In plastic injection moulding, mould temperature controllers (MTCs) are essential tools that ensure consistent product quality, faster cycle times, and energy efficiency. These devices regulate the temperature of the mould throughout the entire injection process, providing stability in material flow, cooling rates, and final part properties. However, proper installation and optimization are crucial for manufacturers to reap the full benefits of MTCs.
This guide will walk you through the installation process, key features to consider when choosing an MTC, and best practices for optimizing its performance in your production line.
What is a Mould Temperature Controller?
A mold temperature controller (MTC) is used in injection moulding to control the mould’s temperature by circulating water or oil through its cooling channels. It ensures that the mould remains at the optimal temperature throughout the production cycle. The MTC typically consists of a heating or cooling unit, a pump to circulate the medium (water/oil), and a control system to maintain the set temperature.
Why is mould temperature control important?
Consistent part quality: Maintains dimensional stability and reduces defects such as warping, sink marks, and short shots.
Faster cycle times: Optimized cooling ensures that parts solidify quickly, allowing speedier mould release.
Energy efficiency: Reduces energy consumption by keeping the mould at the correct temperature.
Increased mould lifespan: Reduces thermal stress on the mould, minimizing wear and tear over time.
Choosing the Right Mould Temperature Controller
Before installing a mould temperature controller, selecting the right one for your production needs is critical. Here are vital factors to consider:
Temperature Range
The required temperature range depends on the type of plastic resin used in the production process. Water-based MTCs generally operate within a lower temperature range (up to 90°C or 194°F), while oil-based MTCs can handle higher temperatures (up to 350°C or 662°F). Ensure the MTC’s temperature range matches the material and production process.
Heating and Cooling Capacity
MTCs come with varying capacities in heating power (measured in kilowatts) and cooling capacity (measured in kilocalories or BTUs). The heating capacity ensures the mould reaches the required temperature quickly, while the cooling capacity maintains precise control of the mould temperature during production. The mould size and production speed will influence the capacity needed.
Pump Flow Rate
The pump flow rate determines how quickly the heat transfer medium (water or oil) circulates through the cooling channels. Higher flow rates ensure uniform temperature distribution across the mould surface, reducing the likelihood of hot spots or cold zones. For larger moulds, ensure the MTC has a pump with sufficient flow capacity.
Digital Control Systems
Modern MTCs are equipped with digital control systems that allow precise temperature regulation. Look for systems that monitor real-time temperature, have programmable settings for different mould cycles, and provide automatic alerts for deviations or faults. A touchscreen interface and data logging features are valuable for tracking production performance.
Safety Features
Safety should always be a priority when installing an MTC. Look for controllers with built-in safety mechanisms such as over-temperature protection, pressure release valves, and automatic shutoff in case of malfunction. These features protect the mould, the machine, and your production staff.
Installation of Mould Temperature Controllers
Proper installation ensures that your MTC functions efficiently and delivers optimal temperature control. Below is a step-by-step guide for installing a mould temperature controller:
Prepare the Installation Site
Electrical connections: Ensure that the power supply voltage and frequency match the MTC’s specifications. If the MTC operates at a higher voltage (380V), ensure the site is equipped with the appropriate electrical infrastructure.
Water or oil supply: For water-based MTCs, ensure a stable water supply with adequate flow and pressure. Oil-based MTCs require specific oil types, so consult the manufacturer’s recommendations for compatibility.
Cooling tower connection: If your MTC requires external cooling, connect it to a cooling tower or chiller. Ensure that all water pipes are adequately insulated to prevent temperature loss.
Connect the MTC to the Injection Molding Machine
Water/oil inlet and outlet: Connect the water or oil inlet and outlet pipes from the MTC to the mould’s cooling channels. Ensure the connections are secure and leak-free.
Temperature sensors: Install temperature sensors in the mould to monitor the real-time temperature. These sensors feed data to the MTC’s control system, allowing for automatic temperature adjustments.
Set the Operating Parameters
Target temperature: Set the desired mould temperature based on the type of plastic resin you are using. For example, polypropylene typically requires mould temperatures of 40-70°C, while engineering plastics like ABS may need higher temperatures.
Flow rate: Adjust the pump’s flow rate to ensure efficient circulation through the mould’s cooling channels.
Test the System
Once all connections are made, run a test cycle to ensure the MTC operates correctly. Check for:
Leaks in the water/oil lines.
Proper temperature control (temperature remains stable throughout the cycle).
Adequate flow rate in the cooling channels.
Pressure stability Optimizingtem.
Optimizing Mould Temperature Controllers for Maximum Efficiency
To fully benefit from optimization, optimization of its performance is critical. Here are the besoptimizeces to optimize your MTC for maximum efficiency:
Monitor Temperature Consistency
Monitor the mould’s temperature regularly and ensure that it stays within the set parameters. Temperature variations can lead to inconsistent part quality and defects like warping or sOptimize.
Optimize Cooling Channel Design
The design of the mould’s cooling channels significantly affects the efficiency of the temperature control. Cooling channels should be placed close to the mould cavity and distributed evenly to avoid hot or cold spots. Implementing conformal cooling designs with 3D-printed moulds can enhance the heat transfer process.
Use a Digital Control System for Precision
Leverage the MTC’s digital control system to set precise temperatures for different stages of the injection process. For example, you can program the system to maintain higher temperatures during injection and lower temperatures during cooling to reduce cycle time.
Regularly Clean and Maintain the MTC
Mould temperature controllers require regular maintenance to ensure optimal performance. This includes:
Cleaning: Flush the system to remove any debris, scale, or contaminants affecting the heat transfer process.
Inspecting seals and hoses: Check for leaks or damage that could lead to performance inefficiencies.
Calibrating temperature sensors: Ensure the temperature sensors provide accurate readings for precise optimization.
Optimize Cycle Times
Fine-tune your moulding cycle to match the capabilities of your MTC. Too much cooling time can lead to extended cycle times and reduced productivity, while insufficient cooling can result in defective parts. Monitor and adjust cycle times for each mould to achieve the right balance.
Energy EOptimizey
Optimize energy consumption by setting the MTC only to heat or cool when necessary. Some modern MTCs feature automatic shutoff mechanisms when the mould reaches the desired temperature, reducing energy costs.
Troubleshooting Common MTC Issues
Despite proper installoptimizationtimization, some issues may arise. Here are common problems and solutions:
Temperature fluctuations: If the mould temperature is unstable, check for blockages in the cooling channels or leaks in the system.
Insufficient cooling/heating: Ensure the pump flow rate is sufficient and the cooling medium (water/oil) is circulating correctly.
Mold overheating: Poor heat dissipation can cause mould overheating. Inspect the cooling channels and verify the proper functioning of the cooling system.
Mould temperature controllers are essential.
Mould temperature controllers are essential for ensuring high-quality production in injection moulding. Proper installation and optimizing cooling channels, temperature settings, and digital control systems can significantly reduce defminimizenimize cycle times and improve production efficiency. By following the best practices outlined in this guide, manufacturers maximize their ability to ensure consistent product quality while reducing operating costs and energy consumption.
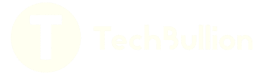