How do engineers keep tiny computer chips from overheating or design huge industrial furnaces that work perfectly? The answer lies in understanding how heat moves. CFD Heat Transfer simulation is a powerful computer tool that lets us see this invisible flow of energy. It helps engineers find and solve heat-related problems in their designs long before anything is built.
At CFDLAND, we help companies master these challenges with our expert CFD heat transfer services. This guide will explain the basics of heat transfer and show how simulation is changing modern engineering.
Figure 1: An overview of CFD Heat Transfer analysis applications, from shell & tube heat exchangers and battery cooling to active cooling in solar panels and natural convection
The science of Heat transfer and importance of CFD heat transfer analysis
Three Ways Heat Moves: Understanding the Mechanisms
Heat always moves from a hotter place to a cooler place. This happens in three different ways, all of which a good CFD thermal modeling study can simulate.
Figure 2: Heat moves from warmer object through the cooler one
-
Conduction: Heat Moving Through Solids
Conduction is heat transfer through direct contact. Imagine touching a hot metal spoon. The heat travels from the spoon directly to your hand. This is conduction. In engineering, a conduction heat transfer simulation is used to see how heat moves through solid parts, like the metal body of an engine or the frame of a building.
-
Convection: Heat Moved by Fluids
Convection is heat transfer through the movement of fluids like air or water. There are two types:
- Natural Convection: This happens when a fluid moves on its own because of temperature. Think of boiling water in a pot. The hot water at the bottom rises, and the cooler water at the top sinks, creating a circular flow that moves heat.
- Forced Convection: This happens when we use something like a fan or a pump to move the fluid. A computer fan blowing air over a hot processor is a perfect example of forced convection.
-
Radiation: Heat Moving as Waves
Radiation is heat that travels as invisible electromagnetic waves. You don’t need any air or water for it. The warmth you feel from the sun or a campfire is radiation. Radiative heat transfer modeling is very important for high-temperature applications like furnaces or for understanding how solar energy heats up a building.
Figure 3: All three heat transfer mechanisms
Advanced Methods in CFD Thermal Analysis
Conjugate Heat Transfer
Many products involve heat moving between a solid part and a fluid. A car radiator is a great example, where heat moves from the solid metal fins into the moving air. A Conjugate Heat Transfer (CHT) analysis simulates both the solid and the fluid at the same time to see exactly how this transfer happens at the interface. This is essential for accurately designing things like heat exchangers and electronics cooling systems.
Figure 4: Temperature distribution in a shell and tube heat exchanger, a classic example of Conjugate Heat Transfer (CHT) analysis.
Phase Change Modeling
Sometimes, a material changes its state, like water boiling into steam. This “phase change” uses a lot of energy and can have a huge impact on heat transfer. Multiphase heat transfer CFD models are used to simulate processes like boiling and condensation, which are critical in power plants and air conditioning systems.
Transient Thermal Analysis
Many systems don’t stay at one temperature. They heat up and cool down over time. A transient thermal analysis simulates how temperature changes moment by moment. This is crucial for understanding the startup process of an engine, the charging cycle of a battery, or how a building responds to the changing sun throughout the day.
Real-World Applications of CFD Thermal Analysis
The true power of CFD thermal analysis is seen in how it solves real-world problems across many industries.
- Electronics Cooling: Modern devices like smartphones and laptops are smaller and more powerful than ever, which means they produce a lot of heat in a small space. Electronics cooling CFD helps engineers design better heat sinks and airflow paths to keep these devices from overheating and failing.
- Heat Exchangers and Industrial Processes: In factories and power plants, moving heat efficiently is key to saving money and energy. A heat exchanger design CFD simulation can optimize the shape and flow inside these devices to maximize their performance.
- Electric Vehicles and Batteries: Batteries work best within a specific temperature range. Battery thermal management CFD is essential for designing cooling systems that keep electric vehicle batteries safe, efficient, and long-lasting.
Figure 5: CFD analysis of an active cooling system for solar panels, designed to improve efficiency by preventing overheating.
- HVAC and Buildings: Designing an efficient heating, ventilation, and air conditioning (HVAC) system is crucial for comfort and energy savings. A building thermal simulation can show how solar heat affects a building and how air circulates in a room, helping architects design more comfortable and “green” buildings.
The CFDLAND.com Difference and Conclusion
Powerful software like ANSYS Fluent is the engine for CFD heat transfer analysis, but a tool is only as good as the expert using it. Getting accurate, meaningful results requires a deep understanding of physics and a careful, systematic approach. Simply running the software is not enough. At CFDLAND, our engineers combine deep software knowledge with years of practical experience to ensure every simulation is not just a colorful picture, but a reliable source of engineering truth.
In conclusion, CFD Heat Transfer simulation is an essential tool for modern innovation. It allows engineers to see and understand complex thermal behavior, test new ideas without expensive physical prototypes, and create products that are safer, more efficient, and more reliable. From the smallest electronic chip to the largest industrial facility, CFD is helping to solve the critical heat challenges of today and build a better-designed future.
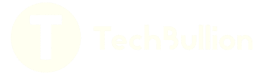