Introduction
Plastic molding solutions play a crucial role in modern manufacturing, offering cost-effective, scalable, and versatile methods to produce a wide variety of components used across industries. From everyday consumer products to intricate parts for aerospace and medical applications, plastic molding technologies deliver precision, repeatability, and high efficiency.
This article provides an in-depth overview of Plastic Molding Solutions, covering the main types, materials used, benefits, industry applications, and innovations driving the future of plastic manufacturing.
What Are Plastic Molding Solutions?
Plastic molding refers to a manufacturing process in which plastic material is heated, shaped in a mold, and cooled to form a solid part. Molding enables the mass production of complex plastic components with consistent accuracy and minimal waste.
These solutions vary depending on the material, complexity, production volume, and intended application. Choosing the right molding method is crucial for achieving cost-efficiency, functionality, and aesthetic appeal.
Major Types of Plastic Molding
There are several plastic molding processes, each with unique advantages and suitable use cases:
1. Injection Molding
- Process: Molten plastic is injected into a metal mold under high pressure.
- Applications: Automotive parts, electronics casings, household goods.
- Advantages: High production speed, consistent quality, supports complex geometries.
2. Blow Molding
- Process: Heated plastic is inflated inside a mold to form hollow objects.
- Applications: Bottles, containers, fuel tanks.
- Advantages: Ideal for high-volume production of hollow items.
3. Rotational Molding (Rotomolding)
- Process: Plastic powder is placed in a mold, which is heated and rotated on multiple axes.
- Applications: Large tanks, kayaks, playground equipment.
- Advantages: Uniform wall thickness, low tooling cost, good for large parts.
4. Thermoforming
- Process: A plastic sheet is heated and formed over a mold using vacuum or pressure.
- Applications: Packaging, trays, automotive panels.
- Advantages: Fast and cost-effective for low-to-medium volumes.
5. Compression Molding
- Process: Plastic material is placed in a heated mold cavity and compressed into shape.
- Applications: Electrical components, automotive parts, industrial seals.
- Advantages: Good for high-strength parts, especially thermosets.
6. Extrusion Molding
- Process: Plastic is melted and forced through a die to create continuous shapes.
- Applications: Pipes, tubing, window frames.
- Advantages: Excellent for long, uniform cross-section products.
Common Plastic Materials Used
Plastic molding can accommodate a wide array of thermoplastics and thermosetting polymers. Popular materials include:
- Polyethylene (PE) – Flexible and chemical-resistant; used in containers and packaging.
- Polypropylene (PP) – Lightweight and fatigue-resistant; ideal for automotive and household goods.
- Acrylonitrile Butadiene Styrene (ABS) – Tough and impact-resistant; used in electronics and toys.
- Polyvinyl Chloride (PVC) – Durable and weather-resistant; used in piping and construction.
- Polystyrene (PS) – Lightweight and easy to mold; used in packaging and disposable items.
- Nylon (PA) – High strength and wear resistance; used in industrial and mechanical parts.
- Polycarbonate (PC) – Transparent and tough; used in lenses, safety gear, and electronics.
The choice of material affects durability, flexibility, clarity, cost, and heat resistance—making material selection vital for successful product development.
Key Applications Across Industries
Plastic molding is integral to countless industries, providing reliable solutions for a wide range of functional and aesthetic requirements:
1. Automotive
- Dashboard components, interior trims, bumpers, and fluid reservoirs.
- Molding enables lightweight parts that enhance fuel efficiency.
2. Consumer Goods
- Toys, kitchenware, packaging, storage containers.
- Molding offers customization, color variety, and scalability.
3. Medical
- Syringes, IV components, surgical instruments, casings for medical devices.
- Precision molding ensures sterility, safety, and biocompatibility.
4. Electronics
- Casings, switches, connectors, cable insulation.
- Injection molding supports miniaturization and durability.
5. Packaging
- Bottles, caps, trays, clamshells, and blister packs.
- Blow and thermoforming methods offer rapid and economical solutions.
6. Construction
- Piping, insulation, panels, window frames.
- Plastic molding ensures weather resistance and cost savings.
Advantages of Plastic Molding Solutions
Plastic molding delivers significant benefits over other manufacturing methods:
1. Cost-Efficiency
- Once the mold is made, each unit is inexpensive to produce—ideal for high-volume manufacturing.
2. Design Flexibility
- Molds can be custom-made for complex shapes, intricate details, and integrated features.
3. Repeatability
- Consistent production with tight tolerances ensures uniformity across thousands or millions of parts.
4. Material Versatility
- Supports a broad spectrum of plastic materials with diverse mechanical and thermal properties.
5. Faster Production
- Automated and high-speed molding machines reduce turnaround time.
6. Minimal Waste
- Advanced molding techniques optimize material use and reduce environmental impact.
Challenges in Plastic Molding
Despite its advantages, plastic molding presents some challenges that require careful planning and execution:
- High Initial Tooling Costs: Designing and machining molds can be expensive, especially for complex parts.
- Material Limitations: Some plastics may not perform well under extreme heat or load.
- Environmental Concerns: Use of non-biodegradable plastics raises sustainability issues.
- Defects: Issues like warping, sink marks, and voids may arise if process parameters are not tightly controlled.
Partnering with experienced plastic molding manufacturers ensures quality control and defect mitigation throughout the production cycle.
Innovations and Trends in Plastic Molding
Plastic molding technologies are rapidly evolving, bringing smarter, greener, and more efficient solutions:
1. 3D-Printed Molds
Additive manufacturing allows for rapid prototyping of molds, reducing lead times and costs for small production runs.
2. Biodegradable Plastics
There is growing adoption of plant-based and compostable materials in response to environmental concerns.
3. Automated Quality Control
Vision systems and sensors embedded in molding machines help detect defects in real time and maintain consistency.
4. Micro-Molding
Miniature precision molding is used in medical and electronics industries to produce extremely small, intricate parts.
5. Hybrid Manufacturing
Combining molding with CNC JSRPM Precision Machining or 3D printing opens new possibilities for advanced product designs.
6. Sustainable Molding Practices
Closed-loop systems for material recycling and energy-efficient machines help reduce the industry’s carbon footprint.
Choosing the Right Plastic Molding Partner
Selecting a trusted plastic molding provider is crucial to the success of any product. Key factors to consider include:
- Experience and Expertise: Proven track record in your industry.
- In-House Capabilities: Design, tooling, prototyping, and post-processing.
- Material Knowledge: Guidance on selecting the right plastic for your application.
- Certifications: ISO, FDA, and other quality standards.
- Customer Support: Transparent communication, flexibility, and on-time delivery.
The right partner helps turn your ideas into reality—efficiently, affordably, and reliably.
Conclusion
Plastic molding solutions have transformed the way products are designed, manufactured, and brought to market. With a wide range of processes and materials available, companies can produce everything from simple packaging to mission-critical components with precision and speed.
As innovations continue to emerge in automation, sustainability, and material science, plastic molding will remain a backbone of global manufacturing—shaping the future one part at a time.
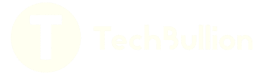