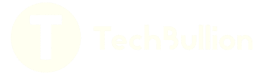