You’ve probably seen those little green boards inside phones or laptops. They’re called PCBs, and they help everything inside work together. For a long time, we used regular ones — nothing special.
But now, there’s a newer kind called HDI. It stands for High-Density Interconnect. Sounds complicated, but really, it just means it’s smaller and does more in less space.
More and more tech companies are using HDI instead of the old kind. Why? Because today’s devices are getting thinner, faster, and smarter — and HDI helps make that happen.
In this post, we’ll walk you through what HDI is, how it’s different from traditional PCBs, and why it’s becoming such a big deal.
Key Advantages of HDI PCBs Over Traditional PCBs
Here are seven major advantages HDI PCBs have over traditional ones.
They Save Space
One of the biggest reasons HDI PCBs are taking off is because they save space without compromising performance. Unlike traditional boards that require more real estate to connect components, HDI technology allows for higher wiring density in a smaller footprint — enabling thinner, lighter devices.
I spoke with Ethan Li, Marketing Director at SFXPCB. He explained, “As device dimensions shrink and performance expectations rise, HDI PCBs provide the density and efficiency needed to keep up. They enable manufacturers to design smaller products without sacrificing speed or reliability.”
Better Performance and Speed
HDI boards don’t just look neat—they actually help devices run better. Since the components are placed closer together, the electrical signals don’t have to travel as far. This means data moves faster and the device responds quicker. Whether it’s a phone loading an app in a flash or a car’s GPS giving directions smoothly, that extra speed makes a real difference. Traditional PCBs can handle basic tasks, but when it comes to speed and performance, HDI wins.
Fewer Problems, More Reliability
When devices stop working, it’s often because something inside the circuit board failed. With HDI, there are fewer chances for things to go wrong. That’s because HDI uses smaller, more direct connections and fewer layers overall. Eric Andrews, Owner of Mold Inspection & Testing, shares, “Fewer layers mean fewer chances for something to get damaged or disconnected. That makes HDI boards more reliable, especially in devices that go through a lot of movement or rough conditions, like smartwatches, medical tools, or even aerospace equipment.”
Ideal for Small and Complex Designs
Try to imagine all the parts that go into a smartphone — camera, processor, sensors, battery management systems — all packed into something that fits in your hand. HDI makes this possible. It allows engineers to design boards that are not just smaller, but also more complex without adding more layers or thickness.
“Traditional PCBs would need multiple layers and larger space to handle this kind of complexity, which just isn’t practical in modern gadgets. HDI keeps the design clean, tight, and efficient,” adds Erick Recors, Founder & CEO of Fullbloom Greenhouse.
Less Power, More Efficiency
Another great thing about HDI boards is that they use less power. Since the connections between parts are shorter, not as much energy is lost when signals move through the board. This not only helps the device work better but also saves battery life.
That’s a big deal for things like wireless earbuds, fitness trackers, and smartphones where every bit of battery life matters. According to Gerald Chan, Founder of HighGround.asia, “Traditional PCBs, with their longer paths and extra layers, simply can’t compete when it comes to power efficiency.”
Future-Ready Technology
Maybe the biggest reason HDI is taking over is that it’s built for the future. As new technology comes out, from smart glasses to electric vehicles, the demand for compact, high-speed, energy-efficient boards is only growing.
HDI is already being used in industries like aerospace, medical tech, and consumer electronics, and it’s not slowing down anytime soon.
“While traditional PCBs still have their place in simpler devices, HDI is what most companies are now choosing when they want to build something modern and high-performing,” shares Adam Fard, Founder & Head of Design at Wireframing with AI.
Why HDI Is Becoming the New Standard
Here’s why so many companies are moving away from traditional PCBs and choosing HDI instead.
Smaller Devices Need Smaller Boards
One of the biggest reasons HDI is taking over is simple: space. Devices today are thinner and more compact, but they still need to fit in more components.
Sumeer Kaur, Founder of Salwar Kameez, mentions, “Traditional PCBs take up too much room and don’t allow for tight layouts. HDI boards solve this by letting more parts fit into a smaller area. That’s how phones keep getting slimmer, and why smartwatches and earbuds can be packed with powerful tech.”
People Expect Speed and Performance
Whether it’s a phone app, a car sensor, or a fitness tracker, people expect things to respond quickly and work smoothly. HDI makes that possible. Because the parts on an HDI board are placed closer together, signals travel faster. This means better performance, fewer delays, and smoother user experiences.
Jake Smith, Founder of Private Number Plates, says, “Traditional PCBs just can’t keep up with the speed that modern devices demand.”
HDI Helps Save Battery Life
Battery life is a big deal in today’s gadgets. Nobody wants a phone that dies after a few hours or headphones that need constant charging. HDI boards help here too. Since the signal paths are shorter, they use less power. That means your devices last longer between charges. It’s one of those hidden advantages that makes a real difference in daily use.
More Reliable in Tough Conditions
Beni Avni, Owner of New York Gates, highlights, “HDI boards are more durable. Because they use fewer layers and more advanced connections, there are fewer points where something can go wrong. That makes them more reliable — especially in devices that face heat, movement, or wear and tear.” Medical devices, cars, and even military equipment are now using HDI for this reason.
Perfect for Complex Designs
Tech companies want to add more features into smaller gadgets, and that means more complex designs. “HDI boards allow for high-density layouts, meaning you can fit a lot of parts and connections in a tight space without making the board thick or clunky. Traditional PCBs would need extra layers or larger boards to handle that same complexity, which isn’t ideal when space is limited,” adds Gerald Ming, Owner of HGHR.io.
Conclusion
HDI is quickly becoming the way things are done in the electronics world. As devices get smaller, faster, and more advanced, traditional PCBs just can’t keep up anymore. HDI makes it easier to fit more into less space, improve speed, save power, and build products that work better and last longer.
Whether it’s your phone, your car, or even a medical device, chances are HDI is already playing a big role behind the scenes. And with the way things are going, it’s clear that HDI is the future of circuit board design.
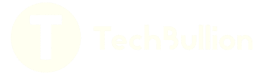