Tensile testing is an integral part of material evaluation in both the aerospace and automotive industries, integral to determining mechanical properties such as tensile strength, ductility, and elasticity. These industries rely on tensile testing to verify that materials can withstand demanding conditions in service. However, while both sectors use similar testing principles, the sample preparation process differs significantly due to the distinct operational requirements and performance expectations in each field.
Aerospace applications require extreme stresses, high temperatures, and dynamic loads, necessitating advanced alloys and composite materials. Precision in tensile test sample preparation, especially for flat specimens, is critical to reliable data. The automotive industry, on the other hand, focuses on efficiency, cost-effectiveness, and mass production, often using round specimens for tensile testing to evaluate structural steels and lightweight aluminum alloys used in vehicle manufacturing.
Understanding these differences in material selection, sample geometry, and preparation techniques is a necessary step for engineers, manufacturers, and researchers working in material testing. Proper tensile test sample preparation guarantees accuracy in results, aiding in material certification, product development, and compliance with international standards.
Material Selection and Specimen Geometry
Aerospace and automotive materials are fundamentally different due to the unique performance demands of each industry. Aerospace components must prioritize high strength-to-weight ratios, resistance to extreme environmental conditions, and long-term structural reliability. Automotive materials, while also requiring strength and durability, are selected based on affordability, manufacturability, and impact resistance. These material choices directly influence tensile test sample preparation, including specimen geometry and machining processes.
Aerospace Industry: High-Performance Materials and Flat Specimens
In aerospace engineering, metals such as titanium alloys, aluminum-lithium alloys, and high-strength stainless steels are frequently used alongside composite materials like carbon fiber-reinforced polymers (CFRPs). These materials need to withstand high-altitude pressure variations, thermal fluctuations, and mechanical loads, making tensile testing a critical step in their development and certification.
Tensile specimens in the aerospace sector are predominantly flat specimens, which provide a uniform cross-section for evaluating anisotropic materials. Standards such as ASTM E8 specify precise dimensions and machining techniques for flat tensile samples, making sure that results are accurate and reproducible across different testing laboratories. Due to the high cost of aerospace-grade materials, every sample must be precisely cut and prepared to minimize waste while adhering to strict testing protocols.
Automotive Industry: Structural Steels, Lightweight Alloys, and Round Specimens
The automotive industry uses many types of metals, including high-strength low-alloy (HSLA) steels, aluminum alloys, and advanced high-strength steels (AHSS). These materials need to balance strength, weight reduction, manufacturability, and crash performance, leading to varied tensile testing requirements.
Unlike aerospace, automotive tensile test samples are often round specimens, particularly when testing structural steels and drivetrain components. The ASTM A370 standard outlines specifications for round tensile specimens, which are commonly used for bulk material testing and mass production evaluations. While some automotive parts, such as body panels, may require flat specimens, round samples are more frequently used in testing engine components, suspension systems, and fasteners.
Impact on Sample Preparation Techniques
Fundamental differences in material properties and specimen geometry between aerospace and automotive tensile testing affect sample preparation. Aerospace flat specimens require precision machining techniques, such as CNC milling or wire EDM cutting, to maintain a consistent thickness and minimize edge defects that could alter test results. In contrast, automotive round specimens are often turned and ground using lathes, thus providing uniform cross-sections and reducing machining time for high-volume testing.
Regardless of the industry, tensile sample preparation is key to achieving accurate and repeatable test results. Any deviations in specimen geometry, surface finish, or material processing can introduce stress concentrations, leading to premature failure and unreliable mechanical property measurements. As industries continue to push material performance limits, advancements in sample preparation techniques and machining technologies remain a necessity for consistent and high-quality tensile test results.
Precision in Tensile Test Sample Preparation: Aerospace vs. Automotive
Tensile test results depend not only on the material being tested but also on how the sample is prepared. In both the aerospace and automotive industries, strict sample preparation protocols guarantee accurate mechanical data without introducing artificial weak points. However, the level of precision required differs between the two sectors, as aerospace demands tight tolerances while automotive testing prioritizes efficiency and mass production.
Aerospace applications require every tensile test specimen to meet stringent industry standards. Flat specimens, commonly used for testing composites and high-strength alloys, require precision CNC milling or laser cutting to achieve perfectly uniform thickness and minimize surface irregularities. Even the polishing process is critical, as small surface imperfections could cause premature failure during testing. Additionally, because aerospace materials are often directionally dependent (anisotropic), sample orientation must be carefully controlled to match expected stress conditions in real-world applications.
In contrast, automotive tensile test sample preparation must balance accuracy with speed to accommodate high testing volumes. Round specimens are widely used, particularly when testing engine components and structural metals, and are often prepared using automated lathe machining. While precision is still important, the focus is on repeatability rather than extreme refinement, as the goal is to produce thousands of identical samples for consistent batch testing. In some cases, hot-rolled steel parts may require additional surface finishing, but for most mass-produced materials, streamlined machining and cutting techniques allow for adequate consistency without excessive processing time.
Despite these differences, quality control remains paramount in both industries. Whether preparing a flat aerospace specimen or a round automotive sample, test accuracy depends on eliminating variations in dimensions, surface roughness, and edge quality. Any inconsistencies in sample preparation could skew test results, leading to incorrect assessments of material performance and potential failures in real-world applications.
Specialized Equipment for Tensile Test Sample Preparation
Tensile test sample preparation requires highly specialized equipment to meet aerospace and automotive industries’ precision and efficiency demands. The choice of machinery depends on factors like material type, specimen geometry, and required accuracy so that prepared samples provide reliable mechanical data for testing.
Aerospace applications use CNC machining and laser cutting systems to fabricate flat tensile specimens with high precision. These systems offer excellent repeatability, maintain tight tolerances, and efficiently process advanced materials like titanium and carbon fiber composites. Since aerospace alloys are highly sensitive to mechanical stress and thermal exposure, sample preparation equipment must minimize heat-affected zones and prevent structural alterations that could affect testing outcomes.
In the automotive industry, where round tensile specimens are more common, lathe machining and automated milling systems dominate sample preparation. These machines are designed for high-speed processing, enabling manufacturers to produce large batches of test specimens from steel and aluminum alloys efficiently. Modern automotive production facilities incorporate robotic automation into their tensile sample preparation workflows, improving consistency while reducing operational costs.
Surface finishing also plays a critical role in tensile sample preparation, particularly in applications that require fatigue testing. To achieve the necessary surface roughness and defect-free finish, polishing systems are used in the final preparation stages. For example, companies such as TensileMill, provide longitudinal polisher systems that guarantee high-quality finishes while meeting strict fatigue testing standards. These systems are configured to comply with ASTM E466 for force-controlled axial fatigue tests, ASTM E647 for fatigue crack growth rate measurements, ASTM E606/E606M for strain-controlled fatigue testing, and ISO 12106 for metallic materials fatigue testing.
Selecting the right equipment—whether CNC machining for flat specimens, automated lathes for round specimens, or high-precision polishing systems—directly impacts tensile testing quality and accuracy. Properly prepared samples lead to more reliable mechanical data, supporting critical material evaluation processes in many different industries.
Bridging Precision and Efficiency in Tensile Testing
Despite their differences, aerospace and automotive tensile test sample preparations share a common goal: to guarantee reliable material performance through accurate testing. Aerospace applications prioritize extreme precision and controlled testing conditions, leading to careful sample preparation techniques, advanced CNC machining, and strict adherence to dimensional tolerances. In contrast, automotive applications focus on efficiency, cost-effectiveness, and large-scale testing, using automated lathe machining and high-volume processing techniques.
Both industries rely on round and flat specimens, but the level of refinement in preparation varies depending on the complexity of the materials and the end-use requirements. While aerospace demands flawless machining to prevent premature failure, automotive testing allows for streamlined preparation methods that maintain consistency over thousands of samples.
As material science advances, tensile sample preparation equipment evolves, bridging the gap between precision and efficiency. Whether for aircraft structures or vehicle frames, tensile testing accuracy remains a cornerstone of quality control, safety, and material innovation, making certain that both industries continue to push the limits of engineering excellence.
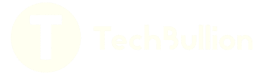