Introduction
The metalworking and fabrication sector has been put to the test in recent years by changes in worker demographics and technological advancements. The worldwide COVID-19 epidemic has brought further difficulties. Given that the metalworking and fabrication sector is composed of several smaller businesses that might not be as resilient as bigger ones, the pandemic may have had a more detrimental effect. However, for those who are able and ready to adjust to the times, this business appears to have a promising future.
According to the North American Industry Classification System (NAICS), the manufacture of fabricated metal products (code 332) and metalworking machinery (code 3335) are the two biggest industry sectors. Together, these two industries employ around 1.6 million people and have about 80,000 enterprises. This equates to around 19 employees per location on average.
Why Metalworking Technology Matters More Than Ever
There are a lot of companies in this business, which are still robust and vibrant. But a lot of them are still having trouble recovering from the COVID-19 epidemic. Since it is an upstream industry and essential to the mass production of metal items with the same form, it is anticipated that the mould and die sector, which is crucial to the fabrication of metal products, would supply the required impetus.
Over the next five years, the sheet metal processing market is anticipated to increase due to rising needs in a variety of industries, including manufacturing, construction, aerospace, automotive, architecture, electronics, food processing, telecommunications, and many more.
Vantage Market Research estimates that the worldwide metalworking market will increase at a compound annual growth rate (CAGR) of 3.2% from 2021 to 2028, from its 2020 valuation of $11 billion to $14.15 billion.
In addition, the Russo-Ukrainian conflict, logistical difficulties, concerns about a deepening recession, and the COVID-19 pandemic’s aftereffects are all predicted to contribute to the volatility of “Aluminum”‘s growth. Since aluminium requires around 40 times as much energy to produce as copper, the rising cost of energy continues to pose a danger to the supply of aluminium.
The Metalworking Tools List
In the metalworking industry, metal fabrication tools are the most widely used machinery for metal cutting and shaping tasks. Additionally, special purpose machines are designed to carry out certain tasks on a particular product.
The purpose of these machine tools is to increase the rate of manufacturing.
1. Lathe Machine
Lathes are metalworking devices that use rotation to carry out a variety of machining tasks. Wood, polymers, and ferrous and non-ferrous metals can all be used to make parts on a lathe.
These are multifunctional machines that may be used for drilling, boring, threading, turning, sanding, knurling, and cutting. They have a variety of attachments and come in different sizes.
Since ancient times, lathes have been employed mostly for precise work. They are found in machine shops and metalworking businesses that have heavy machinery, as well as firms that make light machinery parts.
2. Milling Machine
A metalworking instrument called a milling machine utilises rotary cutters to chop away unwanted material. A revolving tool may be rotated vertically around the mobile work table, which holds the workpiece securely.
Face milling and peripheral milling are the two main tasks that a milling machine completes. In peripheral milling, the cutter is positioned parallel to the workpiece, whereas in face milling, the operator cuts a flat surface at a right angle to the cutter’s rotation.
They may be used for everything from basic cutting to intricate drilling and shaping. Most metalworking firms have milling machines because of their flexibility.
3. Grinding Machine
An abrasive wheel is designed to spin at comparatively high speeds in a grinding machine. The workpiece is finished by the revolving wheel, which removes a very little amount of material from its surface, leaving it smooth to the touch.
Pieces that have been cut using other instruments, such saws or lathes, can have their surfaces shaped, flattened, and smoothed with grinders. In order to repaint or restore items, abrasive materials can also be used to remove paint or corrosion.
Grinding machines are an essential component of every metalworking manufacturing process because of their versatility and accuracy.
4. Drilling Machines
One of the most prevalent equipment types that we frequently find in metalworking shops is the drilling machine. They are also frequently employed for a variety of home maintenance tasks.
A drilling machine is very straightforward to operate since its tools are simple to install and replace. They may be used to drill holes in a variety of materials, such as concrete, cement, and metals.
5. Shaper Machines
A shaper machine cuts a workpiece by use of a single-point cutting tool that travels linearly. It is easy to use and has a straightforward operation.
Metal can be chopped, shaped, or formed into the required shape using these mills. They can reach all edges of the cloth since they are usually installed on a table.
Sheet metal is one kind of workpiece that benefits from these machines as they can effortlessly form intricate patterns like an arc in a single pass. They are widely used in the business, as you can easily imagine.
6. Broaching Machines
A broaching machine can cut, shape, and form a wide range of materials. It removes material from the workpiece with a broach or a toothed tool.
Broaching procedures come in two varieties: rotary and linear. The machine is positioned in line with the workpiece in linear broaching, which is the more popular of the two methods. However, when applying the broach to the workpiece in rotary broaching, it rotates.
Broaches are multipurpose instruments with several applications across numerous sectors. They produce a wide range of goods for specialists in the field that work on metalworking projects.
7. Saw Machines
The hacksaw, circular saw, and band saw are the three different kinds of saw machines. A piece of metal may be divided into smaller pieces using these equipment.
Band Saw
The band saw is an excellent tool for cutting wood and metal. Long objects, such pipes or solid bars, may be made using it in vast quantities and at any length.
Circular Saw
Both portable and table saw versions of circular saws employ a circular blade that reciprocates or revolves to cut. One of the most adaptable saw machine types for use in industrial settings is the circular saw.
Hacksaw
The hacksaw is arguably the most well-known saw. This hand-powered device can cut through a variety of metal items, including pipes, rods, and even sheet metal, thanks to its straight blade with several tiny teeth.
8. Planer Machine
Shaper machines and planar machines are extremely similar. Actually, this machine differs mainly in that the workpiece is designed to move linearly while the cutting tool remains fixed. These machines are often bigger than shaper machines as well.
By shaving off some superfluous material during machining operations, they are used to decrease the thickness and size of materials such as steel plates, bars, and rods. Additionally, it may be used to smooth out uneven or rough surfaces.
9. Shearing Machine
Sheet metal may be cut into the appropriate shapes and sizes using a shearing machine. The fact that the shearing operation leaves no chips or leftover material makes these metalworking machines perfect for industrial shops since it minimises the amount of trash that ends up on the floor and in the air.
Shearing machines are essential for the majority of industrial metalworking activities, much like the other pieces of equipment on this list. Blanking and piercing are two other significant metal cutting processes that resemble shearing.
10. Hobbing Machines
The quality and productivity of production processes have significantly increased in metalworking sectors because of the usage of hobbing machines. They are a sort of milling machine that produces high-precision shafts, gears, splines, and other cylindrical parts required for a variety of applications using a unique kind of cutting tool.
Game-Changing Advances in Metalworking Technology
The metal fabrication business has seen a number of technological advancements and changes in recent years that have altered its landscape. These include sophisticated materials, computer-aided design and manufacture, additive manufacturing, automation and robots, 3D printing, and the combination of Industry 4.0 and the Internet of Things.
1. Automation and Collaborative Robotics
Robots have long been used in the metal production business, mostly for jobs that are considered too risky for human workers. However, conventional robots needed specific workspaces and were big.
As robotics technology has advanced, collaborative robots, or cobots, have appeared that can safely do jobs alongside human workers.
2. 3D Printing and Additive Manufacturing
Once seen as just a tool for enthusiasts, 3D printing has swiftly emerged as a useful tool in many other industries, including metal manufacturing. In the metal fabrication sector, additive manufacturing, commonly referred to as 3D printing, offers unmatched degrees of customization.
3. Implementing Automation and CNC Machines
Until recently, computer numerical control (CNC) machines needed programming and human involvement to operate, despite being an essential component of the metal production sector. Long-term efficiency and productivity can be increased by automating the CNC part of metal manufacturing to eliminate some repetition in this process.
4. Internet of things (IoT) and Industry 4.0
Controlling metal production equipment is becoming more and more dependent on the Internet of Things (IoT). Metal manufacturing equipment may be equipped with sensors and Internet of Things devices to give real-time data for performance and use monitoring. The operation and maintenance of the equipment may then be optimised with the use of this data, increasing productivity and lowering costs.
5. Computer-Aided Design (CAD) and Computer-Aided Manufacturing (CAM)
Because it enables more accuracy and efficiency in the design and manufacturing process, computer-aided design (CAD) and computer-aided manufacturing (CAM) software are being used more and more in metal fabrication. Designers and engineers may produce precise, in-depth 3D models of the components or goods they wish to generate using CAD software.
6. Embracing Digitisation
The adoption of new technology in metal manufacturing has been comparatively gradual, despite the continuous digital revolution in many sectors. It’s crucial to remember, though, that using technology-based platforms does not equate to displacing human labour.
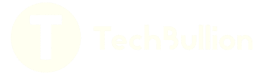