The liquid packaging industry is a labyrinth of precision, where even minor oversights can cascade into costly errors. From cosmetics to pharmaceuticals, food-grade beverages to industrial chemicals, the demand for flawless packaging solutions grows fiercer by the day. Yet, manufacturers often grapple with erratic viscosity, unpredictable temperature control, and the elusive balance of particle size distribution. These challenges aren’t just technical hiccups—they’re barriers to efficiency, brand trust, and market competitiveness.
Enter the expertise of a seasoned filling machine manufacturer. With decades of innovation, companies like Yundu Filling Machine have refined strategies to transform these obstacles into opportunities. This article unveils actionable insights to optimize your liquid packaging processes, blending cutting-edge technology with time-tested practicality.
The Triad of Liquid Packaging Challenges
Liquid packaging is rarely a one-size-fits-all endeavor. Below, we dissect the three most pervasive hurdles—temperature control, particle size, and viscosity management—and reveal how advanced filling equipment can mitigate them.
1. Temperature Control: The Silent Saboteur
Temperature fluctuations are the invisible foe of liquid packaging. Heat-sensitive products like essential oils or vaccines demand unwavering thermal stability, while substances like chocolate syrup or adhesives require precise heating to maintain flowability. A single degree of deviation can alter viscosity, clog nozzles, or compromise product integrity.
Solution:
- Invest in filling machines with integrated thermal regulation systems.
- Utilize jacketed tanks to maintain consistent temperatures during storage and transfer.
- Opt for sensors that monitor real-time heat levels, triggering adjustments automatically.
Recommended Equipment:
- Tube filling machines with heated hoppers for viscous products.
- Aseptic fillers with sterile cooling zones for pharmaceuticals.
2. Particle Size: When Uniformity Meets Chaos
Liquids containing suspensions—think skincare serums or protein shakes—rely on homogenous particle size distribution. Agglomeration or sedimentation mid-filling can lead to inconsistent dosing, clogged valves, or consumer dissatisfaction.
Solution:
- Deploy agitation systems within storage tanks to prevent settling.
- Use high-shear mixers to break down clusters before filling.
- Select piston fillers for products with delicate particulates, as they minimize shear stress.
Recommended Equipment:
- Blister packaging machines for precision dosing of particulate-heavy liquids.
- Rotary fillers with inline homogenizers for large-scale production.
3. Viscosity Management: The Art of Flow
Viscosity—the measure of a liquid’s resistance to flow—can make or break packaging efficiency. Thin solvents demand leak-proof precision, while thick pastes require robust pumps to avoid underfilling.
Solution:
- Match filling equipment to viscosity ranges (e.g., gear pumps for syrups, peristaltic pumps for abrasive slurries).
- Implement automated viscosity sensors to adjust filling speed dynamically.
- Prioritize sanitary design to reduce residue buildup in high-viscosity applications.
Recommended Equipment:
- Positive displacement fillers for non-Newtonian fluids like ketchup or lotions.
- Gravity-based fillers for low-viscosity liquids such as water or alcohol.
The Role of Advanced Filling Equipment in Modern Packaging
Modern challenges demand modern solutions. Below, we spotlight packaging solutions engineered to tackle today’s demands while future-proofing operations.
Equipment Type | Best For | Key Features |
Tube Fillers | Cosmetics, Pharmaceuticals | Hygienic design, adjustable stroke length |
Aseptic Fillers | Dairy, Juices | Sterile environments, ultra-high speed |
Piston Fillers | Sauces, Adhesives | High accuracy, easy cleanup |
Rotary Fillers | Beverages, Chemicals | Scalability, multi-nozzle configurations |
Bridging Innovation and Practicality: Expert Recommendations
While technology is pivotal, success hinges on aligning machinery with operational realities. Consider these strategies:
- Automation Integration: Pair filling machines with IoT-enabled systems for predictive maintenance and data-driven adjustments.
- Material Compatibility: Ensure equipment components (e.g., seals, valves) resist chemical corrosion or wear.
- Sustainability Focus: Opt for energy-efficient motors and recyclable material handling systems.
For tailored advice, consult a filling machine manufacturer like Yundu Filling Machine, whose engineers specialize in customizable solutions for niche industries.
Conclusion:
The complexities of liquid packaging need not be a bottleneck. By embracing adaptive filling equipment, leveraging data-driven insights, and partnering with experts, manufacturers can achieve production efficiency, product consistency, and brand credibility.
Ready to Transform Your Packaging Line?
As a trusted filling machine manufacturer, Yundu Filling Machine combines innovation with reliability. Whether you’re battling temperature control nuances or seeking hygienic packaging solutions, our team is poised to elevate your operations. Contact us today for a consultation—because precision shouldn’t be a compromise.
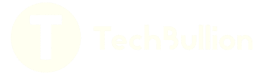