What Materials Can Be Used in CNC Machining?
CNC machining is fundamentally a very accurate procedure that involves converting a raw material into a custom-made product by employing computer-controlled tools. The technique is most certainly very reliable for engineers, manufacturers, and DIY enthusiasts for parts with very close tolerances and complicated geometries. It is difficult to find exactly the right material on cnc quote online because of the contradictory requirements like durability, price, and the specific needs of the particular application.
This article is to help overcome these problems by discussing various metals (such as aluminum, stainless steel) and plastics (like ABS, PEEK), which are the most suitable for CNC machining. Keep reading!
Common Metal Materials in CNC Machining
CNC machining is deeply dependent on metals for its strength and resistance. This paragraph highlights the comparison of several aluminum alloys, stainless steel grades, and niche metals such as titanium, copper, and brass in terms of properties, examples of use, and machining efficiency.
Aluminum Variants
Aluminum 6061 and 7075 are lightweight and corrosion-resistant designs, which are the most widely used in the industry for such properties. 6061 is a softer and more machinable alloy that can be used in aerospace (e.g., aircraft parts) and automotive (e.g., engine mounts) applications. 7075, which is stronger but more expensive, can be used in those situations that require high strength.
For example, when we are considering an aircraft frame or a bicycle frame for competitive racing. Both grades of aluminum are very close to one another in terms of machinability and cost, although 7075 has to be machined with specialized tools and equipment to obtain precise cuts.
Stainless Steel Grades
Stainless steel 304 and 316 are chosen for their properties of being rust-resistant and strong. 304 is the cheapest and most food-safe among stainless steels; therefore, it is most often used for manufacturing medical devices (e.g., surgical tools) and marine hardware like boat fittings. The 316 steel gives better performance in corrosion resistance in extreme conditions such as hot chemical containers or seawater. Though both grades are able to tolerate high temperatures, 316 is suggested for conditions with the highest temperature due to the presence of molybdenum in it.
Niche Applications in CNC Machining
Titanium is a material that has an excellent strength-to-weight ratio and also biocompatibility, so it is a perfect choice for medical implants and aerospace parts such as engines. Copper’s high conductivity is the reason it is used in electrical components (for instance, circuit boards), whereas brass provides the aesthetic aspects of the decorative parts, which are the intricate fixtures, for example. These metals meet the specialized needs that are a perfect match for the performance and design requirements.
Common Plastic Materials for CNC Machining
While metals are often used in applications that need high strength and performance, plastics are an excellent alternative that has the advantage of being lighter and more resistant to corrosion in the context of CNC machining. The following section deals with thermoplastics, high-performance plastics, and specialized plastics, mainly concentrating on their properties, the degree of difficulty in machining, and their usage in real life.
Thermoplastics
ABS (Acrylonitrile Butadiene Styrene) is the best thermoplastic for prototyping since it has great impact resistance and is inexpensive. Consumer electronics, such as phone cases or toy parts, serve as a good example of this where the rapid production and durability matter.
Nylon is a sturdy thermoplastic that makes mechanical parts like gears and bearings with its durability under friction. Polycarbonate is a clear and impact-resistant material that is perfect for making optical components such as lenses or safety goggles.
High-Performance Plastics
PEEK (Polyetheretherketone) is a great chemical-resistant product that can handle temperature and it is mostly used for medical implants and high-heat machinery. POM (Polyoxymethylene, or Delrin®) has very low friction; therefore, it is best for precision parts such as bushings or bearings where smooth movement is imperative.
Specialized Plastics
PVDF (Polyvinylidene Fluoride), being chemically resistant, is frequently the material of choice in piping systems for industrial environments. PTFE (Teflon®) is well known for the non-stick surfaces that can be derived from it when it is applied to seals and cookware. UHMW-PE (Ultra-High Molecular Weight Polyethylene) is very resistant to various types of damage and thus it is the best choice for conveyor systems and sliding parts.
Material Properties and Their Impact on CNC Machining Processes
In connection with the latest research on traditional materials, the understanding of their characteristics is the next step, which is essential in achieving substantial success in CNC machining. This part focuses on machinability, heat resistance, and strength, offering engineers a range of options for choosing the machine that is suitable for their working efficiency, environmental endurance, and cost.
How Material Hardness Affects CNC Machining
Machinability primarily decides the extent to which a given material can easily be shaped. The metals, such as aluminum 6061, are very soft and allow machining operations to be done smoothly, thus less tool pressure and faster feed rates are required. In contrast, hardened steel is cutting resistant which means the speeds have to be lowered and tools that are durable must be used so that they do not break.
Since plastics can be very different, it is PEEK and PTFE that are difficult because of their hardness and slippiness, but ABS and nylon can be machined without any problem. As an illustration, aluminum 6061 is suitable for rapid prototyping and at the same time, hardened steel is meant for heavy machinery parts.
Thermal and Environmental Resistance
Thermal resistance and environmental durability are important factors due to their capability in extreme conditions. PEEK and stainless steel 316 are very suitable for high-temperature environments like aerospace components or chemical reactors due to their heat stability as well as these materials.
HDPE and stainless steel 304 are the best materials that can resist outdoor weathering, thus they are the most suitable for marine hardware and coastal signage. Stainless steel 304 is also food-safe, used in kitchenware, while HDPE’s flexibility suits piping systems.
Cost Analysis
Products that are low-cost such as aluminum and ABS may contribute to the reduction of upfront expenses; however, these products may not be able to sustain long periods of use. Aluminum is an easily portable and inexpensive material that is commonly used for consumer electronics, whereas ABS is more affordable for prototyping but less durable.
Titanium and PEEK are materials of high performance that deserve the price they get, especially in the case of usage in energetically challenging environments.
Application-Specific Material Selection for CNC Machining
We are talking about materials that can be used in the aerospace, medical/food-grade, and outdoor/marine industries. The section is centered on the environmental aspects, such as the necessity of durable products and waste reduction.
High-Performance Materials
Aluminium 7075 and Titanium Grade 5 are the first among the top ones for the aerospace and automotive sectors because of their unmatched strength-to-weight ratios. Aluminum 7075, which is very light and also has high fatigue resistance, is used in aircraft structural components and racing car frames.
Titanium Grade 5 which is very corrosion resistant, is the most suitable material for jet engine parts and high-stress automotive fasteners. Also, both materials have the feature of withstanding high temperatures and vibrations; therefore, they are essential in industries that require high performance.
Hygienic Materials
Stainless Steel 316L and PEEK are the most common materials that come from the medical and food-grade sectors. Stainless Steel 316L is a material that is antimicrobial and resistant to harsh cleaning agents, which are typical in surgical instruments and food-processing equipment.
PEEK, a plastic compatible with the human body, finds its place in implants and medical devices due to its chemical inertness and the fact that it conforms to the sterilization processes. These materials are the first who ensure safety and hygiene, and they are the ones that are able to meet very strict industry standards.
Corrosion-Resistant Options
Stainless Steel 304 and HDPE are the best materials for outdoor and marine environments. Stainless Steel 304 is also a material that has the property of corrosion resistance from saltwater and thus can be used in the manufacture of boat hardware and coastal signage.
HDPE is a highly durable plastic and it is also used in outdoor furniture and piping systems because of its flexibility and the fact that it is resistant to UV radiation. Both materials reduce the need for maintenance in harsh conditions; thus, their use in environmental considerations like minimizing waste through the use of durable materials is highly appropriate.
Environmental and Sustainability Considerations
After performance and cost were optimized, choosing sustainable materials and reducing waste gives the greenest CNC machining projects. The current theme is the use of recyclable materials and the adoption of waste-minimizing strategies that are in harmony with environmental goals.
Recyclable Materials
Aluminum is the most eco-friendly material, as it is highly recyclable, a significant point that is mentioned in competitor articles. While steel is actually much harder to recycle than aluminum, the recycling process for steel uses more energy than for aluminum, which can maintain its features through different cycles and is thus the most appropriate one for the green projects.
Plastics are the ones that definitely cannot meet the features of environmental sustainability in full: ABS and PP are hardly recyclable and most of the time they end up in a landfill, in contrast to HDPE and UHMW-PE which have a definitely greener environmental record.
Reducing Waste
Less waste is of utmost importance for the environment. Nesting techniques have got the potential to utilize the materials to the fullest by meaning using parts efficiently on one sheet or block, thereby increasing the leftover material. Minimal scrap parts are typically made of simple geometries to avoid unnecessary cuts. As an illustration, refraining from intricate internal cavities in metal parts or using standard plastic sheet sizes will benefit the environment.
Conclusion
The success of the CNC machining projects will be dependent on the materials that are consistent with a set of performance, cost, and environmental characteristics. For instance, metals like aluminum (aerospace, automotive) and stainless steel (medical, marine) supply strength, while ABS (prototyping) and PEEK (high-temperature environments) are lightweight, durable plastic options. Titanium and HDPE cover only a few markets, like medical implants and outdoor piping.
To come up with custom-made solutions, reach out to CNC machining experts who will assist you in the most efficient use of the material for your next project.
FAQs: CNC Machining Materials & Applications
Can plastic be CNC machined?
Yes. ABS, nylon, and PEEK are common. Plastics machine faster than metals and resist corrosion, but lack structural strength for heavy loads.
What is the most commonly used tool material for CNC machining?
Carbide tools dominate due to their hardness and durability. High-speed steel (HSS) tools are cheaper but wear faster. Diamond-coated tools are used for machining hard materials like composites.
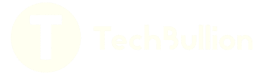