Welding plays a crucial role in the aerospace industry, ensuring the strength, durability, and precision of components used in aircraft and spacecraft. As aerospace engineering pushes the boundaries of innovation, traditional welding methods are being replaced by cutting-edge technologies. These advancements are improving the efficiency of manufacturing processes and enhancing the performance and safety of aerospace structures. From robotic automation to novel materials and hybrid welding techniques, these developments are transforming the way aerospace engineers design, fabricate, and maintain critical components in flight systems.
Friction Stir Welding
One of the most revolutionary welding technologies now widely used in aerospace is Friction Stir Welding (FSW). Unlike traditional fusion welding, FSW is a solid-state process that doesn’t melt the materials. Instead, it uses a rotating tool to generate frictional heat and plastic deformation at the welding zone, effectively joining the materials. This method significantly reduces the chances of defects like cracks and porosity, making it ideal for joining high-strength aluminum alloys commonly found in aircraft fuselages. Boeing and Airbus, for instance, have incorporated FSW into their production lines due to its ability to produce stronger, lighter joints. The precision and repeatability of FSW help minimize material waste and improve structural integrity, which are crucial for fuel efficiency and flight performance.
Robotics and Automation Streamline Production
Robotic welding arms equipped with advanced sensors and real-time monitoring systems can perform complex welds with unmatched accuracy. These systems reduce variability between welds and lower the chances of human error, especially in repetitive tasks. Automation has become indispensable in modern aerospace welding, driven by the need for precision, consistency, and speed. Automation ensures a level of quality and reliability that manual methods can’t consistently match. Robots can operate in hazardous or confined environments, enhancing workplace safety and efficiency. The increased use of collaborative robots (cobots) further allows skilled technicians to work alongside automated systems, combining the best of both worlds.
Laser Welding Enhances Speed and Accuracy
Laser welding is another standout advancement that has been gaining traction in the aerospace sector. By using high-energy laser beams, this technique delivers pinpoint accuracy and incredible speeds, perfect for intricate or delicate components found in aircraft and spacecraft. Laser welding also excels in working with reflective or hard-to-weld materials such as titanium and nickel-based superalloys, which are commonly used in engine parts and structural assemblies. The heat-affected zone (HAZ) in laser welding is minimal, reducing the risk of thermal distortion or weakening of the surrounding material. Aerospace manufacturers benefit from its automation potential, which allows integration into robotic arms and CNC machines for continuous, high-volume production with minimal human error.
Additive Manufacturing Integration
The convergence of additive manufacturing (AM), also known as 3D printing, with welding technologies is paving the way for unprecedented flexibility in aerospace design and fabrication. Techniques like Directed Energy Deposition (DED) and Electron Beam Additive Manufacturing (EBAM) essentially use welding principles to build up parts layer by layer. These hybrid approaches are ideal for repairing damaged components or producing complex parts that would be impossible or too costly to make with traditional subtractive methods. By integrating welding into the additive process, engineers can reinforce specific sections of a part for added strength or customize components on the fly. This capability shortens lead times and supports the trend toward lightweight, efficient aircraft structures.
Advanced Materials Require Innovative Welding Solutions
As aerospace engineering increasingly turns to advanced composites, ceramics, and high-performance metal alloys, traditional welding techniques often fall short. This shift necessitates new approaches tailored to these materials’ unique properties. Materials like titanium require precise control over shielding gases to prevent oxidation during welding, while nickel alloys used in turbine engines demand techniques that can withstand extreme temperatures and stress. Laser beam and electron beam welding have emerged as go-to options due to their ability to produce high-quality welds in challenging materials. Innovations like ultrasonic welding and hybrid welding systems—combining multiple techniques—are also being developed to accommodate emerging materials without compromising joint integrity or performance.
Digital Monitoring and Quality Control Systems
In a field as exacting as aerospace, quality assurance is just as important as the welding process itself. Technological advancements now allow real-time monitoring of welding parameters, including temperature, pressure, and weld penetration, using sensors and AI-driven analytics. These systems detect anomalies on the fly and adjust settings to maintain weld quality automatically. Post-weld inspection methods like phased array ultrasonic testing (PAUT) and 3D laser scanning offer non-destructive evaluation with exceptional accuracy. This shift toward data-driven welding ensures that every joint meets strict aerospace standards, reduces the likelihood of defects going unnoticed, and streamlines the certification process. Manufacturers can achieve higher production standards while minimizing costly rework and delays.
The landscape of aerospace engineering is being reshaped by groundbreaking welding technologies that combine precision, efficiency, and adaptability. From solid-state welding methods like Friction Stir Welding to the integration of robotics, additive manufacturing, and AI-driven quality control, each advancement contributes to creating safer, more efficient, and more resilient aircraft and spacecraft. As the industry continues to evolve, welding technology will remain at the core of innovation, ensuring that aerospace engineering continues to soar to new heights.
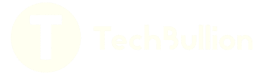