Accelerating Prototyping and Product Development in IoT
3D printing is revolutionizing prototyping in the Internet of Things (IoT) industry by significantly speeding up product development cycles. Traditional manufacturing methods, such as injection molding, typically require weeks or even months to create prototype enclosures, circuit housings, and sensor casings. In contrast, 3D printing enables designers to produce functional prototypes in just hours. This rapid prototyping allows for quick testing, immediate iterations, and real-time feedback based on performance data, greatly improving the development process. For IoT companies, where quick turnaround times are critical to staying competitive, 3D printing’s speed and flexibility provide a significant edge, reducing time-to-market and enabling faster innovation.
Customization and Design Flexibility for IoT Devices
IoT devices come in a wide variety of shapes and sizes, from health monitors and industrial sensors to smart home gadgets. With 3D printing, manufacturers gain the ability to produce highly customized enclosures and components that are perfectly suited to each device’s specific requirements. Unlike traditional manufacturing methods, which can be expensive and time-consuming when it comes to making design adjustments or producing small batches, 3D printing offers complete flexibility. Engineers can optimize designs for functionality, durability, and aesthetics, creating tailored solutions without the need for molds or tooling.
The flexibility of additive manufacturing is particularly beneficial for creating bespoke designs for niche IoT applications. Metal 3D printing, for example, offers the precision and strength required for advanced use cases such as rugged industrial sensors or medical-grade IoT devices. With 3D printing, businesses can create IoT devices that are not only more effective but also better suited to meet the needs of specific users or industries.
Cost-Effective and On-Demand Manufacturing
Traditional manufacturing techniques often involve costly molds, tooling, and large-scale production runs, which can make small-batch production expensive. 3D printing, however, eliminates these upfront costs and allows for on-demand manufacturing, making it a more affordable solution for small businesses and startups in the IoT space. Companies no longer need to invest in expensive equipment or large production quantities. Instead, they can produce small batches of components or prototypes as needed, drastically reducing costs.
This on-demand manufacturing capability is especially advantageous in the fast-evolving world of IoT, where designs frequently change and rapid prototyping is required. By enabling localized production, 3D printing also reduces shipping costs and minimizes supply chain dependencies. Companies can produce IoT devices and components as needed, without worrying about long lead times or global supply chain disruptions.
Integration of Advanced Materials in IoT Manufacturing
The development of advanced 3D printing materials has expanded the possibilities for IoT device production. While traditional manufacturing is often limited to a few standard materials, 3D printing supports a wide range of specialized filaments, including conductive materials, flexible polymers, and high-temperature-resistant composites. These materials allow manufacturers to create complex components with embedded functionality, making them ideal for IoT applications.
For example, conductive filaments enable the integration of electrical pathways directly into printed parts, eliminating the need for separate wiring. Flexible polymers are perfect for creating wearable devices or IoT products that require flexibility and durability, while high-performance composites offer strength and heat resistance for industrial-grade IoT sensors. As the material options for 3D printing continue to grow, they will enable even more efficient, lightweight, and durable smart devices.
Sustainability Benefits of 3D Printing in IoT
Sustainability is a growing concern in all industries, and manufacturing is no exception. Traditional manufacturing methods, such as injection molding, tend to generate significant material waste and consume large amounts of energy. In contrast, 3D printing promotes sustainability by minimizing waste, using recyclable materials, and reducing energy consumption. Since 3D printing is an additive process, it uses only the material required to create each part, leading to more efficient use of resources.
Additionally, 3D printing makes it possible to produce small batches of IoT devices on demand, further reducing the environmental impact associated with overproduction. By embracing 3D printing, IoT manufacturers can not only cut costs but also align their production processes with sustainability goals, supporting eco-friendly development cycles and contributing to a greener future for the IoT industry.
Future Implications and Emerging Trends in 3D Printing for IoT
As 3D printing technology continues to advance, its potential impact on the IoT industry will only grow. Several emerging trends and innovations are likely to further shape the future of IoT manufacturing:
Printed Electronics
Researchers are exploring ways to 3D print entire circuit boards and electronic components, which could streamline the manufacturing process by reducing the need for traditional assembly methods. This could lower production costs, improve efficiency, and accelerate the development of IoT devices.
Self-Healing Materials
One promising area of research is self-healing materials. These materials can automatically repair themselves when damaged, potentially extending the lifespan of IoT devices and reducing electronic waste. By integrating self-repairing materials into IoT devices, manufacturers could improve device longevity, reliability, and performance, which is particularly important for IoT applications requiring long-term durability.
Mass Customization of IoT Devices
The future of IoT could see a dramatic shift towards mass customization. With AI-powered design tools, users may soon be able to personalize IoT devices down to the hardware and software level. This would allow for the creation of highly individualized IoT solutions, tailored to specific needs and use cases. As mass customization becomes more accessible, IoT manufacturers will be able to cater to an even broader range of consumers and industries, offering truly unique and specialized devices.
Conclusion
The synergy between 3D printing and IoT is shaping a new era of innovation in smart device manufacturing. From rapid prototyping and cost-effective production to sustainable practices and advanced material integration, additive manufacturing, including the use of metal 3D printers, is transforming how IoT devices are designed and brought to market. As technology progresses, we can expect even more groundbreaking applications that will redefine the future of interconnected smart systems.
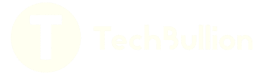