The global supply chain, an intricate network vital to modern commerce, has faced unprecedented challenges in recent years. From the widespread disruptions caused by the COVID-19 pandemic, which affected nearly 73% of companies in 2021, to the ongoing pressures of geopolitical instability and rising operational costs, the need for innovation has never been more acute.
The cost of logistics and transportation in the US, for example, has seen annual increases of 19.6%, with inventory carrying costs surging by over 25%. These figures highlight a landscape demanding transformative solutions and visionary leadership.
Prashanth Cecil stands as a prominent figure in this evolving domain, an accomplished operations and supply chain leader with extensive experience at major corporations including Amazon, Intel, and Procter & Gamble. Currently General Manager at Amazon’s Northern California fulfillment center, he oversees a 1.1 million sq. ft facility and a team of over 1,200 associates.
His career, which began at Maruti Suzuki India Limited and included significant roles at P&G managing manufacturing operations across India, the Middle East, and Africa, is marked by a consistent drive for technological advancement and operational excellence.
He has a strong record of implementing pioneering solutions like LiDAR and IoT for warehouse inventory tracking, adopting machine learning models to optimize sort allocations, and driving automation projects that have yielded 25% efficiency gains. His leadership has also resulted in significant safety improvements, including a 68% year-over-year reduction in safety incidents and substantial cost savings through layout modifications.
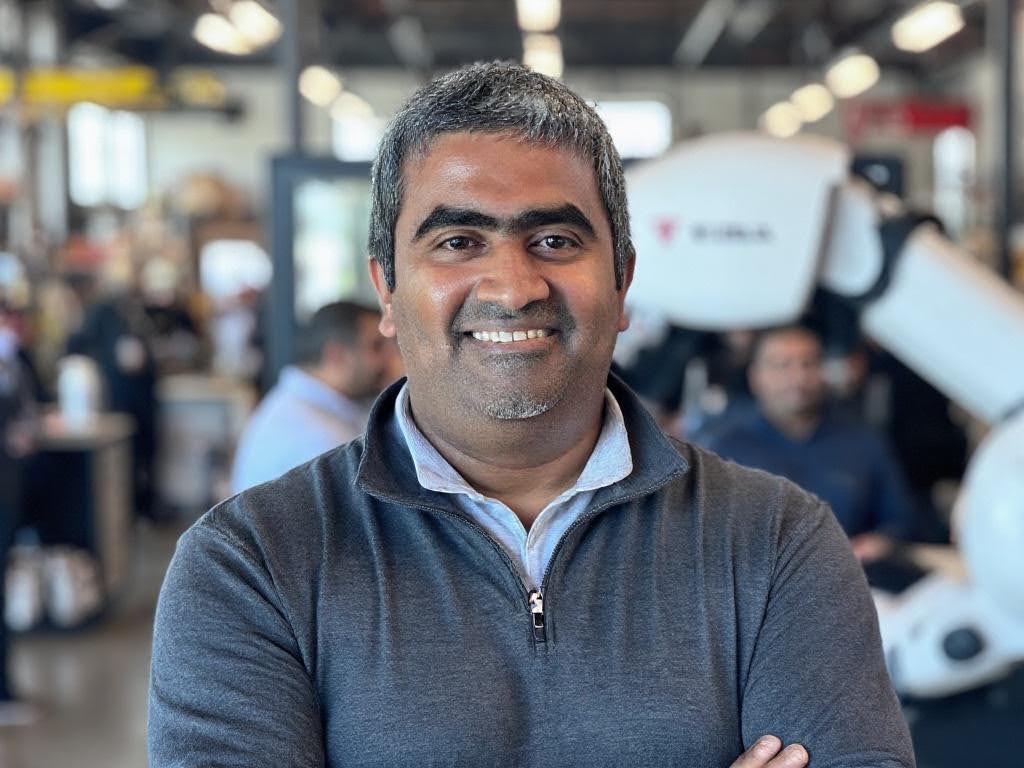
Prashanth Cecil
His work on international benchmarking at P&G led to an 8% process reliability improvement and incremental production increases, showcasing his ability to drive global operational enhancements. A dedicated mentor, Cecil has also coached numerous managers to senior positions, underscoring his commitment to talent development.
Inspiration for LiDAR and IoT
The impetus to integrate advanced technologies like LiDAR and IoT into warehouse inventory tracking often stems from a clear recognition of the limitations of traditional methods. For Cecil, the journey towards adopting these innovations was driven by observing their successful application in other sectors and a deep understanding of the specific inefficiencies within fulfillment centers.
He saw an opportunity to address multiple challenges simultaneously, including improving inventory accuracy and reducing process cycle times; the integration of LiDAR and IoT is indeed revolutionizing warehouse operations by providing real-time data and enabling precise spatial mapping.
Cecil elaborates on his initial motivation: “Throughout my career in operations management, I’ve always been driven by a desire to solve complex logistical challenges through innovation. What initially inspired me to explore LiDAR and IoT technologies was seeing their successful application in retail store environments for customer tracking and inventory management.”
He continued, “I recognized that these same technologies could potentially address the significant inefficiencies we were experiencing in our traditional fulfillment center, particularly with large, non-conveyable items.” This proactive approach, adapting proven technologies from one domain to another, is characteristic of forward-thinking leadership.
The aim was to transform how inventory was located and moved, addressing bottlenecks created by manual tracking. The decision to champion these technologies was further solidified by the multifaceted benefits they promised.
Cecil explains, “The inspiration to implement LiDAR and IoT technologies came from recognizing an opportunity to address multiple operational challenges simultaneously. Our fulfillment center was experiencing challenges with inventory accuracy, increased cycle time in outbound processes, and associate safety concerns due to the manual nature of tracking large items.”
He added, “What truly compelled me to champion this innovation was seeing the potential triple benefit: improved operational metrics, enhanced worker safety, and significant cost savings.” This vision led to tangible results, such as improving fulfillment process accuracy from 97% to 99.9%, demonstrating the powerful impact of these technologies.
Navigating LiDAR and IoT adoption
Introducing new technologies into large-scale operations is rarely without its hurdles, often encountering resistance and presenting unforeseen technical complexities. Cecil’s approach to implementing LiDAR and IoT technologies was rooted in a strategic change management process that prioritized associate buy-in and iterative improvement.
He recognized that gaining the support of frontline associates and managers was as critical as overcoming technical integration challenges, aligning with best practices in change management that emphasize clear communication and stakeholder engagement.
A key element of Cecil’s strategy was early engagement and the formation of cross-functional teams. “First, I recognized that associate buy-in would be critical. Rather than simply announcing a new technology initiative, I engaged frontline associates and area managers early in the process.” He further stated, “We created cross-functional pilot teams that included representatives from operations, IT, maintenance, and safety.”
These teams were not passive observers but active participants, providing feedback that shaped the implementation. This collaborative approach helps in building ownership and addressing concerns proactively. The technical side, particularly integrating new systems with existing warehouse management systems, also required significant attention.
To overcome resistance and manage expectations, Cecil focused on tangible benefits and an iterative rollout. He states, “I emphasized concrete benefits rather than abstract technological advantages. For associates, we highlighted how the technology would reduce their physical strain by eliminating unnecessary movement and searches for inventory.”
“For managers,” he continued, “we demonstrated the impact on key performance metrics and cost savings.” Coupled with tailored training programs and a willingness to adapt, this approach proved effective.
“The most valuable lesson from this implementation was the importance of iterative improvement,” Cecil notes. “Rather than attempting a perfect launch, we started with a minimum viable product, gathered feedback continuously, and made rapid adjustments,” highlighting a strategy that led to a 12% reduction in outbound process cycle time.
Developing an ML model for sort allocation
ML has emerged as a transformative force in supply chain optimization, offering powerful tools for enhancing efficiency. Cecil spearheaded the development of an ML model to tackle a significant challenge: optimizing sort allocations on large volume sorters to maximize throughput.
The project leveraged Amazon SageMaker, and a custom XGBoost model was chosen for its efficacy in handling complex variables. The successful application of ML in areas like demand forecasting is well-documented, often leading to substantial cost reductions and improved service levels.
The development process was methodical, beginning with comprehensive data collection and rigorous preprocessing. Cecil explains, “We began by collecting comprehensive historical data from various flat sorters across the network, including throughput metrics, package dimensions, weight distributions, destination clusters, and time-based patterns. This data underwent rigorous preprocessing to handle missing values and normalize features.”
He added, “We then split the data into training, validation, and testing sets to ensure robust model performance.” This structured approach is crucial for building reliable ML models. A distinctive feature of this implementation was its ability to adapt to real-world operational dynamics.
The impact of the ML model was substantial, leading to a 30% increase in flat sorter throughput and an 89% reduction in recirculation rates. Cecil attributes this success to a blend of technical expertise and operational insight: “What made our approach unique was the incorporation of real-time operational constraints. The model needed to adapt to dynamic variables like staffing levels, inbound volume fluctuations, and downstream capacity.”
“We implemented a feedback loop that continuously refined the model based on operational outcomes, which was critical for maintaining performance across varying conditions,” he elaborated. This solution was subsequently adopted as an industry best practice.
Impactful automation projects
While large-scale automation often captures headlines, Cecil has found that smaller, targeted automation projects can deliver more immediate and impactful results. These focused initiatives contributed significantly to the 25% overall efficiency gains achieved in his operations. One such project involved implementing computer vision technology for quality control, a technology increasingly recognized for improving accuracy and potentially reducing inventory costs by up to 25%.
Cecil describes the targeted approach: “Rather than investing millions in a complete system overhaul, we started with a focused application that used industrial inspection cameras and machine learning algorithms to identify defects that human inspectors might miss.
This targeted approach gained immediate buy-in from frontline teams because they could see how it enhanced their capabilities rather than replacing them.” He noted, “The result was a 40% reduction in quality-related returns within just three months.”
Another successful project involved automating storage location assignments based on product velocity, which reduced travel distances by 22% with minimal capital expenditure. The success of these smaller projects, according to Cecil, lies in their focus on specific pain points and incremental implementation.
“I’ve consistently found that smaller automation projects succeed where ambitious overhauls fail for three reasons. First, they focus on solving specific pain points that teams already recognize, which creates natural champions for adoption.”
He continued, “Second, they can be implemented incrementally, allowing for continuous refinement based on real-world feedback.” These targeted projects build organizational confidence and create momentum for more extensive automation initiatives.
Assessing technological innovations
With a constant stream of new technologies emerging, a structured approach to evaluating their potential impact is crucial for sound investment decisions. Cecil employs what he terms the “Operational Impact Assessment Matrix,” a framework designed to quantify the value of innovations. This systematic evaluation helps prioritize technologies that offer the most significant operational benefits relative to their implementation effort.
The matrix evaluates technologies based on four pillars: Value creation potential, implementation feasibility, organizational readiness, and strategic alignment. Cecil explains, “Each technology is scored on a 1–5 scale across these dimensions, creating a comprehensive profile that guides investment decisions. We then plot technologies on a quadrant map with ‘Implementation Effort’ on one axis and ‘Operational Impact’ on the other.”
This methodical process ensures that decisions are data-driven and aligned with strategic objectives. This framework has proven effective in practice. “For example, when evaluating robotics solutions for our fulfillment processes, we discovered that a mid-tier automated inventory tracking system using LiDAR and IoT scored higher in our matrix than a fully automated picking solution, despite the latter being more advanced,” Cecil shares.
The tracking system addressed a critical pain point in inventory accuracy with less integration effort. He further emphasizes the collaborative nature of this process: “What makes this approach particularly effective is how it democratizes the evaluation process. By establishing clear criteria, we can involve cross-functional stakeholders in technology assessment, ensuring we capture diverse perspectives on potential impacts.”
Lesser-known technological benefits
Beyond the widely recognized efficiency gains, advanced supply chain technologies offer transformative improvements to both employee and customer experiences. Cecil highlights several such benefits observed in large fulfillment operations, emphasizing how technology can humanize the supply chain. These include advanced safety monitoring systems that enhance workplace safety and machine learning algorithms that optimize work scheduling by incorporating employee preferences.
From the customer’s perspective, Cecil points to the quiet revolution brought about by AI-driven demand forecasting integrated with inventory placement. “Modern supply chain systems now analyze not just historical purchasing patterns but also emerging social trends, weather events, and regional preferences to predict demand spikes before they occur. This means customers consistently find what they need when they need it, even during unexpected demand surges.”
He added, “The emotional impact of reliable availability on customer satisfaction far exceeds what traditional metrics capture.” Similarly, dynamic routing systems that consider real-time conditions have significantly reduced missed deliveries and damaged packages. Cecil believes that the true value of technology extends beyond pure metrics.
“The most valuable technologies aren’t necessarily those that drive the biggest efficiency gains but those that humanize the supply chain experience,” he stated. “Advanced vision systems that help employees quickly identify hazards, AI assistants that empower workers to make better decisions, and customer communication tools that provide unprecedented visibility — these technologies create benefits that don’t always show up on traditional scorecards but fundamentally transform how people experience the supply chain.” This perspective underscores a holistic view of technological impact.
Next major supply chain innovations
Looking ahead, Cecil envisions the next wave of supply chain transformation emerging from the convergence of real-time visibility networks, artificial intelligence, and sustainable operations. While individual technologies like autonomous vehicles will mature, the true breakthrough will be in creating interconnected, intelligent supply networks. This aligns with industry forecasts that see AI and cloud solutions as pivotal for future capabilities.
Cecil foresees a future where supply chains operate as self-healing networks. “When disruptions occur—whether from natural disasters, geopolitical events, or unexpected demand spikes—the system automatically reconfigures routing, adjusts inventory positions, and optimizes production schedules without human intervention. Unlike today’s reactive systems, these networks will be truly predictive, detecting potential issues days or weeks before they materialize.”
Another critical evolution will be the complete digitization of inventory, with comprehensive digital twins containing location, condition, and carbon footprint data; digital twins are increasingly seen as key to unlocking end-to-end supply chain growth. Sustainability is also central to Cecil’s vision, becoming fully integrated into decision-making. “Supply chain systems will automatically optimize for carbon impact alongside traditional metrics like cost and speed,” he predicts.
Furthermore, he sees these technologies transforming the human element, automating mundane tasks, and allowing professionals to focus on strategy and innovation. “The organizations that will lead this transformation won’t necessarily be those with the largest technology budgets, but rather those that can effectively combine technological capabilities with the right operating models and talent strategies,” Cecil concludes.
Ensuring employee adoption
The successful implementation of new technology in the supply chain hinges critically on employee adoption and engagement. Cecil emphasizes that technology without proper human integration is an underutilized asset. His strategies for fostering adoption focus on involving employees from the outset and providing contextual learning, aligning with effective change management practices that include clear communication and robust training.
Cecil believes in empowering frontline employees. “During my time launching a new multi-million-dollar fulfillment center, we established ‘innovation teams’ composed of associates from various levels. These teams weren’t just consulted—they had meaningful input on system design and process flows.”
He elaborated, “When people help build something, they develop a sense of ownership that drives adoption far more effectively than top-down mandates.” This approach is complemented by innovative training methods.
“We’ve moved beyond traditional training approaches to what I call ‘contextual learning environments.’ When implementing new automation systems, we created micro-learning opportunities embedded directly in the workflow rather than relying solely on classroom sessions,” he explains, noting this reduced training time by 40%.
Transparency and ongoing communication are also vital. Cecil states, “When employees understand how technology impacts broader goals—not just productivity but also quality, safety, and customer experience—they’re more motivated to embrace new tools.” He champions a ‘continuous conversation’ through regular forums for feedback, which helps identify problems and surface innovative solutions.
“Ultimately, successful technology adoption isn’t about forcing compliance—it’s about building a culture where technology is viewed as an enabler rather than a replacement,” Cecil asserts. “When employees see themselves as partners in digital transformation rather than subjects of it, the results are exponentially better.”
Cecil’s career and insights provide a compelling narrative of how strategic technological adoption, coupled with strong leadership, can drive transformative change. From pioneering LiDAR and IoT for enhanced inventory tracking to implementing sophisticated machine learning models, his work demonstrates a holistic approach.
As supply chains continue to evolve, Cecil’s focus on creating resilient, agile, and human-centric systems offers a clear blueprint for navigating modern commerce and shaping a more sustainable future. His emphasis on both groundbreaking technological integration and the indispensable human element ensures that progress is not only efficient but also equitable and enduring.
This balanced perspective is crucial as industries worldwide strive to build supply networks that can withstand future shocks while fostering innovation and growth. Ultimately, Cecil’s contributions underscore the idea that the most advanced supply chains are those that intelligently weave together technology, strategy, and people.
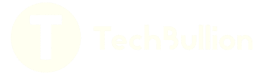