A servo motor is a rotary actuator or linear actuator that allows for precise control of angular or linear position, velocity, and acceleration. It consists of a suitable motor coupled with a sensor for position feedback. The motor is usually a standard DC motor, but it can also be an AC motor or a brushless DC motor. The position feedback sensor is typically a potentiometer for rotary servos or an encoder for more advanced servos.
Servo Motor
Basic Components
Motor
The motor is the core component that provides the mechanical power to move the output shaft. It can be a small DC motor in simple hobbyist servos or a more powerful and precise motor in industrial servos.
Position Sensor
For rotary servos, a potentiometer is commonly used. It is connected to the output shaft and provides a voltage signal proportional to the shaft’s angle. In more sophisticated servos, an encoder can be used, which provides a digital signal with higher precision and resolution.
Gear System
The gear system is used to reduce the speed of the motor and increase its torque. This allows the servo to produce a higher output torque at a lower speed, which is necessary for precise positioning. The gear ratio determines the relationship between the motor speed and the output shaft speed.
Control Circuit
The control circuit processes the feedback signal from the position sensor and compares it with the desired position signal. It then adjusts the motor’s speed and direction to drive the output shaft to the desired position. The control circuit usually includes a microcontroller or a dedicated servo controller chip.
Working Principle
The servo motor operates on a closed-loop control system. When a control signal is sent to the servo, the control circuit compares this signal with the feedback signal from the position sensor. If there is a difference between the desired position and the actual position, the control circuit sends a signal to the motor to rotate in the appropriate direction and at the appropriate speed to reduce this difference. This process continues until the desired position is reached and the difference is minimized.
Types of Servo Motors
Rotary Servo Motors
These are the most common type of servo motors. The output shaft rotates within a certain range, usually 0 to 180 degrees or 0 to 360 degrees. They are widely used in applications such as robotic arms, RC (radio-controlled) vehicles, and CNC machines.
Continuous Rotation Servo Motors
Unlike standard rotary servos, continuous rotation servos can rotate continuously in either direction. They are modified versions of regular servos and are often used in applications where continuous motion is required, such as in the wheels of a robot.
Linear Servo Motors
Linear servos convert the rotary motion of the motor into linear motion using a lead screw or a rack and pinion mechanism. They are used in applications where linear movement is needed, such as in linear actuators, CNC machines, and robotic grippers.
Applications
Robotics
Servo motors are extensively used in robotics for controlling the movement of robotic arms, legs, and other joints. They enable precise positioning and movement, allowing robots to perform complex tasks.
RC Vehicles
In radio-controlled cars, boats, and airplanes, servo motors are used to control the steering, throttle, and other functions. They provide accurate control and quick response, which is essential for the performance of these vehicles.
Industrial Automation
In manufacturing and industrial automation, servo motors are used in CNC machines, pick-and-place machines, and other automated equipment. They offer high precision, repeatability, and reliability, which are crucial for maintaining the quality and efficiency of the production process.
Consumer Electronics
Servo motors are also used in consumer electronics such as cameras for zoom and focus control, and in printers for paper feeding and print head positioning.
Advantages
High Precision
Servo motors can achieve very precise positioning, making them suitable for applications that require high accuracy.
Fast Response
They can respond quickly to control signals, allowing for fast and dynamic movement.
Torque Control
The gear system allows servo motors to produce high torque, which is useful for applications that require strong force.
Compact Size
Many servo motors are small and lightweight, making them easy to integrate into various systems and devices.
Limitations
Limited Range of Motion
Rotary servos have a limited range of motion, typically up to 180 or 360 degrees. For applications requiring full rotation, other types of motors or modifications are needed.
Cost
High-precision servo motors can be relatively expensive compared to other types of motors, especially for industrial-grade servos.
Complexity
The closed-loop control system and the need for position feedback sensors add complexity to the design and implementation of servo motor systems.
Conclusion
Servo motors are versatile and precise actuators that play a crucial role in a wide range of applications, from hobbyist projects to industrial automation. Their ability to provide accurate control of position, velocity, and acceleration makes them indispensable in modern engineering and technology.
Related Articles
RJ45 Connectors: A Comprehensive Guide
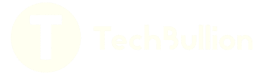