In an era defined by innovation, connectivity, and speed, the manufacturing industry is undergoing a dramatic transformation. While digital technologies like IoT, AI, and automation tend to grab headlines, the foundation of many advancements remains deeply physical: precision metal fabrication.
Often operating behind the scenes, precision fabrication enables the creation of the parts, structures, and systems that power everything from transportation to telecommunications. As industries demand greater efficiency, tighter tolerances, and faster production, advanced metalworking technologies like CNC machining and laser cutting have emerged as vital tools in the manufacturing toolkit.
The Rise of High-Precision Fabrication
Metal fabrication has long been a staple of industrial production. But modern precision fabrication is a far cry from traditional welding and stamping. Today’s systems involve sophisticated machinery, computer-aided design (CAD), and real-time process controls—all working together to produce parts accurate to within microns.
This high level of precision is crucial across sectors:
- Aerospace and automotive industries require consistently accurate components to ensure performance and safety.
- Medical device manufacturers demand ultra-precise surgical instruments and implants.
- Electronics rely on metal housings, brackets, and cooling systems fabricated with microscopic precision.
Unlike mass production, where flexibility is often sacrificed for volume, precision fabrication delivers both scalability and customization.
CNC Machining: Precision at Scale
One of the most transformative technologies in modern metal fabrication is Computer Numerical Control (CNC) machining. In this process, pre-programmed software dictates the movement of tools and machinery, enabling manufacturers to automate even the most complex cutting, drilling, and milling tasks.
Key benefits of CNC machining include:
- Consistency: Identical parts can be produced repeatedly without variation.
- Efficiency: Complex geometries are machined quickly and accurately.
- Material versatility: CNC machines can work with steel, aluminum, brass, and other alloys.
Whether producing prototypes or full-scale production runs, CNC machining empowers manufacturers to meet modern demands for speed, precision, and flexibility.
The Integration of Laser Cutting and Presswork
Laser cutting has added another layer of precision to the fabrication process. Using high-powered beams, fabricators can achieve:
- Clean, burr-free cuts
- Minimal material waste
- High-speed processing of intricate designs
When combined with presswork where custom dies and high-tonnage machines stamp metal into shape fabricators can produce high-volume parts quickly and affordably. This makes it ideal for components like enclosures, fixtures, and sheet metal parts across automotive, construction, and industrial sectors.
Applications Across Industries
Precision metal fabrication plays a critical role in a variety of modern applications:
- Renewable energy systems: Fabricated frames and enclosures for solar panels and wind turbines.
- Smart infrastructure: Custom brackets and fixtures for sensors, security systems, and control panels.
- Industrial automation: Housings, supports, and linkages for robots and automated machinery.
- Public and commercial hardware: Durable, precision-cut fittings for restrooms, railings, signage, and more.
The ability to quickly produce reliable, customized parts gives manufacturers an edge in competitive markets where downtime or supply chain delays can mean lost revenue.
Quality Control and Traceability
As tolerance expectations tighten, quality control becomes non-negotiable. Leading fabrication shops invest heavily in:
- In-process inspections using sensors and digital measuring tools.
- Non-destructive testing to validate welds and structural integrity.
- Material certification and traceability, especially in regulated sectors like aerospace and defense.
These capabilities ensure compliance, reliability, and long-term customer trust—critical factors in today’s highly competitive B2B environment.
Sustainability in Modern Fabrication
Sustainability is no longer a buzzword—it’s a necessity. Fortunately, modern fabrication processes support green manufacturing by:
- Reducing waste through accurate cutting and efficient material use.
- Optimizing energy consumption via CNC and automated systems.
Encouraging recyclability by working with metal alloys that can be reused and repurposed.
As environmental regulations grow stricter and consumers demand greener supply chains, precision fabrication offers a tangible way to reduce environmental impact without compromising quality or performance.
Choosing the Right Fabrication Partner
Selecting a fabrication partner is about more than price it’s about reliability, innovation, and support. Manufacturers should look for providers that offer:
- Full-service capabilities, from design to delivery
- Experience with multiple materials and industries
- A strong reputation for consistency and responsiveness
- Investment in modern equipment and process control
For example, companies like Kirmell have built their reputation on decades of delivering precision-engineered components for industrial, commercial, and architectural applications in the UK and beyond.
Conclusion
As global supply chains grow more interconnected and industries push for greater efficiency, the importance of precision metal fabrication continues to rise. Technologies like CNC machining, laser cutting, and presswork aren’t just enabling better parts—they’re empowering better products, processes, and performance across the board.
By embracing the latest in fabrication technology and working with experienced partners, businesses can reduce lead times, boost quality, and bring bold ideas to life in metal.
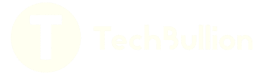