What Are MIM Parts?
MIM parts, or Metal Injection Molding parts, are high-precision components produced using a combination of plastic injection molding and powdered metallurgy. This advanced manufacturing process allows for the creation of complex metal parts with excellent dimensional accuracy, surface finish, and mechanical properties.
MIM is widely used across industries including automotive, aerospace, medical devices, consumer electronics, defense, and industrial equipment. Companies like Jiangsu JH MIM Technology Co., Ltd are at the forefront of delivering high-quality MIM parts for a global client base.
The Metal Injection Molding Process
Step-by-Step Production Method
- Mixing: Fine metal powders are combined with a thermoplastic binder to form a feedstock.
- Injection Molding: The feedstock is injected into a mold cavity, forming a “green part.”
- Debinding: The binder is removed from the molded part through chemical or thermal processes.
- Sintering: The debound part is heated to near the metal’s melting point, densifying it into a solid component with properties close to wrought metals.
This four-step process enables the production of intricate shapes that would be difficult or expensive to achieve through traditional machining or casting.
Advantages of MIM Over Traditional Methods
- High Precision: MIM parts maintain tight tolerances with minimal post-processing.
- Material Flexibility: A wide range of metals, including stainless steel, titanium, and magnetic alloys, can be used.
- Cost-Effective: Ideal for high-volume production runs where tooling costs are amortized.
- Design Freedom: Complex geometries, undercuts, and internal threads are possible.
- Minimal Waste: Near-net shape reduces material loss compared to CNC machining.
Applications of MIM Parts
Medical Devices
MIM is extensively used in the production of surgical instruments, orthodontic brackets, and implants. These applications require high biocompatibility, strength, and intricate geometries, all of which MIM provides.
Automotive Industry
MIM parts such as sensor housings, turbocharger components, and fuel system parts are increasingly replacing machined or cast parts. Their strength, precision, and repeatability meet stringent automotive standards.
Consumer Electronics
With the miniaturization of electronic gadgets, MIM offers a scalable solution for producing small, detailed components like phone buttons, camera modules, and internal structural frames.
Aerospace and Defense
MIM components are used in locking mechanisms, safety triggers, and fuel nozzles, offering high strength-to-weight ratios and corrosion resistance critical to aerospace and defense environments.
Why Choose JH MIM for MIM Parts?
Jiangsu JH MIM Technology Co., Ltd specializes in delivering custom MIM solutions with state-of-the-art manufacturing capabilities. The company stands out for:
- ISO-Certified Quality: Adheres to ISO 9001 and IATF 16949 standards.
- Material Expertise: Offers stainless steel, low alloy steel, titanium, and more.
- Precision Tooling: Uses advanced mold-making and automation systems.
- Global Distribution: Serves clients in North America, Europe, and Asia.
- R&D Support: Assists clients in design optimization and material selection.
Their comprehensive capabilities ensure fast turnaround, high-quality outputs, and cost-efficiency across industries.
Key Considerations in MIM Design
Design for Manufacturability
While MIM allows for complex shapes, certain design guidelines must be followed:
- Uniform wall thickness to reduce shrinkage variation
- Rounded corners instead of sharp edges
- Avoidance of excessively thin walls or deep holes
Incorporating these principles early in the design phase ensures smoother production and optimal performance.
Material Selection
The choice of material depends on the application. For example:
- 316L Stainless Steel: Excellent corrosion resistance, ideal for medical and food-grade parts.
- 17-4PH: High strength and moderate corrosion resistance for aerospace and defense.
- Soft Magnetic Alloys: Used in electronic and automotive sensors.
A professional MIM supplier like JH MIM can assist in selecting the most suitable alloy.
MIM vs Other Manufacturing Methods
Method | Complexity | Cost per Unit | Volume Suitability | Material Waste |
MIM | High | Low (high volume) | High-volume production | Minimal |
CNC Machining | Moderate | High | Low to medium | High |
Die Casting | Moderate | Moderate | High-volume | Moderate |
Investment Casting | High | High | Low to medium | Moderate |
MIM is particularly beneficial when producing small, complex parts in large volumes where dimensional precision and fine surface finish are required.
Sustainability and MIM
MIM is an environmentally favorable process due to its:
- High material efficiency
- Minimal post-processing
- Energy-efficient sintering compared to full melting
- Reduced scrap rates compared to machining
As industries move toward greener production models, MIM stands out as a sustainable alternative.
Final Thoughts
MIM parts are transforming modern manufacturing by enabling the production of intricate metal components with remarkable accuracy, strength, and cost-effectiveness. Industries from medical to aerospace benefit from this technology, and trusted suppliers like JH MIM Technology Co., Ltd play a critical role in its adoption and evolution.
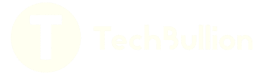