The precise cutting and shaping of industrial sheets of metal is one of the foundational practices in the manufacturing of high-quality complex products utilized in automobiles, aircraft, electronics, constructions, and many others. The process starts with designing and prototyping then moves to final assembly and subsequently product delivery. This piece discusses the process of sheet metal fabrication and assembly, specifically detailing the actions taken towards turning an idea into a working product. Most B2B firms should comprehend this information as it tends to their cost, product value, and manufacturing processes. Accuracy and dependability can be guaranteed at each step of production when proper partners are employed, portraying ideal collaboration. Accurate vehicle metal fabrication guarantees solid structural and economical design considerations which beneficially serves the manufacturers and consumers from value perspective for a very long time.
Understanding Bespoke Metal Fabrication in Vehicle Design
Bespoke metal fabrication is the process of creating custom metal parts for a specific design. Unlike off-the-shelf components, bespoke metal fabrication offers the ability to create custom parts that are specially designed for a specific vehicle or project. This process entails shearing, bending, welding, and finishing sheets of metal into more complex patterns, with exact measurements down to the micron. It is this degree of customization that enables manufacturers to produce vehicle components with unmatched distinctions in quality.
In contemporary automobiles, bespoke metal fabrication is employed to produce precisely tailored structural components, body panels, and other specialized elements. The ability to manufacture these bespoke components allows vehicle builders to adhere to stringent quality benchmarks while fulfilling the design’s functional and visual intent. With bespoke metal fabrication, designers unleash true innovation; it allows achieving the desired contours, thicknesses, and features which would otherwise not be feasible with pre-set mass production molds. This provides an unmatched advantage in fulfilling the design team’s specific criteria while achieving outstanding operational capabilities.
How Industrial Sheet Metal Fabrication Enhances Vehicle Performance
The fabrication of sheet metal for industrial purposes has an undeniable impact on the performance of vehicles. The process makes it possible to manufacture parts that are both lightweight and strong, which makes the vehicle more efficient. Vehicle manufacturers can design parts using high-strength metals and sophisticated fabrication methods which improve the aerodynamics, reduce the weight, and sustain the structural integrity of the vehicle. Reduction of mass in the components improves the fuel economy and handling of the vehicle which is vital for daily driving cars and high-end sports cars alike.
As an example, bespoke metal fabrication allows for body panels to be custom designed face-lifted for the specific make and model of the automobile, giving ease when it comes to appealing aesthetics . In consideration of the need for fuel economy and lower emissions, the automotive industry relies on bespoke industrial sheet metal fabrication to design the components because of the precision and speed with which it works. Tailored made vehicle parts guarantee an optimal performance and precision throttle durability with extreme conditions and climate. Also, the tailored description enables the designers to retain a seamless appearance while optimizing the performance of the components across the vehicle’s systems, aiding in modern vehicle construction.
The Role of Industrial Sheet Metal Fabrication in Safety Features
Due to industrial sheet metal fabrication, safety elements in vehicles are improved. Vehicle metal works are vital to guarantee that the structural parts can withstand impacts, guard, and allow protective elements to be civil within the vehicle’s safety regulations internationally. Precision sheet metal fabrication makes it possible for a vehicle’s parts to be optimally manufactured to safeguard the vehicle and its passengers.
Bespoke metal fabrication is used to make reinforced frames, crumple zones, and other essential protective structural elements. These structures help to safeguard passengers by bearing some of the impact forces during a collision. The strength and weight of these features can be increased simultaneously using industrial sheet metal fabrication with no compromise on the vehicle’s performance. Also, bespoke fabrication aids adaptation for modern safety features such as ADAS sensor mounts, thus adding convenience and protection while aligning the vehicle with contemporary safety standards.
Environmental Considerations in Bespoke Metal Fabrication for Vehicle Design
The use of sustainability and environmental considerations are now included in the latest vehicle models. Through custom metal fabrication and industrial sheet metal fabrication, eco-friendly cars can be manufactured. Waste reduction during the manufacturing process, as well as using lighter metals, can improve the carbon footprint of production. While the automotive industry has always been a source of concern for the environment, the shift towards the adoption of electric vehicles (EVs) has transformed the industry into a cleaner one – allowing for the development of eco-friendly cars.
The use of bespoke fabrication also facilitates better sustainability practices by allowing for the integration of recycled materials to vehicle components. Eco-friendly vehicles (EVs) and hybrid models are becoming more common, and this trend highlights the importance of metal fabrication in designing environmentally-friendly vehicle parts. For example, minimizing the design of sheet metal parts maximizes their use resulting in lighter vehicle weight which improves the driving range and efficiency of electric vehicles. Indeed, we are moving towards a greener future with reduced carbon footprints from the automotive industry. Additionally, enhancing the design of processes and materials leads to higher energy efficiency, improved operational efficiencies, less environmental impact, and reduced production costs.
Conclusion
Every contemporary automotive vehicle incorporates elements of custom metal fabrication as well as industrial sheet metal fabrication. These processes enable the sophisticated custom vehicle parts like safety features which modern vehicles possess to be manufactured. The cutting edge industrial sheet metal fabrication does not only participate in vehicle design but also assists in performance optimization, reliability, safety, and environmentally friendly manufacturing practices.
For business-to-business companies, collaborating with reputable suppliers for bespoke vehicles will guarantee that you obtain precision bespoke parts. There are constant demands for new automotive solutions, and reputable metal fabrication firms will always be needed to realize those innovations automotive manufacturers need to keep up with market demands. It’s clear now, from electric vehicles to combustion engines, that bespoke metal fabrication will be essential to the future of the automotive industry.
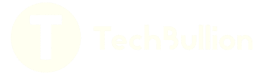