In many industrial processes, maintaining consistent temperatures in pipes, tanks, and equipment is crucial. Whether it’s to prevent liquids from freezing or to optimize system efficiency, temperature control is a key element of operational reliability. One widely used technique to achieve this is heat tracing — a dependable solution for industries dealing with temperature-sensitive processes.
What is heat tracing?
Heat tracing is a method that involves installing heating cables along pipes, tanks, or other equipment to maintain a desired temperature. This helps prevent contents from freezing or ensures that materials remain at the optimal temperature for processing. Industries such as
oil and gas, chemicals, and food processing often rely on heat tracing systems to keep operations running smoothly, particularly in environments subject to fluctuating or extreme temperatures.
The importance of mineral insulated heat trace
One of the most trusted and efficient forms of heat tracing is mineral insulated heat trace. This technology consists of a robust cable built with a metal sheath, insulating powder, and an internal conductor — enabling high-performance heat transfer. MI heat trace systems are especially suitable for demanding environments, such as offshore platforms, chemical plants, and marine installations, where durability and temperature precision are essential.
Benefits of mineral insulated heat trace
There are several advantages to using mineral insulated heat trace in industrial applications: ● Exceptional reliability in extreme hot or cold conditions
- High resistance to corrosion, contributing to long service life
- Efficient heat transfer, reducing energy consumption
- Certified for hazardous environments, making it ideal for use in areas with explosion risk, such as oil and gas facilities
- Tolerance to high temperatures, allowing use in a wide range of industrial systems
Thanks to these benefits, mineral insulated heat trace has become a preferred choice for companies that need consistent and safe heating solutions across critical infrastructure.
Industrial applications of heat tracing
Heat tracing is used across a broad range of industrial applications. It plays a vital role in protecting pipelines carrying chemicals or oils from freezing, which could otherwise lead to blockages or unsafe reactions. It’s also used in steam or water-based systems, where maintaining a stable temperature is essential to ensure the efficiency and integrity of production processes.
Business benefits of heat tracing
Implementing heat tracing offers significant value to businesses. By maintaining reliable temperature control, companies can increase process efficiency, reduce the risk of production downtime, and minimize waste caused by temperature deviations. Additionally, the high thermal efficiency of these systems contributes to energy savings, supporting both operational performance and sustainability goals.
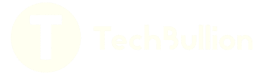