Waiting for important machinery to fail before fixing it is a fast way to tank your profits. When a machine goes down unexpectedly, operations come to a halt, productivity stops, and costly emergency repairs are needed to return to normal. Whether you’re down for a few hours, days, or weeks, the loss of revenue can be devastating. Some customers won’t wait for you to return before heading to your competitors, and if the disruption lasts too long, your reputation may suffer.
Preventive maintenance is the best approach to avoid expensive, unexpected breakdowns. Instead of fixing what’s broken, a maintenance strategy continuously maintains all assets to keep them running smoothly and catches small issues before they grow.
By implementing a well-structured maintenance schedule, you can increase equipment lifespans, reduce unexpected downtime, and optimize operational efficiency. If you don’t currently have a plan, here’s a good way to get started.
- Implement a backup system
Backup systems are the foundation of a good preventive maintenance plan. Nothing prevents a crisis like being fully prepared. Ideally, you’ll need a backup system or plan for every piece of equipment central to your daily operations. For example, if you own your electrical transformer, unplanned downtime due to failure will cause the electricity to go out. However, a backup transformer or a backup power source will minimize the disruption.
Common transformer backup systems include:
- Redundant systems. Having a parallel transformer will give you the best protection by immediately transferring the load if your main unit fails.
- Onsite backup transformers. Many organizations keep a spare transformer onsite or in a nearby storage location.
- Planned replacements. Proactively replacing an aging transformer will help prevent failure.
- Emergency response plan. If you can’t implement a backup system, an emergency response plan is critical. Your plan should include knowing who to call to get a replacement unit fast.
Regardless of the equipment, backup systems and plans should be reviewed periodically, assessed for practicality, and adjusted as needed.
- Read your equipment manuals
Few people read manufacturer’s manuals, but this is crucial for implementing an effective maintenance strategy. You need to know what the manufacturer recommends for ideal service intervals and how to maintain the equipment.
Sometimes intuitive actions aren’t appropriate for certain machinery, and the manufacturer’s manual will explain these things. For example, if you use the wrong cleaning substance or do something the manual says to avoid, it can damage the equipment and will likely void your warranty.
- Inventory your equipment
A solid preventive maintenance schedule begins with an inventory of all equipment to be cycled through the program. List every machine, tool, and asset that requires regular maintenance. Include the make, model, usage frequency, and how critical it is to operations. Make a note to prioritize maintenance for equipment that would cause significant disruptions if it failed.
- Define maintenance tasks
For each piece of equipment, document what maintenance tasks need to be done. You can get this information from manuals and manufacturer websites. If you can’t find the information, call the manufacturer directly.
Once you know what the manufacturer recommends, customize the tasks based on industry best practices and your usage.
- Determine maintenance intervals
Once you have a list of maintenance that needs to be performed, you’ll want to break it down into intervals. These intervals will be based on time, usage, or condition. For instance, some equipment will need weekly or monthly maintenance tasks, while other equipment gets maintained based on usage, like hours run or cycles completed. You might even have some machinery that only requires maintenance under certain conditions detected by sensors.
- Assign responsibilities
Defining clear roles will prevent maintenance tasks from falling through the cracks and will establish accountability. Assign specific individuals or teams to every maintenance task, and define their roles and expectations. Be specific about who is responsible for task execution and reporting.
- Train your maintenance teams
Around 70% of employees reported not having the skills to do their jobs. In many cases, employers pass maintenance responsibilities to untrained employees just to check the task off their list. This will end in disaster.
If your regular employees aren’t trained to perform maintenance, either train them fully or source a dedicated maintenance team. Whoever is in charge of performing maintenance needs to be trained to spot red flags and implement first-line fixes. Maintenance isn’t just about being able to follow instructions to perform a few tasks. It requires a holistic understanding of the equipment that provides the awareness required to troubleshoot effectively.
- Schedule your maintenance tasks on a calendar
A visual schedule makes planning and tracking manageable. Use automated scheduling tools so your teams can see what’s coming ahead of time and implement alerts so everyone gets their assigned tasks done on time. Sync this to everyone’s work calendar and ensure your employees turn on notifications.
- Create written documentation
Your current maintenance team might be amazing, but when an employee with extensive knowledge quits, that information leaves with them. Over time, your maintenance employees will get to know your equipment in ways that make it easier for them to do their jobs, and new hires won’t have that advantage. When you need to hire someone new, they’ll benefit from what the rest of the team knows. Having thorough written documentation will help.
Your documentation should include a condensed collection of manufacturer recommendations, a past history of all problems, maintenance, and repairs for each piece of equipment, and any relevant notes that will support future maintenance.
- Include visual inspections
An important part of preventive maintenance involves visual inspections. Not every inspection needs a wrench. Sometimes it’s about catching leaks, rust, vibrations, or strange noises.
- Keep a maintenance log
In most industries, keeping a maintenance log is a legal requirement. Regardless, maintaining a log of all tasks performed will help you spot patterns and prove compliance if you’re ever audited.
Proactive maintenance pays off
Implementing a preventive maintenance schedule will give you a strategic advantage in your industry. By prioritizing maintenance, you can avoid costly downtime, extend the life of your equipment, and maintain efficient and reliable operations.
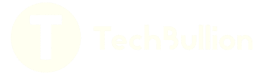