Accurate and reliable measurements are essential in any industry that relies on material testing. Whether used in research laboratories, quality control departments, or manufacturing facilities, testing equipment must consistently deliver the correct results. For this to happen, regular calibration is necessary.
Calibration is the process of comparing a device’s output against a known standard to detect and correct discrepancies. Over time, even the most advanced testing tools can experience minor accuracy shifts due to environmental conditions, regular use, or mechanical wear. These shifts, if left uncorrected, may lead to invalid data, failed quality checks, and non-compliance with international testing standards.
Industries that rely on material testing equipment, such as tensile testers, hardness testers, and CNC machines for specimen preparation, depend on precise performance to make informed decisions. Regular calibration supports that precision. This article explores the role of calibration in achieving measurement accuracy, the potential risks of improper calibration, and the best practices for keeping your equipment in optimal condition.
The Role of Calibration in Measurement Accuracy
Calibration is a controlled and documented process that ensures a testing device is producing measurements within an acceptable range of error, as defined by national or international standards. It serves as a reference point to confirm that each instrument operates correctly and consistently. In the field of material testing, where exact values are necessary for determining properties such as strength, durability, or resistance, calibration is integral to guaranteeing valid results.
For instance, a universal testing machine used to measure tensile strength must apply the load accurately. Even a small deviation in force measurement can lead to incorrect conclusions about material performance. Similarly, devices used for hardness testing or abrasion resistance must apply the correct pressure and follow a defined measurement path. If the equipment is not calibrated, the results may show materials as compliant or non-compliant without a basis.
Many industry standards, including ISO/IEC 17025, ISO 7500-1, and ASTM E4, require regular testing and machine calibration. These standards help laboratories and manufacturers meet international measurement accuracy expectations. Without calibration, an organization risks using equipment that does not meet these standards, which can compromise test results.
Moreover, traceability is a core requirement for calibration. It means that the equipment being calibrated must be compared against reference standards calibrated to national or international measurement benchmarks. It provides accountability and increases the accuracy of the measurement data by establishing a chain of accountability.
In modern laboratories and production environments, the testing tools like CNC machines, optical systems, and sensor-based devices must also be recalibrated periodically. These machines are often used to prepare samples or conduct automated tests. Their reliability depends not only on proper operation but also on precise alignment and control confirmed through calibration.
Ultimately, regular calibration safeguards measurements’ accuracy, repeatability, and traceability. It allows businesses and laboratories to make informed decisions, comply with standards, and uphold quality.
Risks of Infrequent or Improper Calibration
When testing equipment is not calibrated regularly, the consequences can be significant. Even a slight deviation from accurate measurements can result in incorrect data, leading to quality failures, safety risks, or loss of customer trust. In environments where precision is essential—misleading results caused by poor calibration can lead to serious operational and financial consequences.
One of the main risks is failure to detect defects or non-compliance with materials. For example, if a tensile testing machine is out of calibration, it may display a material as stronger or weaker than it is. This could result in using unsafe materials in production or rejecting acceptable materials. The same applies to hardness testers, impact testing tools, and abrasion testing machines. Any error in the applied force or measurement output compromises test validity.
Another concern is the impact on audits and certifications. Many industries operate under strict regulatory frameworks that require proper equipment maintenance and calibration. If a company cannot provide calibration records or is found to use improperly calibrated devices, it may lose its certification or face legal penalties. This can damage the organization’s credibility and affect its market position.
Operational efficiency also suffers when machines give inconsistent or unreliable results. Teams may waste time rechecking samples or performing additional tests to verify suspicious results. This delays the process, but also increases costs. In some cases, improperly calibrated material testing equipment may require unexpected repairs, further increasing downtime and expenses.
In advanced systems, such as CNC machines used for tensile specimen preparation, calibration also includes alignment and positioning accuracy. These machines cut or shape test samples to precise dimensions. If their calibration is off, the prepared samples may not meet standard requirements such as those outlined in ASTM or ISO guidelines, making the entire testing process invalid.
Best Practices for Regular Calibration
To maintain testing equipment accuracy and reliability, laboratories and manufacturers must adopt a consistent and documented calibration process. Calibration frequency depends on several factors, including how often the equipment is used, the critical nature of its application, and the manufacturer’s recommendations. As a general rule, high-precision devices used for daily testing should be calibrated more frequently than those used occasionally.
A formal calibration schedule should be established as part of the organization’s quality management system. This schedule must include past calibration dates, upcoming due dates, and the specific instruments involved. Documenting this information helps you prepare for internal audits, external inspections, and recertification processes.
Whenever possible, calibration should be performed by accredited third-party service providers or in-house technicians using traceable reference standards. These standards must conform to national or international measurement systems. This traceability ensures that every test result can be linked back to a known standard, reinforcing confidence in the data.
CNC machines used for specimen preparation should be calibrated, including checking the positioning system, tool alignment, and software accuracy. Some modern CNC systems are equipped with automatic calibration features that alert the operator when performance shifts outside acceptable limits. This technology helps reduce manual oversight and supports a more reliable testing environment.
Other testing tools, such as extensometers, pressure sensors, and load cells, also require periodic calibration. Each component must function within its designed parameters to maintain overall system accuracy. Failing to calibrate just one part can affect the entire measurement process.
Digital tools should also be reviewed for software updates affecting measurement algorithms or calibration routines. Calibration certificates should be securely stored and readily available when requested. This documentation supports regulatory compliance and helps organizations track long-term performance trends.
Securing Long-Term Accuracy and Compliance
Regular calibration is not simply a maintenance task—it is a foundational requirement for reliable testing. Without consistent calibration, even the most advanced material testing equipment and CNC machines can produce inaccurate data, putting product quality, safety, and compliance at risk.
By adopting structured calibration routines, supported by traceable reference standards and accurate documentation, laboratories and manufacturers can ensure their testing tools deliver precise and consistent results. This builds trust in the data, supports certification efforts, and helps organizations meet industry regulations with confidence.
Moreover, as technology advances, the integration of automated calibration features into modern systems allows for improved efficiency and reduced error risk. From tensile testers to digital hardness testers and CNC specimen preparation systems, calibrated equipment is essential for maintaining high standards in research, development, and production environments.
As a conclusion, regular calibration is a small investment that yields long-term returns in measurement accuracy, regulatory compliance, and operational reliability. Organizations that prioritize it demonstrate a commitment to quality and position themselves for success in a data-driven, standards-focused industry landscape.
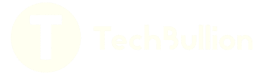