The demand for precision and efficiency in manufacturing processes continues to rise, leading to groundbreaking advancements in metalworking. This sector constantly seeks innovative technologies to improve quality and reduce costs.
The metalworking industry stands at the crossroads of tradition and technology, preparing to embrace the future with open arms. Dive into the latest trends and innovations shaping the future of metalworking.
Metal Stamping Solutions
The demand for high-quality metal components has given rise to specialized manufacturing techniques. Metal stamping, in particular, processes aim to produce precise and complex parts at scale. The process involves placing metal sheets into a stamping press, which forms the desired shapes efficiently. Industries that commonly rely on this method include automotive, electronics, and appliances, where durability and precision are mandatory.
Companies that choose to invest in metal stamping solutions have made the creation of intricate designs much easier. Investing in advanced equipment like metal stampings and skilled labor is a must for companies who want to remain competitive in the metalworking industry. Embracing modern techniques can meet growing market demands.
3D Printing
Also known as additive manufacturing, 3D printing allows for the creation of complex geometries that are often impossible with traditional methods. By layering materials to build parts, 3D printing reduces waste and minimizes the need for extensive tooling. This approach accelerates product development cycles and enables companies to go from concept to market faster than ever before.
Aerospace and healthcare are reaping the benefits of 3D printing, with lightweight components and customized implants that cater to individual patient needs. Now, there are more and more materials compatible with 3D printing.
Automation and Robotics
Manufacturers are adopting automated systems to streamline operations and increase productivity. By employing robotic arms and advanced machinery, companies can achieve higher production rates and minimize human error. These robots can operate continuously, performing tasks like welding, machining, and assembly with remarkable precision. They can adapt to varying production demands and result in higher flexibility in operations. Automation also contributes to worker safety by taking over hazardous tasks. Factories equipped with robotic solutions are saving plenty of time and driving operational excellence.
Smart Manufacturing
Smart manufacturing utilizes the Internet of Things (IoT), artificial intelligence (AI), and automation—among the most advanced technologies. Manufacturers can optimize their processes and reduce operational costs. IoT devices collect real-time data and help organizations monitor equipment performance and predict maintenance needs. AI algorithms analyze this data to achieve informed decision-making and improved product quality.
Automation can streamline repetitive tasks and allow skilled workers to focus on more complex operations. It’s not a secret that smart manufacturing improves productivity and establishes a safer working environment for all.
Sustainable Practices
Sustainability is now the central focus in the metalworking sector. Companies can recycle scrap metal and optimize resource use to diminish waste generation. Innovative technologies, such as energy-efficient machinery, are being implemented to lower energy consumption during production processes.
Many companies are evaluating their supply chains to streamline operations and reduce carbon footprints. The shift toward sustainable practices aligns with increasing regulations and growing consumer demand for environmentally friendly products. Many manufacturers are reporting benefits, including cost savings and improved brand reputation, derived from adopting sustainable methods.
Digital Twin Technology
Digital twin technology is emerging as a powerful tool in metalworking. This innovative approach creates a virtual replica of physical assets, processes, or systems. By simulating different scenarios, manufacturers can analyze performance, predict outcomes, and optimize operations without disturbing actual production lines. Implementing digital twin technology allows for detailed monitoring and precise adjustments to machinery and workflows and results in higher-quality outputs.
Manufacturing industries want to achieve better accuracy and performance, and digital twins offer invaluable insights to guide operational strategies. The integration of digital twins into metalworking workflows represents a technological advancement and an opportunity for sustained growth.
Workforce Training
With advancements in technology comes the necessity for a skilled workforce capable of adapting to new tools and processes. Investment in training programs can cultivate talent in the metalworking sector. These programs focus on skill enhancement for existing employees, introducing them to emerging technologies and methodologies.
When companies create a culture of continuous learning and development, their workforce will be knowledgeable and remain competitive. Education initiatives can attract new talent to the industry and have a steady pipeline of skilled professionals ready to tackle future challenges. A well-trained workforce can maximize productivity, innovation, and overall success.
The metalworking industry is on the brink of significant transformation, driven by technological advancements and innovative practices. As automation, 3D printing, smart manufacturing, and sustainable methods are on the rise, the capabilities of manufacturers will expand.
Staying ahead in this evolving landscape requires businesses to remain adaptable and open to embracing new methodologies. Collectively, these advancements paint an exciting picture of a future where metalworking continues to thrive through ingenuity and resourcefulness.
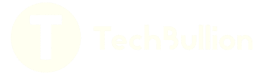