In today’s competitive manufacturing world, precision and customization are key factors driving success across industries. From automotive to aerospace, electronics to plumbing, the demand for custom brass cnc parts continues to grow. Thanks to advances in CNC (Computer Numerical Control) machining, manufacturers can now produce highly detailed, accurate, and durable brass components tailored to specific project needs.
If you’re considering brass for your next project or seeking reliable CNC machining solutions, this guide will help you understand the advantages, applications, and key considerations when ordering custom brass CNC parts.
Why Choose Brass for CNC Machining?
Brass, a versatile alloy of copper and zinc, is widely valued for its exceptional machinability, corrosion resistance, durability, and aesthetic appeal. Its unique combination of mechanical properties makes it a preferred choice for many industries.
Here’s why brass is often selected for CNC machining projects:
- Excellent Machinability
Brass is one of the easiest metals to machine. Its softness allows for high-speed cutting with minimal tool wear, making production more efficient and cost-effective.
- Dimensional Accuracy
Thanks to its stable composition, brass allows for tight tolerances and high precision during CNC milling, turning, and drilling processes.
- Corrosion Resistance
Brass exhibits excellent resistance to corrosion, especially from water and other environmental factors. This makes it ideal for plumbing fixtures and marine applications.
- Electrical Conductivity
Brass has good electrical conductivity, making it suitable for electronic connectors and terminals.
- Aesthetic Appeal
The gold-like appearance of brass makes it a popular choice for decorative and architectural applications where appearance matters as much as function.
Applications of Custom Brass CNC Parts
Custom brass CNC parts serve a variety of functions across multiple industries. Some of the most common applications include:
- Automotive Industry
Brass CNC parts are used for fuel system components, valves, and fittings due to their durability and resistance to corrosion.
- Electronics
Brass’s conductivity and machinability make it ideal for manufacturing electrical connectors, pins, sockets, and switch components.
- Plumbing and HVAC
Brass parts such as couplings, adapters, valves, and faucet components are widely used in plumbing systems for their longevity and resistance to water damage.
- Aerospace
Though used in non-critical applications, brass CNC parts still play a role in lightweight fittings, instruments, and non-magnetic components in the aerospace industry.
- Architectural and Decorative Items
Brass’s appearance makes it suitable for hardware, door handles, light fixtures, and custom decorative elements.
CNC Machining Processes for Brass Parts
Producing custom brass CNC parts involves several precise machining processes. Common CNC operations include:
- CNC Turning
Ideal for cylindrical parts like bushings, shafts, and rings, turning shapes the exterior and interior surfaces with great precision.
- CNC Milling
For more complex shapes, flat surfaces, slots, and detailed contours, CNC milling is the preferred method.
- Drilling and Boring
Used to create accurate holes and internal passages in brass components.
- Threading
Both internal and external threading for brass fittings and connectors.
- Surface Finishing
After machining, brass parts often undergo finishing processes like polishing, plating, or coating to enhance their appearance and durability.
Advantages of Custom CNC Machined Brass Parts
Opting for custom CNC machining for brass components offers several benefits:
- High Precision
CNC machines can produce complex geometries with tight tolerances, making them ideal for parts that require exact specifications.
- Consistency Across Batches
Whether you need one prototype or thousands of parts, CNC machining ensures that each part meets the same high standard.
- Short Turnaround Times
With brass being easy to machine and CNC setups being fast and efficient, you can expect quicker production runs compared to traditional machining.
- Cost Efficiency
Brass’s machinability reduces tool wear and machining time, making production more affordable, especially for larger quantities.
- Customization Flexibility
You can easily specify dimensions, tolerances, surface finishes, and other features to suit your exact project requirements.
Types of Brass Alloys Used in CNC Machining
Different projects require different types of brass alloys. Commonly used brass grades include:
- C360 Free-Machining Brass: Known for exceptional machinability and widely used in precision turned parts.
- C260 Cartridge Brass: Offers good corrosion resistance and is often used in decorative items and fittings.
- C464 Naval Brass: Highly resistant to seawater corrosion, making it ideal for marine applications.
- C230 Red Brass: Frequently used for plumbing fixtures and electrical connectors.
When ordering custom brass CNC parts, specifying the correct alloy is crucial for meeting performance expectations.
Choosing the Right CNC Machining Partner: Key Steps
- Assess Experience: Choose a partner with proven expertise in CNC machining, especially for your required materials like brass, aluminum, or steel.
- Check Equipment and Technology: Ensure they use modern CNC machines capable of delivering tight tolerances and complex geometries.
- Review Quality Control: Look for providers with strict quality assurance processes, including in-process inspections and final checks.
- Evaluate Customization and Support: A good partner offers design feedback, prototyping, and engineering support.
- Confirm Lead Times and Capacity: Make sure they can meet your production schedule and scale up as needed.
- Check Client Reviews: Look for positive testimonials and case studies.
Surface Finishing Options for Brass CNC Parts
Post-machining finishing enhances both the appearance and functionality of brass parts. Popular finishing options include:
- Polishing: For a bright, reflective surface.
- Plating: Nickel, chrome, or gold plating to improve corrosion resistance or aesthetic appeal.
- Anodizing (Limited Use on Brass): Other protective coatings may be used.
- Passivation: Reduces surface reactivity.
- Laser Engraving: For part numbers, logos, or functional markings.
Finishing selection depends on the intended application and aesthetic preferences.
How to Choose the Right CNC Machining Partner for Brass Parts
Selecting the right machining service provider is essential for quality and cost-efficiency. Here are some factors to consider:
- Experience with Brass
Not all machine shops specialize in brass. Choose a provider with proven experience in machining brass components.
- Advanced Equipment
Ensure the shop uses modern CNC milling and turning equipment capable of tight tolerances and high production speeds.
- Customization Support
Look for providers who offer engineering support, prototyping services, and design for manufacturability (DFM) feedback.
- Quality Assurance
Reputable CNC shops provide in-process inspections, final quality checks, and documentation to ensure every part meets your specifications.
- Lead Times and Scalability
Consider lead times and the shop’s ability to scale production if your demand grows in the future.
Conclusion:
Invest in Precision with Custom Brass CNC Parts
When your project demands precision, reliability, and aesthetic excellence, custom brass CNC parts provide the ideal solution. From small-scale prototypes to high-volume production runs, CNC machining delivers parts that meet tight tolerances and specific design requirements.
With the right material selection, professional machining, and appropriate surface finishing, you’ll receive brass components that not only perform well but also offer long-term durability.
If you’re ready to bring your brass component project to life, partner with a trusted CNC machining service provider specializing in custom brass solutions. Their expertise will ensure you get the quality, precision, and service your project deserves.
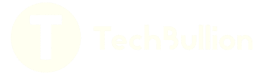