In the fast-evolving landscape of industrial automation, the integration of Artificial Intelligence (AI) into Manufacturing Execution Systems (MES) is redefining production efficiency and process optimization. Aman Jain, an expert in AI-powered manufacturing systems, explores this transformation in his latest research, shedding light on how AI-driven MES is revolutionizing the manufacturing sector.
The Evolution of Manufacturing Execution Systems
Traditional MES has long served as the backbone of industrial operations, handling workflows, inventory tracking, and quality control. However, conventional systems relied on predefined rules and historical data, limiting their adaptability. The integration of AI has introduced real-time decision-making capabilities, enabling manufacturers to process vast amounts of data instantaneously. Modern AI-enhanced MES can now analyze thousands of data points per second, allowing for dynamic adjustments that significantly reduce production inefficiencies.
Predictive Maintenance: Reducing Downtime with AI
One of the most impactful innovations in AI-powered MES is predictive maintenance. By leveraging machine learning algorithms, manufacturers can anticipate equipment failures with over 90% accuracy, providing maintenance teams with early warnings. This capability minimizes unplanned downtime by up to 41% and reduces maintenance costs by nearly 37%. With AI-driven anomaly detection, industries can move from reactive repairs to proactive maintenance, ensuring uninterrupted production cycles.
Intelligent Scheduling: Optimizing Resource Allocation
AI-powered scheduling is transforming how manufacturers allocate resources. Advanced machine learning models, combined with blockchain-secured scheduling frameworks, optimize production schedules with near-perfect accuracy. These systems automate up to 87% of routine scheduling decisions, reducing human intervention and improving efficiency. The integration of AI in resource allocation has resulted in a 33.8% improvement in production throughput and a 25.6% reduction in energy consumption, making manufacturing operations more sustainable and cost-effective.
Quality Control: Enhancing Precision with AI
Automated quality control, powered by AI, is revolutionizing defect detection and product validation. Smart vision systems equipped with deep learning models achieve nearly 99% accuracy in identifying surface defects and dimensional variations. These AI-driven quality control mechanisms not only reduce false positives by over 67% but also enhance first-pass yield rates, lowering rejection rates and improving overall production output.
Overcoming Data Integration Challenges
Despite the advantages of AI-driven MES, data integration remains a critical challenge. Manufacturing facilities operate with multiple legacy systems, leading to inconsistencies in data formats and communication protocols. Implementing standardized data governance frameworks can reduce integration complexities by 45%, improving real-time data accessibility by over 41%. Edge computing solutions further enhance data reliability, reducing processing latency by 67% and ensuring seamless AI implementation across facilities.
Digital Twins: The Future of Smart Manufacturing
Looking ahead, digital twin technology is set to play a pivotal role in AI-driven MES. Digital twins, virtual replicas of physical manufacturing processes, enable real-time simulations that optimize production lines. Facilities that have integrated digital twins report operational efficiency gains of over 40%, along with improved predictive maintenance accuracy. The combination of AI, edge computing, and digital twin frameworks is paving the way for fully autonomous, self-optimizing manufacturing ecosystems.
Workforce Transformation: The Human-AI Collaboration
AI-powered manufacturing is transforming workforce roles, shifting employees from manual tasks to AI-assisted decision-making. Companies investing in specialized training, such as data analysis and predictive maintenance, have seen a 58% improvement in proficiency, ensuring smooth AI-MES integration.
Sustainability and Environmental Impact
AI-driven MES is not only optimizing production but also driving sustainability. Smart energy management systems, powered by AI, optimize power consumption patterns, reducing energy use by up to 25%. These systems contribute to greener manufacturing by minimizing material waste and optimizing resource utilization. As industries strive to meet environmental regulations, AI-enhanced MES offers a viable solution for balancing productivity with sustainability.
In conclusion, unparalleled efficiency, reliability, and adaptability are now within reach. As Aman Jain highlights in his research, AI-driven manufacturing systems are reshaping traditional processes, enabling predictive maintenance, intelligent scheduling, and advanced quality control. With continued advancements in digital twins and edge computing, the future of smart manufacturing is bright. The convergence of AI and Manufacturing Execution Systems (MES) marks a turning point in industrial automation, offering greater autonomy and efficiency than ever before. Embracing this transformation will be key for industries aiming to maintain a competitive edge in the evolving global market.
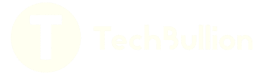