If you manage or work in a warehouse, you’ve likely experienced the frustration that comes with congestion: cluttered aisles, delayed shipments, and staff constantly trying to navigate around one another. It’s not just a nuisance; it’s a serious problem that can affect productivity and increase operating costs. More than that, it can even put people’s safety at risk.
Warehouse congestion tends to happen when too many goods, people, or vehicles are trying to occupy the same space at once. This issue can stem from problems like poor layout design and inefficient workflows. It can also be because of lack of planning during peak periods.
The good news is that it can be resolved. With the right strategies in place, you can manage and reduce congestion while improving your company’s overall efficiency. Let’s look at some practical tips that can help you take control of the space and operations in your warehouse:
1) Optimise Your Warehouse Layout
An optimised layout is one where movement—of both people and goods—is smooth and logical. Does your facility employ an optimised layout? To find the answer, start by looking at the physical layout of your warehouse.
Are your aisles wide enough for equipment to pass through safely? Are your high-frequency items stored in easily accessible spots? If you answered yes to both questions, that’s a good start. Another area to consider is bottlenecks. Avoid them by clearly marking walkways and setting up dedicated zones for loading, unloading, picking, and packing.
Don’t forget to make full use of your vertical space. Installing higher racking systems allows you to store more goods without expanding your footprint. This frees up floor space and reduces clutter at ground level.
2) Assign and Train Staff Strategically
When everyone is running around without clear roles or zones, congestion becomes inevitable. To avoid this, make it a point to assign staff to specific areas or shifts. Doing so can help balance workloads and reduce traffic in key parts of the warehouse.
Proper training is also key. When employees know how to handle equipment and follow routes, their place of work can run more smoothly. If you use equipment like an electric stacker, make sure that your team members can operate it properly. This way, you’ll be able to maximise the machine’s capability to speed up material handling in tight spaces while promoting safety.
3) Make Use of Slotting Strategies
Slotting is all about placing items in the right location based on how often they’re picked. Fast-moving items should be positioned close to packing areas or at waist height for easier access, while slow-moving or seasonal stock can be stored further away. This reduces unnecessary foot traffic and prevents congestion in high-activity zones.
Aside from adopting this tried-and-tested slotting strategy, be sure to review your slotting plan so you can adapt to changing demand and keep your operation flowing efficiently.
4) Stagger Inbound and Outbound Deliveries
Too many deliveries or collections happening at the same time can bring your warehouse to a standstill. As much as possible, stagger your inbound and outbound schedules so that loading docks aren’t overwhelmed and staff aren’t dealing with multiple shipments all at once. A simple delivery appointment system can make a big difference in keeping vehicle movements and receiving activities organised.
5) Use a Warehouse Management System (WMS)
A WMS will help you keep track of your inventory in real time. It has many functionalities, which can include guiding pickers along the most efficient paths, alerting you to overstocking issues, and helping you plan restocking or deliveries more accurately. With better visibility and control over your operations, you’ll be able to reduce unnecessary movement and prevent items from piling up in the wrong areas.
If your system integrates with other business tools, like sales or procurement software, you’ll be able to make even smarter decisions across the supply chain.
6) Regularly Audit Your Inventory
Sometimes, congestion comes down to simple overstocking. Holding on to excess, outdated, or damaged inventory takes up valuable space and makes your warehouse harder to navigate. Control this issue by holding regular stock audits that can help you identify what’s not moving and clear it out. Implementing leaner inventory practices, like just-in-time stocking, combined with advanced technologies such as AS/RS Systems, can also prevent build-up and keep your storage space focused on what’s actually in demand.
7) Consider Cross-Docking Where Applicable
Cross-docking, which is the practice of directly transferring goods from inbound delivery to outbound dispatch, lets you effectively bypass long-term storage. Adopting this strategy can dramatically reduce the number of items clogging up your warehouse and speed up order fulfilment.
Keep in mind, though, that not every operation is suited for cross-docking. This strategy is most effective if you handle large volumes of predictable, fast-moving goods.
8) Invest in the Right Material Handling Equipment
Besides electric stackers, having a range of material handling equipment such as pallet jacks, forklifts, conveyors, or even automated guided vehicles (AGVs) can greatly improve the speed and safety of your operations. The right tools allow your team to move heavy or bulky items more efficiently, freeing up floor space and reducing potential traffic jams. Just ensure that each piece of equipment is properly maintained and suitable for the size and layout of your warehouse.
9) Set Up Temporary or Off-Site Storage
If you’re dealing with seasonal peaks or special projects that bring in extra stock, consider setting up temporary storage units or using off-site facilities. Keeping overflow inventory off the main floor ensures that your day-to-day operations remain smooth and congestion-free. Portable storage containers or rented warehouse space can be particularly cost-effective ways to manage short-term volume spikes without compromising your workflow.
10) Improve Communication Across Teams
Finally, clear and consistent communication across teams goes a long way in preventing congestion. Whether it’s through regular briefings, radio systems, or warehouse dashboards, keeping everyone informed will help your organisation avoid surprises and delays. When your teams understand what’s coming in, what’s going out, and what needs to happen next, they can work together more effectively to prevent build-ups and solve problems quickly.
All in all, reducing warehouse congestion isn’t just about clearing space, but more about creating a more efficient, safer, and productive environment for your team. Take a thoughtful approach to layout, staffing, equipment, and planning, and you’ll be able to transform your facility into a well-oiled machine. As you’ll quickly discover, a well-organised warehouse is not only easier to manage—it’s more profitable, too.
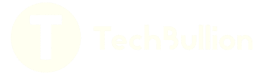