In the ever-evolving domain of advanced manufacturing, where precision, accuracy, and surface integrity converge to determine the performance and lifespan of high-end optical components, one name is emerging as a formidable presence: Adeniyi Kehinde Adeleke. With his groundbreaking master’s thesis titled “Ultraprecision Diamond Turning of Monocrystalline Germanium,” completed in April 2021 at Nelson Mandela University, Adeleke offers not just academic inquiry, but a concrete and transformative solution to one of the most critical challenges in optics and infrared lens production—the precise machining of brittle, hard-to-process materials.
Adeleke’s research arrives at a pivotal moment. Global industries, from aerospace and defense to semiconductor and photonics manufacturing, are racing to enhance the reliability and performance of their infrared systems. These systems depend heavily on lenses with incredibly smooth surfaces—typically requiring surface roughness within the 1–10 nanometer range. At this scale, even microscopic imperfections can lead to scattering, thermal distortion, or catastrophic system failure. Traditionally, materials like monocrystalline germanium, prized for their infrared transparency and thermal conductivity, have been difficult to process without inducing microcracks or surface defects due to their brittle nature.
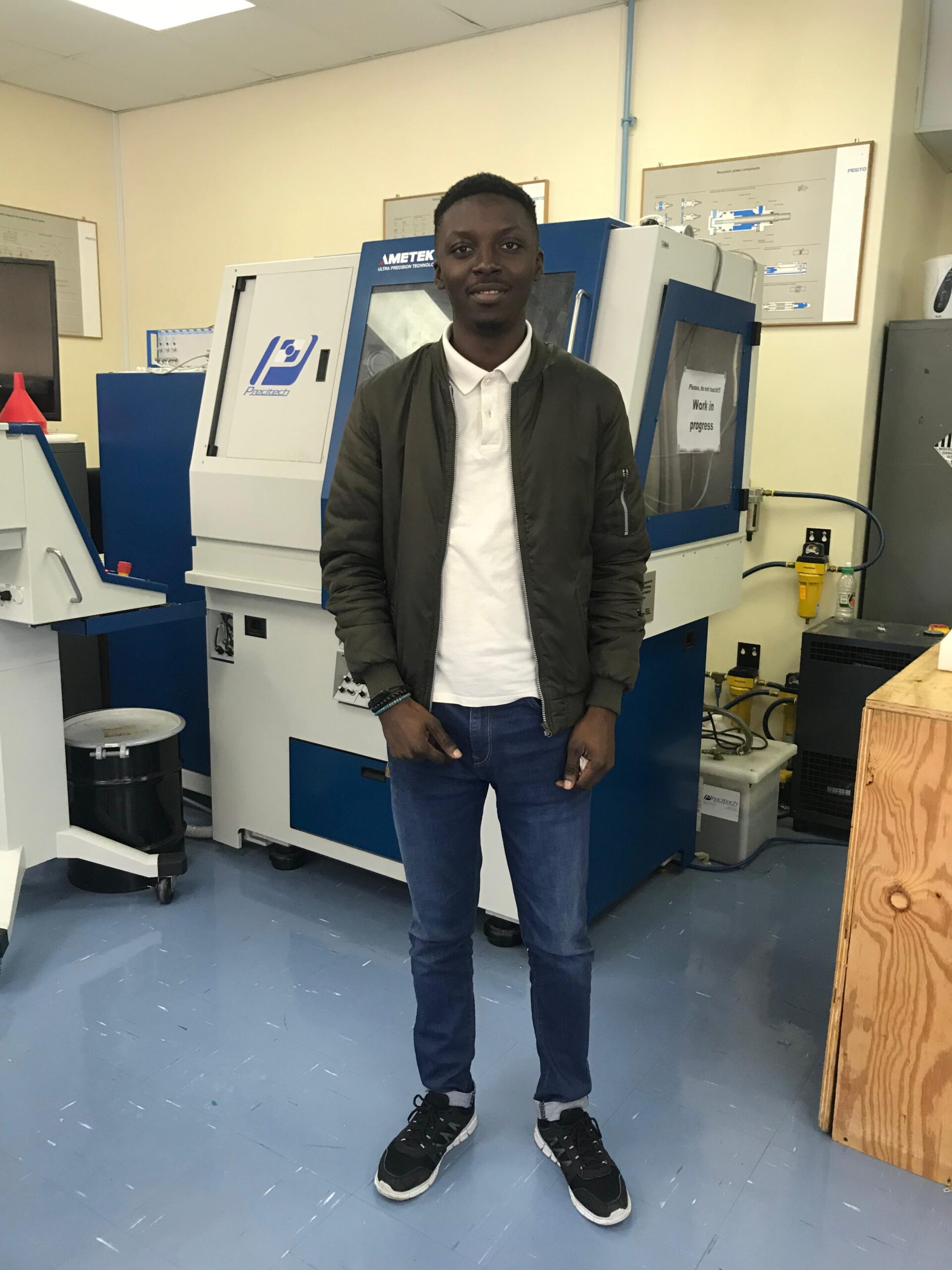
Adeniyi Kehinde Adeleke
That’s where Adeleke’s work breaks new ground. His thesis explores the application of Single Point Diamond Turning (SPDT) in what is known as ductile regime machining, a technique that fundamentally alters how we interact with fragile materials. Rather than cracking or fracturing under tool stress—a common issue with conventional lapping and polishing techniques—germanium, under Adeleke’s optimized conditions, undergoes plastic deformation, resulting in ultra-smooth finishes without structural compromise.
“We’re entering an age where micro-scale accuracy is not a luxury but a necessity,” Adeleke states in his research summary. “Through ultraprecision machining, particularly diamond turning, we can meet the escalating industrial demand for optical components that perform flawlessly in high-stakes environments.”
Redefining Precision Manufacturing Through Diamond Turning
The core of Adeleke’s study lies in the systematic optimization of machining parameters. Using a controlled set of experiments, he examined the behavior of monocrystalline germanium under two different cutting conditions—one using a diamond tool with a 1.5 mm nose radius, the other using a tool with a 1.0 mm radius. These tool geometries were not randomly chosen but were selected using a rigorous Box-Behnken Design approach—an experimental design methodology used for response surface modeling. This allowed Adeleke to map the effects of multiple parameters and their interactions, including spindle speed, feed rate, and depth of cut, on the resulting surface finish.
The experiments were not confined to theory. Practical measurements were taken using the Taylor Hobson PGI Dimension XL profilometer, an industry-grade metrology tool known for its precision in capturing surface topography down to the sub-nanometer level. The results were eye-opening: both tool configurations, under optimal settings, were capable of producing surfaces with roughness levels well within the 1–10 nm range, with minimal deviations—confirming the effectiveness of SPDT in processing brittle materials in the ductile mode.
What makes Adeleke’s work truly revolutionary is not just the execution of experiments, but the incorporation of real-time monitoring and predictive modeling into the process. Recognizing that surface roughness cannot be measured during machining without interrupting production, he turned to Acoustic Emission (AE) sensors—non-intrusive devices that capture high-frequency signals emitted by the workpiece during material deformation. These signals, when analyzed correctly, provide early indications of tool wear, vibration anomalies, and—most importantly—changes in surface integrity.
“Acoustic Emission monitoring brings a real-time layer of intelligence to ultraprecision machining,” Adeleke explains. “It’s like giving the machine a sense of hearing that lets it ‘listen’ to what’s happening during the cut.”
Modeling the Future: ANN and RSM in Predictive Manufacturing
Having gathered experimental and signal data, Adeleke designed predictive models that allow manufacturers to forecast surface roughness before and during machining operations. The deployment of Response Surface Methodology (RSM) enabled him to statistically assess the effect of multiple variables and their interactions. Meanwhile, Artificial Neural Networks (ANN) provided a machine learning-based framework capable of learning from non-linear patterns in the data.
These models became especially powerful when combined with Acoustic Emission (AE) signal features, extracted from both time and time-frequency domains. AE signals serve as an indirect but highly accurate indicator of surface quality and tool condition. By feeding AE-derived features into the ANN, Adeleke demonstrated that surface roughness could be predicted with remarkable precision—without the need to pause machining for physical inspection.
This real-time predictive capability introduces a new era of smart manufacturing. The models developed in this study not only minimize machining downtime but also reduce trial-and-error setups, optimize tool usage, and prevent expensive failures due to tool wear or subpar machining conditions. Adeleke validated the effectiveness of these models using Mean Absolute Error (MAE) calculations, which confirmed the strong correlation between predicted and actual surface roughness measurements.
“We now have the ability to anticipate machining outcomes before defects occur,” Adeleke notes. “This is especially vital when working with materials like germanium, where the margin for error is practically nonexistent.”
From Academic Research to Technological Blueprint
Adeleke’s thesis is both a detailed academic treatise and a roadmap for technological advancement. It bridges classical machining theory with advanced sensor integration, data-driven process optimization, and AI-enabled manufacturing intelligence. This holistic approach makes the research exceptionally relevant for today’s global industry needs.
The implications go far beyond academic interest. In aerospace, sensors and guidance systems demand components that are not only lightweight and thermally stable but also flawlessly precise. In defense systems, missile guidance and surveillance applications rely heavily on optical elements made from materials like germanium. And in semiconductor and photonics manufacturing, SPDT is rapidly becoming the gold standard for shaping and finishing materials used in laser optics, microelectromechanical systems (MEMS), and imaging devices.
Moreover, by proposing hybrid models combining AE and ANN, the study lays the groundwork for the development of closed-loop manufacturing systems, where AI algorithms adjust machining parameters in real-time based on live sensor feedback.
Local Roots, Global Impact
Adeleke’s journey is also a testament to the power of localized academic excellence. Conducted at Nelson Mandela University’s Faculty of Engineering, the Built Environment & Information Technology, the research showcases the global relevance of African innovation. It underscores the capacity of African institutions not just to replicate foreign methodologies, but to pioneer new ones that serve global markets.
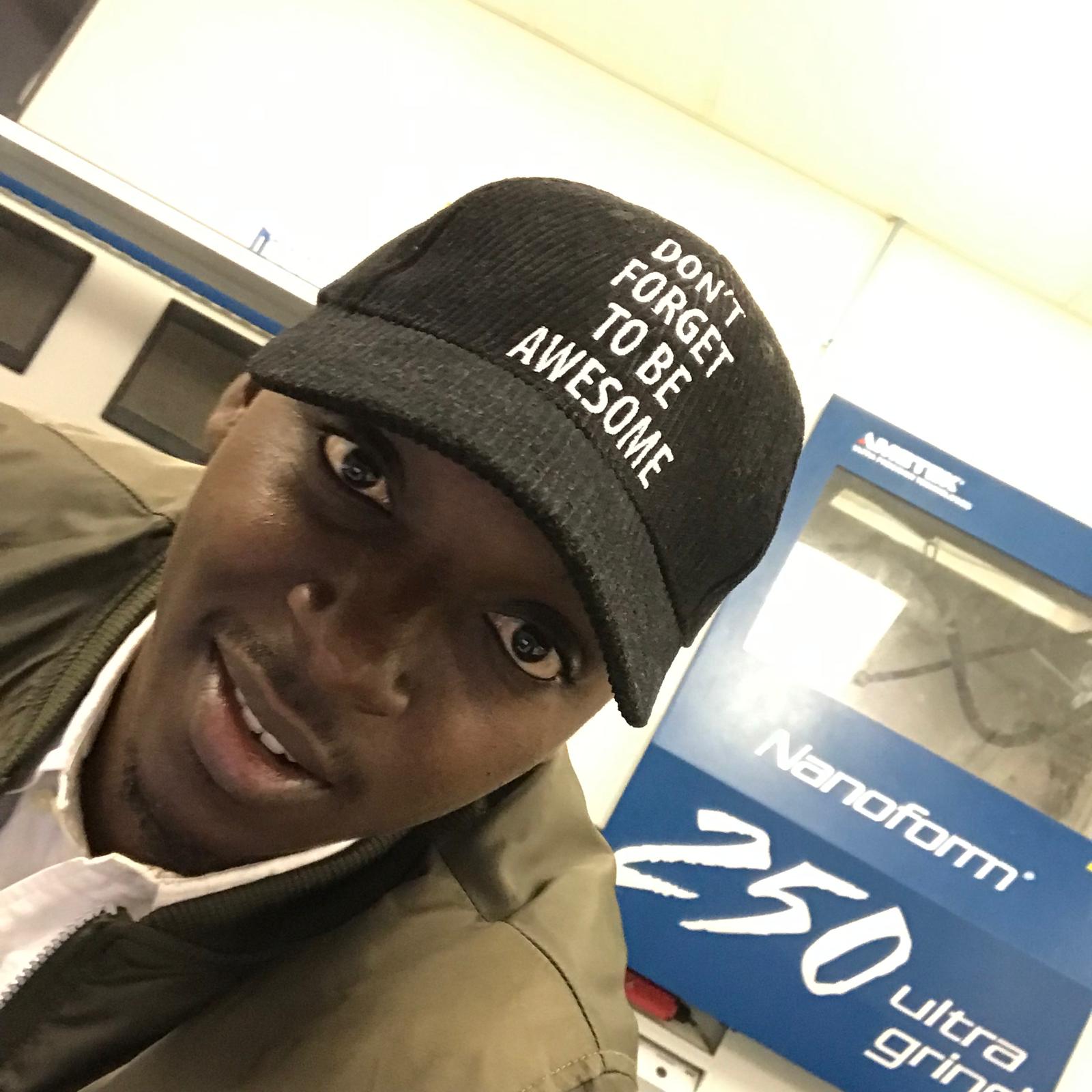
Adeniyi Kehinde Adeleke
Located in South Africa, the university provided Adeleke with access to advanced laboratory infrastructure, computational tools, and academic mentorship. His work has already drawn attention from international manufacturing experts, particularly those focused on high-value optics production and predictive maintenance systems.
“Precision engineering has often been seen as the reserve of industrial superpowers,” notes one faculty member. “What Adeniyi has done is redefine the narrative. He’s shown that with the right mindset and resources, African institutions can lead the world in scientific innovation.”
The Road Ahead: Scaling Innovation
As Adeleke transitions from academic research to industrial application, the possibilities are wide open. The methodologies he developed can be transferred to other brittle materials such as silicon, quartz, or gallium arsenide, all of which are integral to sectors like electronics, photovoltaics, and medical diagnostics.
There is also strong potential for scaling the ANN and RSM models through cloud-based platforms, enabling manufacturers to simulate, analyze, and optimize production conditions in real-time from anywhere in the world. By building a digital twin of the machining process, manufacturers can test configurations virtually before applying them on the shop floor.
With increasing global interest in sustainable and cost-effective manufacturing, Adeleke’s approach also aligns with the principles of the circular economy. By minimizing scrap, extending tool life, and improving process efficiency, his research contributes to greener, smarter, and more resilient manufacturing.
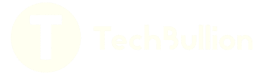