Introduction
Printed Circuit Boards (PCBs) form the backbone of modern electronic devices, providing both structural support and electrical connectivity for components. The choice of PCB substrate material is critical especially in advanced applications where signal integrity, thermal performance, and reliability are paramount.
As electronic devices grow smaller, faster, and more powerful, PCB materials must meet increasingly stringent demands. At Hongrong (Shenzhen) Electronics with over 20 years of experience in the PCBA industry, we understand how essential it is to choose the right materials to optimize both performance and cost.
Common PCB Materials and Their Properties
- FR-4 (Flame Retardant 4)
Widely used across the industry, FR-4 is a glass-reinforced epoxy laminate known for its affordability and balanced mechanical and electrical characteristics. However, its higher dielectric constant (Dk) and dissipation factor (Df) limit its effectiveness in high-frequency applications. - PTFE (Teflon)
PTFE-based laminates are ideal for radio frequency (RF) and microwave systems. Their low Dk and Df provide excellent signal integrity but come at a higher cost and require more sophisticated manufacturing processes. - Ceramic-Filled Composites
These advanced materials offer excellent thermal conductivity and signal stability, making them suitable for high-power applications. However, due to higher material and processing costs, they are primarily used in specialized sectors such as aerospace and defense. - High-Speed Laminates (e.g., Rogers, Isola)
Brands like Rogers and Isola provide low-loss laminates specifically engineered for high-speed digital and RF applications. These materials ensure better impedance control and minimal signal loss, making them ideal for data centers, telecom, and aerospace systems.
Key Performance Trade-Offs
Choosing the right PCB material involves balancing performance needs with practical constraints. Below are some of the most common trade-offs:
- Signal Integrity vs. Cost
High-speed designs require materials with low Dk and Df to minimize signal degradation. While premium materials like PTFE offer excellent performance, they increase overall production costs.
Trade-off: FR-4 is economical but may not maintain signal integrity at high frequencies. - Thermal Management vs. Manufacturing Complexity
Effective heat dissipation is vital for power electronics. Materials with higher thermal conductivity, such as ceramic-filled substrates, support thermal efficiency but pose greater manufacturing challenges.
Trade-off: Advanced thermal performance often requires more complex processing. - Mechanical Stability vs. Flexibility
Rigid laminates offer dimensional stability and support for high-density components. Flexible materials, such as polyimide, are essential for dynamic or compact form factors like wearables.
Trade-off: Mechanical strength must be weighed against design flexibility. - Dielectric Constant vs. Miniaturization
A lower Dk enables faster signal transmission and tighter design tolerances. However, such materials typically come at a premium price.
Trade-off: Higher performance in compact devices requires investment in more advanced materials.
Design Considerations for Advanced Applications
When designing advanced electronics, material selection must be aligned with the application’s technical and environmental demands. Key factors include:
- Operating Frequency – Higher frequencies necessitate low-loss materials.
- Thermal Environment – High-power designs require effective heat dissipation.
- Mechanical Requirements – Consider rigidity, flexibility, and mechanical endurance.
- Manufacturability – Materials should be compatible with existing assembly processes.
At Hongrong, we offer end-to-end PCBA services with expert engineering support to guide material selection based on your product requirements and manufacturing goals.
Future Trends in PCB Materials
The PCB industry is evolving rapidly. Emerging materials such as Liquid Crystal Polymers (LCPs) and ultra-low-loss laminates are becoming critical for 5G infrastructure, autonomous systems, and next-generation IoT devices. These materials promise exceptional electrical performance and long-term reliability—but their adoption is currently limited by high costs and supply constraints.
By staying at the forefront of industry developments and leveraging our mature customer support and ISO-certified quality systems, Hongrong is ready to help you integrate cutting-edge materials into your designs.
Conclusion
Selecting the right PCB material is a strategic decision that significantly impacts the performance, reliability, and cost of an electronic product. In a landscape driven by miniaturization, speed, and thermal demands, there is no universal solution—only carefully considered trade-offs.
With two decades of experience, a professional engineering and sales team, and a commitment to quality and service, Hongrong (shenzhen) Electronics Co., Ltd. is your trusted partner in delivering high-performance PCBA solutions tailored to your needs.
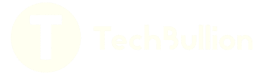