Biotech manufacturing has long relied on globally distributed supply chains for access to affordable materials, specialized technologies, and efficient production at scale. However, recent trade policy fluctuations, supply chain shocks, and geopolitical tensions have prompted a strategic rethink. As the industry grapples with the consequences of over-reliance on distant suppliers, nearshoring—the practice of relocating production closer to end-use markets—is emerging as a serious alternative.
The Push Toward Supply Chain Resilience
Global biotech supply chains are built on interdependence. Active pharmaceutical ingredients (APIs), specialized bioreactors, reagents, and custom lab equipment frequently cross multiple borders before reaching final production facilities. While this structure has traditionally optimized for cost and efficiency, it has also proven fragile in the face of external disruptions.
The pandemic underscored these vulnerabilities, and more recently, trade tensions have made matters worse. For instance, how on-again, off-again tariffs impact supply chains is now a top concern among executives, who are being forced to account for unpredictability in costs, delivery timelines, and regulatory compliance.
Nearshoring presents an opportunity to reduce this uncertainty by shortening transit routes, aligning manufacturing with local regulations, and enhancing responsiveness. By maintaining production within closer proximity to key markets, organizations can react more quickly to disruptions, adjust to regulatory shifts in real time, and reduce their exposure to international shipping delays or embargoes.
Benefits of Nearshoring for Biotech
Relocating manufacturing to nearby countries or within domestic borders provides several strategic advantages:
- Reduced transit time and customs risk: Shorter supply routes mean quicker delivery of materials and finished products, which is critical in time-sensitive R&D and clinical trials.
- Improved regulatory alignment: Local or regional facilities operate under familiar legal frameworks, reducing complexity in quality assurance and compliance.
- Better risk management: Nearshoring reduces exposure to volatile foreign trade policies, tariffs, and political instability.
- Increased visibility and control: Proximity to suppliers and manufacturing partners enables tighter collaboration and real-time decision-making.
- Enhanced sustainability: Reduced transport distances and emissions help companies meet ESG goals and regulatory requirements on environmental performance.
These benefits not only improve operational resilience but can also accelerate the pace of innovation—an essential factor in biotech’s competitive landscape. For instance, a drug developer conducting Phase II trials can mitigate costly delays if materials arrive within days rather than weeks, allowing for quicker iteration and faster regulatory filings.
Tradeoffs and Challenges
Despite its promise, nearshoring comes with challenges. Domestic or regional facilities often involve higher labor and infrastructure costs. Companies may also face limited availability of skilled biotech workers or specialized equipment in some regions. The transition itself can be disruptive and expensive, requiring validation of new sites, requalification of suppliers, and updates to regulatory filings.
Moreover, existing global partnerships may be difficult to unwind due to long-term contracts, intellectual property considerations, or the lack of equivalent capabilities nearby. Building trust with new suppliers or partners can take years, especially in regulated industries where quality consistency is paramount.
According to Deloitte’s 2024 Global Life Sciences Outlook, companies are increasingly weighing these tradeoffs as they build long-term supply chain strategies that blend both global and regional models. The shift is not simply about cost—it’s about strategic adaptability, risk diversification, and operational agility.
Hybrid Models: The Best of Both Worlds?
Rather than choosing between global sourcing and nearshoring, many biotech firms are adopting hybrid models. This includes:
- Strategic regional hubs for critical operations like fill-finish manufacturing or cold-chain logistics.
- Localized sourcing of raw materials with global oversight on formulation and packaging.
- Collaborative partnerships with domestic research institutions and CDMOs (Contract Development and Manufacturing Organizations).
Hybrid approaches allow for better business continuity, as they reduce dependence on any single supplier or geography. Companies can also tailor their strategies based on product type—critical therapies with short shelf lives may benefit more from nearshoring, while bulk generics can remain in low-cost offshore facilities.
This model also opens the door for better collaboration between R&D teams and manufacturing. When production is located nearby, feedback loops between scientists and production engineers can be shorter and more effective, leading to greater efficiency and innovation.
Policy and Infrastructure Considerations
Governments are also playing a role in supporting nearshoring efforts. Incentives such as tax credits, expedited regulatory pathways, and investment in local infrastructure are helping to reduce barriers to domestic biotech manufacturing.
For example, the U.S. government’s National Biotechnology and Biomanufacturing Initiative outlines a roadmap for building resilient bioeconomy infrastructure, including support for regional production capabilities. Similar policies in the EU and Asia are creating a competitive environment where nearshoring becomes not only viable but strategically advantageous.
In addition, clusters of innovation such as biotech corridors in Boston, San Diego, and Toronto are already benefiting from these efforts. These ecosystems combine academic research, startup acceleration, and advanced manufacturing under a single geography, enabling localized innovation pipelines that move from discovery to commercialization faster than ever before.
However, public-private collaboration will be critical. Policymakers must continue reducing regulatory barriers, investing in skilled labor development, and supporting small-to-mid-sized biotech firms that may lack the capital to nearshore independently.
Conclusion: Is Nearshoring the Future?
While nearshoring is not a one-size-fits-all solution, it is clearly gaining traction as part of a broader shift toward supply chain resilience and responsiveness. In biotech, where time-to-market and regulatory precision are mission-critical, the ability to localize production can offer a competitive edge.
As companies re-evaluate their operations in light of recent disruptions, nearshoring should be viewed not as a reactive measure, but as a strategic opportunity to future-proof innovation pipelines, reduce dependency risks, and drive long-term growth.
Nearshoring may not replace global supply chains—but it will likely redefine them. The global biotech industry is entering a new era—one where proximity, flexibility, and resilience may matter just as much as cost and scale. Companies that begin the nearshoring conversation now will be better positioned to navigate the uncertainty ahead, without sacrificing the innovation that defines the industry.
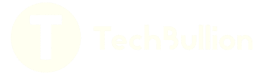