Additive Manufacturing (AM), also known as 3D printing, is one of the most transformative technologies of our time, revolutionizing industries ranging from aerospace and medical devices to automotive manufacturing. This technology not only enables the creation of complex parts but also offers engineers unparalleled freedom in design. However, success in additive manufacturing is not solely dependent on advanced equipment; precise simulations play a key role in achieving optimal results. A striking contrast with subtractive machining is often observed, as outlined below.
What is CNC Machining Technology?
CNC (Computer Numerical Control) machining uses pre-programmed software to control the movement of tools such as drills and lathes. This technology is widely used for the production of precise and durable parts and is well-suited for materials like metals, plastics, and composites. The precision and versatility of CNC machining make it indispensable in industries where exact specifications are critical, such as automotive, aerospace, and the manufacturing of medical devices. However, as effective as it is, CNC machining has its limitations, particularly when it comes to creating highly intricate or customized designs.
Differences Between Additive Manufacturing and CNC Machining
Additive manufacturing builds objects layer by layer, adding only the necessary material. In contrast, CNC machining is a subtractive process that removes material from a solid block to create the desired shape. These fundamental differences lead to:
- Material Usage: Additive manufacturing minimizes waste, whereas CNC often results in significant material loss.
- Complexity: Additive manufacturing can produce highly intricate designs, such as lattice structures, which are challenging for CNC.
- Time Efficiency: CNC machining is faster for simple parts, but additive manufacturing excels in rapid prototyping and complex geometries.
The Importance of Simulation in Additive Manufacturing
While additive manufacturing offers unique design capabilities, its engineering and process complexities present significant challenges. Traditional trial-and-error methods are often inefficient due to high costs and time constraints. Advanced simulations not only optimize processes but also reduce costs and accelerate production cycles.
With Abaqus, complex geometries and material layouts can be analyzed before actual production. This ensures the final design is structurally stable and performs optimally under ideal conditions.
Now, how to learn Abaqus additive manufacturing simulation? From where we can start? In the following, we will introduce several ways to do that.
Advanced Courses:
CAEassistant : Specialized courses on 3D printing simulation using Abaqus additive manufacturing simulation .
One standout feature of CAE Assistant is its focus on specialized and practical courses, such as 3D printing simulation in Abaqus. These courses incorporate real-world projects and provide detailed guidance, making learning more effective for engineers. Additionally, its robust support services and tools, like custom plugins tailored for specific needs, distinguish it from other learning platforms.
The CAE Assistant 3D printing tutorial covers two methods for additive manufacturing simulation:
- Python for Abaqus: Tutorials on scripting for custom analysis.
- AM Modeler Training: Courses on using specialized 3D printing plugins.
Studying Official Abaqus Documentation:
Dassault Systèmes Documentation: Official guides including mechanical and thermodynamic analyses.
Abaqus Benchmarks: Validated analyses for specific simulations.
Webinars and Conferences:
Dassault Systèmes Events: Free specialized webinars.
NAFEMS: Renowned engineering conferences focusing on numerical simulations.
Industrial Projects:
LinkedIn Learning: Practical projects with real-world applications.
Academic Publications: Research papers focusing on industrial Abaqus applications.
YouTube Videos
You can search in YouTube with the keyword “3D printing simulation” or its variation and watch the top videos in top channels regarding the 3D printing simulation in Abaqus or any other software you need.
The 8 Primary Methods of Additive Manufacturing
Additive manufacturing encompasses several methods, each suited to specific types of materials and applications. Here are the seven main techniques:
- Fused Deposition Modeling (FDM): Ideal for rapid prototyping and low-cost production, FDM is widely used for creating simple models and parts that don’t require complex material properties.
- Stereolithography (SLA): Produces highly accurate parts with smooth surfaces, making it ideal for prototypes and parts that require fine details and high precision.
- Selective Laser Sintering (SLS): Known for its ability to create durable and functional parts, SLS is often used in industries like aerospace and automotive, where material strength and durability are crucial.
- Direct Metal Laser Sintering (DMLS): Used for creating strong, high-performance metal parts, DMLS is particularly effective for aerospace and medical device applications where structural integrity is paramount.
- Binder Jetting: Suitable for multi-material parts, binder jetting allows for the production of objects that require complex material compositions, including metals and ceramics.
- Material Jetting: Known for producing highly detailed parts with excellent surface finish, material jetting is used in industries where fine details and high resolution are needed.
- Electron Beam Melting (EBM): Ideal for high-performance metal parts, EBM is often used in industries like aerospace, where the parts must perform under extreme conditions.
- Laser Powder Bed Fusion (LPBF): Known for its precision and versatility, LPBF is a highly advanced technique that uses a laser to selectively melt fine metal powder layer by layer, creating dense, high-performance parts. LPBF is widely used in industries such as aerospace, medical, and automotive, where complex geometries, fine details, and exceptional material properties are essential.
Key Features of Abaqus for Additive Manufacturing Simulation
As a leading finite element analysis (FEA) software, Abaqus is renowned for its advanced tools and capabilities tailored for additive manufacturing. Key features include:
- Thermal-Mechanical Coupling
Abaqus accurately models the interaction between thermal and mechanical effects, essential for predicting distortions and residual stresses caused by thermal gradients.
- Advanced Material Models
Abaqus offers extensive material libraries for simulating metals, polymers, and composites. These libraries handle temperature-dependent properties, phase changes, and anisotropy.
- Layer-by-Layer Process Simulation
Abaqus provides precise analysis of heat accumulation and residual stress development during the layer-by-layer process.
- Scripting and Automation Capabilities
Abaqus supports Python scripting, enabling users to automate repetitive tasks, develop custom material models, and integrate external software tools into their workflows.
Practical Applications of Abaqus in Additive Manufacturing
- Aerospace
In aerospace, where complex parts with high performance are essential, Abaqus simulations help reduce residual stresses and ensure structural integrity under extreme conditions.
- Medical Devices
Abaqus is used to design and analyze custom implants and prosthetics, considering the mechanical properties of biocompatible materials and complex geometries to ensure optimal performance.
- Automotive Industry
Abaqus aids in designing lightweight, cost-effective, and durable components that meet performance and safety standards while optimizing production costs.
- Consumer Electronics
Abaqus simulates components that balance aesthetics and mechanical strength, ensuring high-quality products that perform well under real-world conditions.
conclusion
Additive manufacturing and CNC machining offer distinct advantages, serving as essential tools for modern industries. While additive manufacturing excels in design flexibility and material efficiency, CNC machining remains critical for precision and durability. The synergy between advanced technologies, such as Abaqus for simulation, enables the optimization of these processes, ensuring better performance and reduced costs. By leveraging tailored resources and continuous learning, engineers can harness the full potential of these methods to meet the demands of innovative, high-performance applications across various industries.
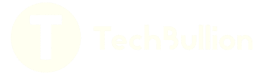