Material testing is one of the most important steps in product development and quality control. It helps manufacturers understand the strength, durability, and safety of their materials before these materials are used in real-world conditions. Whether testing metals, plastics, rubber, or composites, selecting the correct equipment directly affects the results accuracy.
Different industries require different testing equipment. For example, a construction company may need a compression tester for concrete blocks, while an automotive factory may use an impact tester to measure how car parts respond to sudden force. Using the wrong machine or outdated technology can result in poor-quality products and safety failures.
Choosing the right material testing equipment depends not only on what you are testing, but also on the standards you must meet, the precision your tests require, and the long-term service you will need. In this article, you will learn how to select the most appropriate testing equipment for your specific needs and why it is important to work with a reliable supplier who can provide support, spare parts, and maintenance over time.
Key Factors That Influence Equipment Selection
Choosing the right material testing equipment starts with understanding what needs to be tested and how. The type of material—such as metal, plastic, rubber, composite, or concrete—will determine the kind of test you must perform. Each test requires a different machine, and selecting the wrong one may lead to inaccurate results.
As an example, if you need to test metal samples’ tensile strength, you will likely use a Universal Testing Machine (UTM). These machines can also perform compression and flexural tests, making them suitable for many materials. If your goal is to measure how hard a material is, you will need a hardness tester. Common types include Rockwell, Vickers, and Brinell hardness testers. To evaluate how a material responds to sudden force or shock, you may need an impact tester, such as a Charpy or Izod machine. For parts that withstand repeated use, fatigue testing machines simulate long-term stresses.
Apart from the test type, you must consider accuracy and repeatability. Equipment must meet standards such as ASTM E8 for tensile testing or ISO 6508 for Rockwell hardness testing. Testing machines must provide precise results, especially when used in industries where safety and performance are critical.
Another important factor is automation. Some laboratories prefer fully automatic machines with built-in software and sensors, which reduce human error. Others may choose manual machines due to lower costs or a simpler setup.
Matching Equipment to Industry Requirements
Every industry has different testing requirements based on the materials they use and the standards they must follow. Selecting the right testing equipment means understanding these differences and choosing machines that fit your specific industrial needs.
In the construction industry, one of the most common tests is compressive strength testing for concrete. This is usually done using a concrete compression testing machine, which can apply high levels of force, often up to 2000 kN, to test how much pressure a concrete sample can withstand before failing. Construction companies may also use moisture analyzers to check water content in aggregates and concrete mixes, which affects strength and durability.
Automotive industry manufacturers need to test vehicle components under stress. This includes fatigue testing machines that simulate real-world vibrations and repeated use. Impact testers, such as Charpy or drop weight machines, are used to examine how parts react to sudden collisions.
Aerospace requires extremely precise and reliable testing equipment. Materials used in aircraft must be tested for strength, fatigue, and even minor deformations. For this reason, aerospace companies often use advanced Universal Testing Machines with precise extensometers and computer control. In addition, they use non-destructive testing (NDT) equipment, such as ultrasonic flaw detectors, to check for internal defects without damaging the material.
The plastics and rubber industry relies on machines like the Mooney Viscometer, which measures rubber compounds’ viscosity, and the Moving Die Rheometer (MDR), which tests curing behavior. These devices help guarantee that rubber products like seals and tires meet performance standards.
Why the Right Supplier Matters as Much as the Equipment
Even the best material testing equipment can fail to deliver results if it is not supported by a reliable supplier. When choosing testing machines, it is worthwhile to think not only about the technical features of the equipment, but also about who will supply, install, and maintain it.
A professional supplier does more than just sell the machine. They help select the correct model based on your industry, material type, testing standards, and daily workload. For example, a supplier may recommend a 150 kN UTM with a digital extensometer for testing metals in a manufacturing plant or a fully automated Vickers hardness tester for a laboratory that handles hundreds of samples per week.
Once the equipment is delivered, proper installation and training are critical. A reliable supplier will send a technician to set up the machine and teach your team how to use it safely and correctly. This reduces errors and increases equipment lifespan.
Maintenance is another key factor. Testing machines need regular calibration to meet international standards such as ISO 17025 or ASTM E4. If the machine is not properly maintained, the test results may become incorrect. A good supplier offers scheduled servicing, remote diagnostics, and on-site support.
Access to spare parts is also a necessity. Over time, parts such as load cells, grips, electronic boards, or sensors may need replacement. A reliable supplier keeps these parts in stock and delivers them quickly to reduce downtime. In contrast, buying from a low-cost, unknown brand can lead to long delays or complete replacement of the machine if parts are unavailable.
Modern machines, such as CNC specimen preparation systems and touchscreen-controlled impact testers, require software updates and technical adjustments over time. A trustworthy supplier will provide updates, manuals, and user support for these systems.
Final Considerations for Long-Term Testing Success
Selecting the right material testing equipment affects every part of the production and quality control process. The correct machine helps to make certain that materials meet the strength, durability, and safety requirements. It also helps companies follow national and international testing standards, avoid failures, and protect their reputation.
The key is to choose equipment based on the type of material you work with, the tests you need to perform, and the standards you must meet. This includes using machines like Universal Testing Machines, hardness testers, impact testers, or specialized systems such as the Mooney Viscometer or MDR. These tools must be accurate, reliable, and supported by certified data output.
Just as important as the equipment itself is the supplier you choose. A reliable supplier will provide full support from selection to installation and long-term service. This includes technical advice, regular maintenance, calibration, and quick access to spare parts. Working with the right partner guarantees consistent, compliant, and cost-effective testing.
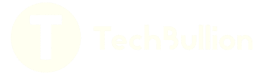