Walk onto any modern manufacturing floor, and you’ll see a network of machines, conveyors, and controls working in tandem to deliver high volumes of packaged goods. But behind the smooth flow of products is often something less visible—a strategic integration of systems engineered to reduce downtime, improve accuracy, and maximize throughput.
This is where a packaging system integrator proves invaluable. These specialists design, coordinate, and implement packaging systems that align with production needs, ensuring seamless communication between machines and optimizing every step of the line. Their work turns a collection of equipment into a fully synchronized operation.
Creating Cohesion Across Multiple Machines
Packaging lines typically involve a mix of machines—fillers, labelers, case packers, shrink wrappers, and more—each with its own controls and capabilities. Without a unifying strategy, these machines can work against each other, leading to inefficiencies and frequent slowdowns.
A packaging system integrator ensures all machines communicate effectively through centralized control systems and automation logic. This allows processes to run in harmony, with materials moving smoothly from one step to the next, minimizing delays and manual intervention.
Identifying and Solving Workflow Gaps
Even small inefficiencies can snowball into significant production losses over time. System integrators assess entire packaging lines to identify where bottlenecks or idle time are occurring. Once identified, they make adjustments—reconfiguring equipment placement, fine-tuning speeds, or implementing better sequencing to keep products flowing efficiently.
These adjustments don’t just boost output—they also reduce mechanical stress on equipment and cut down on waste, helping extend system life and reduce maintenance needs.
Tailoring Solutions to the Operation
Every facility has its own space constraints, throughput targets, and unique product mix. A packaging system integrator builds custom solutions around those specifics. They consider your layout, goals, and long-term growth plans to create a packaging system that meets your current needs and can scale in the future.
Whether your focus is food safety, speed, or flexibility, a tailored system outperforms off-the-shelf solutions and delivers consistent results under real-world conditions.
Making Data Work for You
Most packaging systems today are rich with data. Integrators make sure that data is accessible and useful. By linking equipment to plant-wide control systems, dashboards, or MES platforms, you gain insight into key metrics like downtime, throughput, and quality performance.
Real-time data allows operators to react quickly and managers to make informed decisions. Over time, these insights support continuous improvement, driving higher efficiency across the entire line.
Simplifying Operations and Support
Without integration, each machine might come from a different vendor, with its own user interface, maintenance requirements, and update schedule. This makes operations more complex and troubleshooting more time-consuming.
An integrator simplifies this by unifying controls and creating centralized monitoring systems. When issues arise, operators know exactly where to look—and downtime is minimized. Long-term, this makes system upgrades and expansions far easier to manage.
From machine compatibility to real-time visibility, a packaging system integrator brings structure and strategy to complex production environments. Instead of working harder to overcome inefficiencies, integrated packaging lines work smarter—delivering higher output with greater reliability.
If your packaging process feels fragmented or underperforming, it may be time to explore the benefits of system integration. With the right partner, you can transform your operation into a well-synchronized, high-efficiency production line.
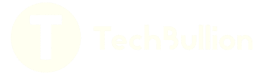