In 2025, the automotive manufacturing sector continues to seek innovative ways to optimize costs and efficiency, particularly in the face of rising production demands and competitive pressures. Mold transfer services are revolutionizing how automotive manufacturers cut costs, speed up production, and maintain top notch quality.
I’ve spent two decades in automotive manufacturing, watching it transform firsthand. The shift toward mold repurposing isn’t just about pinching pennies, it reflects a deeper industry evolution toward utilizing smarter resources and flexibility in the operations. Let me share what I’ve learned from working with dozens of major automotive brands.
Why Mold Transfer Services Are A Big Deal
Mold transfer services let manufacturers repurpose existing molds instead of shelling out for new ones. In the automotive world, molds shape everything from engine blocks to dashboard trims. These aren’t lightweight tools—they can weigh 100 tons and demand pinpoint accuracy. Building a new mold? That’s weeks of design, machining, and testing, not to mention costs that can hit $40,000 to $50,000 a pop. Transferring an existing mold, though, might run you $5,000 to $10,000, depending on the tweaks needed.
Why does this matter? Because every dollar saved is a dollar you can pour into R&D, equipment upgrades, or beating the competition on price. Plus, it’s not just about the upfront cost. Reusing molds cuts down on material waste and energy use, which aligns with the industry’s push toward sustainability.
The Financial Upside of Mold Repurposing
The numbers tell a compelling story. New automotive molds frequently command price tags north of $50,000 and sometimes much higher for complex components. The material costs alone can be staggering, not to mention the specialized labor and machine time required to produce them.
I worked with a parts supplier last year who needed to update a dashboard component for a luxury vehicle line. Their options were stark and needed to commission a new mold or modify an existing one. The new mold quote came in at $43,500. Our transfer and modification approach was just $7,800. The savings were transformative for their quarterly budget, allowing investment in quality control equipment they had been postponing for years.
This becomes even more importan when you multiply the many molds needed in automotive production. One manufacturer I consulted with saved over $1.2 million in a single year by implementing a comprehensive mold transfer program rather than defaulting to new molds.
Beyond the direct savings, there’s the sustainability. Every repurposed mold means less raw material consumed, reduced energy expended in machining, and fewer transportation emissions. In an industry increasingly measured by its carbon footprint, these benefits matter.
Less Downtime, More Output Keeps the Line Moving
Downtime is the silent killer in automotive manufacturing. Every minute your production line sits idle, you’re bleeding money. Traditional mold changes can take hours and sometimes days. You’ve got forklifts, cranes, and a team of operators wrestling with a 50-ton mold. It’s a logistical nightmare. Professional mold transfer services, paired with specialized equipment like mold transfer carts, turn that headache into a breeze.
Let’s say a plant producing engine components for commercial trucks.needs to switch between different engine block designs weekly. The old school mold changes took 8 hours, stalling the line and delaying shipments. By using automated mold transfer carts, they were able to cut that to two hours. That’s an extra shift’s worth of production each week.
Real world examples back this up. At Faurecia, they use a mold change system, which shuttles molds from a large storage facility to the injection molding machine in minutes. Automated centering and clamping make it seamless. Other companies have followed suit, using rail carts and electric tugs to move heavy molds with minimal fuss. The result is that downtime shrinks, and production cycles speed up.
Speed-to-market can make or break automotive programs. When regulatory changes or consumer preferences shift, the ability to pivot quickly separates market leaders from followers.
There was a European manufacturer who faced a sudden safety regulation change affecting their side impact door components. Using traditional approaches, they would have missed their compliance deadline by weeks. By modifying and transferring existing molds, we had updated parts in production within nine days maintaining their certification timeline and avoiding costly penalties.
This responsiveness extends beyond crisis management. The repeating of the quicker product delivery, enabled by efficient transfers allows for more customer responsive design cycles. Rather than committing to unchangeable designs for years due to the cost of the mold investment, manufacturers can introduce refinements and improvements with each production run.
Precision is the Heart of Quality Parts
In automotive manufacturing, precision isn’t just a buzzword; it’s a non-negotiable. A mold that’s off by a fraction of a millimeter can produce parts that don’t fit, fail under stress, or compromise safety. Mold transfer services have to nail this. It’s not enough to move a mold, you need to ensure it performs like it’s brand new.
This is where skilled technicians and high tech equipment come in. Automated alignment tools and careful handling prevent damage during transfer. Sometimes, molds need minor tweaks to account for wear or new specs. If done right, the result is parts that meet the industry’s standards for engine components that withstand 200,000 miles or bumpers that ace crash tests.
For example, Thunderbird Molding has a six-step process to ensure precision during mold transfers. They evaluate the mold, document its condition, and even photograph it for quality assurance. Before shipping, they clean and coat it to prevent corrosion. Once it’s reinstalled, they run test shots to confirm everything’s perfect. It’s meticulous, but that’s what keeps vehicles safe and manufacturers’ reputations intact. An experienced transfer team reads these patterns like a mechanic diagnoses an engine, understanding which areas might need reinforcement or adjustment during the transfer process.
What’s Next for Mold Transfer Services?
The future looks bright. Automation and AI are poised to take mold transfer services to the next level. Imagine autonomous carts navigating molds from storage to production lines, adjusting on the fly to new specs. These innovations will cut human error and boost precision even further. And with sustainability climbing the priority list, reusing molds fits perfectly with economic goals. Less waste, lower energy use, and a smaller carbon footprint.
Seasonal shifts also play a role. As 2025 rolls into summer, manufacturers gear up for new model launches. Mold transfer services let them pivot quickly, whether it’s tweaking a mold for a hybrid vehicle’s battery casing or adapting one for a redesigned grille. Staying ready in a fast moving industry is the name of the game.
As someone who’s helped transform dozens of production floors through optimized mold transfer programs, I can attest to their transformative potential. The question isn’t whether you can afford to implement these practices,it’s whether you can afford not to.
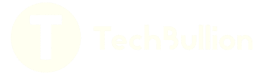