The injection moulding industry is an integral part of the manufacturing industry in a wide range of industries, including automotive, consumer goods, and more. In countries such as Mexico, where manufacturing plays a significant role in the economy, the need for high-quality, efficient production processes is paramount. Mold temperature controller have become an essential tool for optimizing the injection moulding process. These devices are designed to regulate the temperature of the mould during the production process, ensuring that moulded parts are of consistent quality, dimensionally accurate, and free of defects. This article explores the key benefits that mould temperature controllers offer the Mexican injection moulding industry and provides insight into how they can increase production efficiency, reduce costs, and improve product quality.
Mould Temperature Controllers: Improving Efficiency in the Mexican Injection Molding Industry
Mould temperature controllers are essential for optimizing cycle times and ensuring that the production process runs smoothly. In the Mexican injection moulding industry, manufacturers face the ongoing challenge of maintaining efficiency while managing energy consumption and reducing waste. Engineers specifically design them to regulate mould temperature and prevent overheating, which can lead to product defects and costly delays. By maintaining the mould temperature at an optimal level and helping to reduce cycle times and increase output, they boost productivity. In addition, temperature controllers minimize the risk of production downtime because they provide real-time monitoring and adjustments to ensure that mould temperature remains within the desired range. This can improve overall operational efficiency, benefiting both large manufacturers and small, high-precision moulding operations.
Reduce Production Costs with Mould Temperature Controllers
One of the main benefits of mould temperature controllers in the injection moulding process is their ability to help reduce production costs. In the competitive Mexican market, manufacturers face constant pressure to reduce operating costs while maintaining product quality. Optimizing temperature control in the mould helps prevent costly issues such as material waste, production delays, and energy inefficiencies. For example, they ensure that temperatures remain stable, preventing overcompensation that results in excessive energy or material use. In addition, these devices help extend the life of the mould, reducing the need for frequent replacements or repairs that can add up over time. By preventing defects caused by inconsistent mould temperatures, mould temperature controllers minimize the likelihood of product rejection, scrap, and rework.
Improve Product Quality with Consistent Mould Temperature Control
Maintaining consistent mould temperatures is critical to ensuring the quality and integrity of moulded parts. Temperature variations can cause inconsistent material flow, which can lead to surface defects, poor dimensional accuracy, and weak spots in moulded products. Mold temperature control is an indispensable tool for Mexican manufacturers looking to win with quality in the global market. By precisely controlling temperature throughout the injection molding process, they keep the mold at the optimal temperature for the material being used, preventing defects such as short shots, flashes, or warping. Maintaining consistent temperatures also reduces the risk of thermal cycling, which can compromise the integrity of the final product. With mould temperature controllers, manufacturers can produce high-quality parts that meet stringent international standards and customer specifications.
How can I improve energy efficiency in injection moulding in Mexico?
Energy consumption is a significant concern for manufacturers in Mexico, where rising electricity costs and environmental regulations are forcing companies to adopt more energy-efficient practices. Mould temperature controllers play a vital role in improving energy efficiency by ensuring that mould temperatures are precisely regulated and energy is used efficiently. By maintaining a constant temperature, mould temperature controller prevent the overuse of heating and cooling systems, which often occur when mould temperatures fluctuate or are poorly controlled. This helps manufacturers reduce energy consumption, lower utility bills and reduce environmental impact. Implementing mould temperature controllers meets economic and environmental goals in the context of Mexico’s growing emphasis on sustainability and energy conservation. In addition, they monitor energy usage in real-time, allowing manufacturers to track and optimize energy consumption.
Role in Extending Mold Life
The life of an injection mould is an essential factor in determining the overall cost-effectiveness of a moulding operation. Replacing or repairing a mould can be an expensive and time-consuming process, which is why many manufacturers in Mexico are turning to mould temperature controllers to extend mould life. Moulds exposed to fluctuating or extreme temperatures tend to degrade more quickly, leading to surface wear, cracking, or other forms of damage. Regulating mould temperature and ensuring it remains within an optimal range help prevent thermal stress and reduce the likelihood of mould-related damage. Consistent and even temperature distribution also minimizes the risk of hot spots that can cause uneven mould wear.
Ultimately
Mould temperature controllers have become essential tools in the Mexican injection moulding industry. They offer a range of benefits that increase operational efficiency, reduce costs, improve product quality, and extend mould life. As the industry continues to evolve, the importance of these devices will only increase, especially as Mexican manufacturers strive to remain competitive in an ever-changing global market.
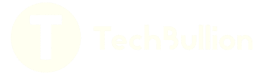