In an era where sustainability is becoming a cornerstone of industrial development, powder metallurgy (PM) has emerged as a key player in eco-friendly manufacturing. This innovative process combines environmental responsibility with high performance, making it a preferred choice in sectors such as automotive, aerospace, medical devices, and electronics. But what exactly makes powder metallurgy sustainable, and why is it gaining global attention?
This article explores the fundamentals of powder metallurgy, its sustainability benefits, and its growing importance in modern manufacturing.
What is Powder Metallurgy?
Powder metallurgy is a manufacturing process that involves producing metal powders and shaping them into functional components using compaction and sintering. Instead of melting raw metal and casting it into shapes, PM allows manufacturers to form parts from powdered metals at lower temperatures and with minimal waste.
The powder metallurgy process typically includes the following steps:
- Powder Production – Metal powders are created through techniques like atomization, reduction, or electrolysis.
- Blending and Mixing – Powders are mixed with lubricants or other metal powders to achieve desired properties.
- Compaction – The powder mixture is compressed into a die to form a “green” compact.
- Sintering – The green compact is heated in a controlled atmosphere to bond the metal particles and achieve final strength.
- Secondary Operations – These may include sizing, machining, or heat treatment to improve precision and performance.
The entire process operates at relatively low energy levels and generates minimal scrap, making it inherently sustainable compared to traditional methods.
Sustainability Advantages of Powder Metallurgy
1. Material Efficiency
One of the biggest sustainability wins of powder metallurgy is its near-zero waste approach. Traditional machining involves cutting metal from a larger block, which leads to significant material loss in the form of chips and shavings. In contrast, PM uses only the amount of material needed to form the part, resulting in minimal scrap.
This efficient use of resources significantly reduces raw material consumption, which is not only cost-effective but also environmentally responsible.
2. Energy Savings
Unlike conventional casting or forging methods, powder metallurgy does not require melting metals at high temperatures. Sintering occurs below the melting point, dramatically lowering the energy requirements. This leads to a reduced carbon footprint and supports energy conservation—two vital goals in sustainable manufacturing.
3. Lower Emissions and Pollution
Since PM avoids high-temperature processes and chemical-intensive treatments, it produces fewer greenhouse gases and pollutants. Additionally, the absence of coolants and cutting fluids—often used in traditional machining—means fewer harmful chemicals enter the waste stream.
4. Recyclability
Metal powders used in powder metallurgy are often derived from recycled materials. This circular economy approach makes PM even more sustainable, as it gives waste metals a second life. Unused powders from production can also be reclaimed and reused.
5. Lightweight Components
Powder metallurgy can create parts with complex geometries and tailored porosity. This allows for the development of lightweight components, especially important in the automotive and aerospace industries, where reducing weight translates into improved fuel efficiency and lower emissions.
Applications of Powder Metallurgy
Thanks to its versatility, powder metallurgy is used in a wide array of industries:
- Automotive – Manufacturing of gears, bushings, and brake pads
- Aerospace – Lightweight structural parts and turbine components
- Medical – Orthopedic implants and surgical tools
- Electronics – Magnetic materials and conductive components
- Defense – Ammunition and precision parts
The ability to produce durable, high-performance parts with complex shapes makes PM a cost-effective alternative to conventional metalworking methods.
Challenges and Innovations
While powder metallurgy offers numerous benefits, it does come with challenges such as:
- Limited Size Range – PM is generally more suitable for small to medium-sized parts.
- Tooling Costs – High initial costs for molds and dies can be a barrier for low-volume production.
- Material Limitations – Not all metal alloys are suitable for powder processing.
However, ongoing research and technological advancements are addressing these issues. Additive manufacturing (3D printing using metal powders) is one such innovation expanding the capabilities of PM. This allows for rapid prototyping and complex part fabrication without the need for extensive tooling.
Moreover, developments in metal powder production and hybrid materials are improving the quality, affordability, and environmental impact of PM components.
Choosing the Right Powder Metallurgy Supplier
For businesses looking to integrate PM into their manufacturing process, selecting a reliable powder metallurgy supplier is crucial. The supplier should offer:
- High-quality metal powders with consistent properties
- Customization for specific applications
- Compliance with industry standards
- Proven experience across various sectors
- Sustainable practices in sourcing and production
A reputable supplier can help optimize the powder metallurgy process to meet both performance and environmental goals, providing long-term value and competitive advantage.
Future of Powder Metallurgy in Green Manufacturing
As industries continue to seek greener alternatives, powder metallurgy is expected to play a pivotal role in next-generation manufacturing. Several trends highlight its growing relevance:
- Green Mobility – The electric vehicle (EV) market is booming, and PM offers lightweight, durable components for motors and batteries.
- Eco-Friendly Packaging – PM allows for the creation of biodegradable or recyclable materials used in specialized packaging.
- Smart Materials – Integration with nanotechnology and smart sensors is leading to intelligent PM-based products.
- Decentralized Production – With 3D printing, localized production becomes feasible, reducing the need for global shipping and its associated emissions.
These advancements align PM with the principles of Industry 4.0 and sustainable development.
Conclusion
Powder metallurgy is more than just an alternative manufacturing method—it’s a forward-thinking approach that combines efficiency, precision, and sustainability. Its ability to minimize waste, reduce energy consumption, and produce high-performance components with complex geometries makes it a standout choice in eco-conscious industries.
Whether you’re an engineer, manufacturer, or decision-maker in a company seeking sustainable solutions, powder metallurgy offers a compelling case. From the raw material to the final product, the entire process supports a greener, more responsible manufacturing future.
As demand for low-impact production grows, partnering with an experienced powder metallurgy supplier and embracing the powder metallurgy process could be your next step toward environmental and economic success.
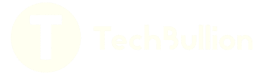