The manufacturing sector has undergone a profound transformation. At the heart of this revolution lies smart manufacturing—an advanced approach to production that relies heavily on digital technologies. Among these technologies, the Internet of Things (IoT) stands out as a critical enabler. By integrating IoT into production lines, manufacturers are achieving new levels of efficiency, precision, and adaptability.
Understanding Smart Manufacturing and the Role of IoT
Smart manufacturing refers to the use of interconnected systems and data analytics to improve manufacturing performance. Unlike traditional manufacturing methods, which often operate in silos, smart manufacturing focuses on connectivity and real-time decision-making.
IoT, or the Internet of Things, is a key driver of this approach. It involves embedding sensors, software, and other technologies into physical devices. These devices then collect and share data over a network without requiring human intervention. When applied to manufacturing, IoT devices monitor equipment, track product movement, and ensure optimal working conditions.
By enabling real-time data collection and communication, IoT bridges the gap between digital planning and physical execution. As a result, it becomes easier to maintain quality, reduce waste, and anticipate system failures before they disrupt production.
Key Benefits of IoT Integration in Manufacturing Processes
Integrating IoT into production lines offers a wide array of benefits. Below are some of the most significant advantages:
Enhanced Operational Efficiency
Firstly, IoT enables manufacturers to automate many repetitive and manual tasks. Sensors collect data on machine performance, temperature, pressure, and more. This data is then analyzed to determine whether the machine is operating within optimal parameters. Consequently, companies can reduce downtime and improve machine utilization.
Predictive Maintenance Reduces Unplanned Downtime
Traditionally, machines were either maintained on a fixed schedule or repaired after failure. Both methods are costly and inefficient. However, with IoT sensors, it becomes possible to monitor equipment in real-time and predict when a component is likely to fail. This approach, known as predictive maintenance, helps companies prevent unplanned downtimes and extends the lifespan of equipment.
Improved Quality Control Measures
Another benefit of IoT integration is the enhancement of quality control processes. Sensors can detect variations in production conditions and alert operators immediately. Moreover, historical data can be analyzed to identify patterns associated with defects. As a result, manufacturers can take corrective actions faster and improve overall product quality.
Better Resource Management
Through real-time tracking of raw materials and inventory, IoT improves resource management. Companies can monitor supply levels and automatically trigger reorders when inventory is low. Furthermore, this data helps in reducing overstocking and understocking, both of which are expensive mistakes in manufacturing.
Increased Energy Efficiency
Energy consumption is a significant cost in manufacturing. IoT devices can monitor energy use across different machines and departments. This information helps identify where energy is being wasted and allows companies to optimize energy usage. Therefore, businesses not only cut costs but also contribute to sustainability efforts.
IoT Applications Across Various Manufacturing Stages
IoT is not limited to a single phase of production; rather, it impacts multiple areas across the manufacturing process.
Production Monitoring and Control
IoT-enabled systems provide real-time insights into every aspect of the production line. Sensors track variables such as speed, pressure, temperature, and humidity. Data analytics platforms then process this data to ensure all parameters remain within set thresholds. If an anomaly is detected, alerts are sent to operators for immediate intervention.
Supply Chain and Logistics Management
Beyond the factory floor, IoT enhances supply chain visibility. Smart trackers and RFID tags offer real-time location updates for shipments. This level of transparency allows businesses to make informed decisions and reduce lead times. Consequently, the overall responsiveness of the supply chain improves dramatically.
Safety and Compliance Monitoring
Ensuring workplace safety is a top priority in manufacturing. IoT devices can monitor environmental conditions like air quality, noise levels, and chemical exposure. Additionally, wearables for workers can track fatigue, body temperature, and motion, helping to prevent accidents before they occur.
Asset and Inventory Management
IoT-powered asset management systems automatically track the location, usage, and condition of tools and equipment. This data ensures assets are used efficiently and reduces the chances of theft or misplacement. Similarly, real-time inventory monitoring helps avoid delays caused by stockouts or incorrect stock levels.
Challenges to Overcome in IoT Implementation
Despite its numerous advantages, integrating IoT into manufacturing does present certain challenges.
Data Security and Privacy Concerns
One of the primary concerns is data security. With so many connected devices transmitting sensitive information, the risk of cyberattacks increases. Manufacturers must implement robust cybersecurity measures, such as encryption and multi-layer authentication, to protect their networks.
High Initial Investment
Implementing an IoT ecosystem requires a significant upfront investment. Sensors, connectivity infrastructure, and analytics platforms all come at a cost. While the long-term benefits are substantial, smaller companies may struggle with the initial financial burden.
Data Overload and Analysis
Another challenge is managing the vast amounts of data generated. Without proper analytics tools, manufacturers can become overwhelmed and fail to derive actionable insights. Therefore, investing in intelligent data processing systems is essential for success.
Integration with Legacy Systems
Many manufacturing facilities still rely on older machinery and software systems. Integrating these legacy systems with modern IoT technologies can be complex and time-consuming. Often, it requires customized solutions and specialized expertise.
Strategies for Successful IoT Integration in Production
To overcome the above challenges and maximize the benefits of IoT, manufacturers must adopt a strategic approach:
Start Small and Scale Gradually
Rather than overhauling the entire production line, companies should begin with a small pilot project. This approach helps in identifying potential issues and refining strategies before full-scale implementation.
Invest in Employee Training
Employees must understand how to use new technologies effectively. Offering training programs and workshops ensures that staff can operate IoT systems safely and efficiently.
Collaborate with Technology Partners
Partnering with IoT solution providers brings in technical expertise and accelerates deployment. These partnerships also provide access to ongoing support and updates, ensuring the system remains current.
Prioritize Cybersecurity Measures
To prevent breaches, manufacturers should implement strong data security protocols from the outset. Regular audits, firewall protection, and encrypted communication channels are essential components of a secure IoT infrastructure.
The Prospect of Smart Manufacturing with IoT
Looking ahead, the integration of IoT in manufacturing is expected to grow exponentially. Technologies like artificial intelligence (AI), machine learning, and 5G connectivity will further enhance IoT capabilities. These advancements will enable even faster data processing, deeper insights, and more autonomous operations.
Moreover, the shift towards Industry 5.0—where human and machine collaboration is prioritized—will see IoT play a pivotal role. Intelligent systems will not only optimize production but also adapt to human needs, ensuring a more personalized and efficient manufacturing process.
Conclusion
In summary, integrating IoT in production is no longer optional; it is a necessity for manufacturers aiming to thrive in the digital era. From improving efficiency and reducing downtime to enhancing product quality and safety, the benefits are vast and undeniable. Although challenges exist, they can be effectively managed through strategic planning, investment in training, and a strong cybersecurity framework.
As industries continue to evolve, smart manufacturing powered by IoT will lead the way toward greater innovation and sustainability. Companies that embrace this transformation early will not only gain a competitive edge but also set the benchmark for future-ready manufacturing
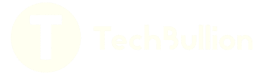