If you’ve ever wondered what it takes to bend steel the size of a billboard, this one’s for you.
It all started with a pretty simple goal: reshape massive steel plates—each about 145 inches long and more than a third of an inch thick—into curved supports for a big public venue in Los Angeles—the kind of place you’d recognize instantly from the skyline. The catch? The forming process had to be precise, strong enough to support thousands of fans, and clean enough to ship and install without rework.
And to do that, California Steel Services brought out the big tools.
What Does 2,000 Tons of Pressure Actually Look Like?
Imagine flattening a shipping container—or crushing a full-size car until it’s the size of a lunchbox. That’s the kind of force a 2,000-ton press brake applies when bending thick steel.
This isn’t about brute strength alone. It’s about control. Every bend, every degree, has to be exact, especially when you’re working with ASTM A572-50, a high-strength structural steel grade commonly used in bridges and stadiums.
Why This Project Was Tricky
This wasn’t a typical steel bending job. A few things made it more complex:
- The plates were massive—145 inches long
- The required bend radius was massive (over 160 feet for some sections)
- The material was thick, high-strength steel
Standard shop equipment wouldn’t cut it. That’s why CalSteel used its 2,000-ton press brake—one of the few machines in the region with enough power to pull this off.
How They Bent Steel This Big (Step by Step)
Here’s a breakdown of how the team shaped these giant plates without a single redo:
- Cut to Length
-
- First, each steel sheet was plasma-cut to size. That meant cleaning up the edges, squaring the ends, and removing burrs so nothing messed with the bend.
- Measure and Mark
-
- Operators used layout tools and chalk lines to mark precisely where each bend should go, including spring-back compensation (because steel tends to push back after bending).
- Position Under the Press Brake
-
- These plates are heavy—really heavy. So an overhead crane lifted each one into place, and operators used wedges and hydraulic supports to align everything perfectly.
- Bend in Stages
-
- A bend this big can’t happen in one shot. The team used incremental presses to shape the curve slowly, rotating and re-aligning the plate between each step.
- Check and Double-Check
- After forming, they measured every profile against CAD drawings using laser tools and radius templates. The goal? Ship the steel without any tweaks or cutting on-site.
So, Did It Work? Yes. The formed profiles were installed exactly as intended. No adjustments, no time lost.
More Than Just Steel
According to Tito Martinez, one of CalSteel’s sales reps, the project meant more than specs and measurements:
“We’re all based in the LA area, so working on a venue like this—one that people in our community love—was something special. It’s one of those jobs you don’t forget.”
Where Projects Like This Go Next
If you’re in construction or fabrication, here’s the cool part: projects like this aren’t limited to LA. California Steel Services serves contractors and builders across California, Nevada, Oregon, and Washington with precise metal forming solutions. With an in-house truck fleet and the equipment to shape large-radius, heavy-gauge steel, they help with everything from public venues to industrial builds.
So, next time you see a stadium, arena, or even a high-traffic public space, you might be standing above a plate that went through 2,000 tons of force and a lot of planning.
Read more: techbullion.com
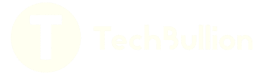