A well-trained workforce is one of the most valuable assets in a warehouse environment. Employees who receive comprehensive training not only work more efficiently but also contribute to a safer workplace. Warehouse managers must invest in effective training programs that enhance productivity, minimize errors, and promote safety. Implementing structured and ongoing training initiatives ensures employees are equipped with the necessary skills to handle day-to-day operations while reducing workplace incidents.
The Importance of Warehouse Training
Warehouse operations involve multiple processes, from inventory management and order fulfillment to equipment handling and workplace safety. Without proper training, employees are more prone to making errors, leading to operational inefficiencies and increased risks of accidents. A well-designed training program addresses these challenges by:
- Reducing workplace accidents and injuries.
- Improving order accuracy and fulfillment speed.
- Enhancing employee confidence and job satisfaction.
- Ensuring compliance with industry regulations and safety standards.
- Minimizing equipment damage and operational disruptions.
By incorporating a structured training approach, warehouse managers can create a more efficient and secure work environment.
Key Components of Effective Warehouse Training Programs
1. Safety Training
Safety should be a top priority in any warehouse training program. Employees must be educated on best practices for accident prevention, emergency procedures, and proper handling of hazardous materials. Safety training should include:
- Proper lifting techniques to prevent strain and injuries.
- Fire prevention and emergency evacuation procedures.
- Use of personal protective equipment (PPE) such as gloves, helmets, and safety vests.
- Awareness of common hazards like slip-and-fall risks and forklift accidents.
- Compliance with OSHA (Occupational Safety and Health Administration) guidelines.
Regular safety drills and refresher courses help reinforce best practices and keep employees aware of potential risks.
2. Equipment Handling and Maintenance
Warehouse operations often require the use of various machinery, including forklifts, pallet jacks, and conveyor systems. Employees must receive hands-on training to operate this equipment safely and efficiently. Training should cover:
- Proper operation of forklifts and other material-handling equipment.
- Routine maintenance checks to identify potential mechanical issues.
- Safe loading and unloading procedures to prevent product damage.
- The importance of palletizing techniques to ensure stability during transport and storage.
Effective equipment training reduces workplace accidents, minimizes damage to goods, and extends the lifespan of machinery.
3. Inventory Management and Order Fulfillment
Accurate inventory management is essential for warehouse efficiency. Employees should be trained on:
- Using warehouse management systems (WMS) to track inventory in real-time.
- Proper labeling and scanning procedures to avoid misplacements.
- Effective picking and packing techniques to minimize order errors.
- Strategies for reducing waste and improving stock rotation (FIFO and LIFO methods).
A well-trained workforce ensures that products are stored, retrieved, and shipped accurately, leading to higher customer satisfaction.
4. Ergonomics and Workplace Efficiency
Training programs should also focus on ergonomic best practices to prevent long-term injuries caused by repetitive tasks. Key areas of ergonomic training include:
- Proper posture when lifting or moving heavy items.
- The use of adjustable workstations to reduce strain.
- Stretching exercises to prevent muscle fatigue and improve flexibility.
- Implementing automation tools to reduce manual labor intensity.
Promoting ergonomic awareness helps reduce work-related injuries and increases overall productivity.
5. Communication and Teamwork
A successful warehouse operates as a coordinated unit, making communication and teamwork essential. Training programs should emphasize:
- Effective verbal and written communication to prevent misunderstandings.
- The importance of collaboration between departments (e.g., receiving, packing, and shipping teams).
- Conflict resolution strategies to maintain a positive work environment.
- Leadership development programs for employees interested in advancing their careers.
Encouraging strong communication and teamwork leads to a more cohesive and efficient workforce.
Implementing Continuous Training for Ongoing Improvement
Training should not be a one-time event but an ongoing process. Warehouse managers can implement the following strategies to ensure continuous learning and improvement:
- Onboarding Programs: New hires should undergo comprehensive training before starting their roles.
- Regular Refresher Courses: Periodic training sessions help reinforce best practices and keep employees up to date with new procedures.
- Cross-Training Opportunities: Training employees in multiple roles enhances workforce flexibility and ensures coverage during peak seasons.
- Use of E-Learning Platforms: Online training modules allow employees to learn at their own pace and review key concepts as needed.
- Performance Evaluations: Regular assessments help identify skill gaps and provide targeted training solutions.
By prioritizing continuous learning, warehouse managers create a culture of improvement that benefits both employees and operations.
Conclusion
A well-structured warehouse training program significantly enhances productivity and safety. By focusing on safety protocols, equipment handling, inventory management, ergonomics, and communication, warehouse managers can develop a highly skilled workforce. Incorporating training on palletizing techniques ensures goods are handled and stored efficiently, reducing product damage and improving warehouse organization.
Investing in continuous training programs not only improves operational efficiency but also fosters a safer and more engaged work environment. As warehouses continue to evolve, ongoing education will remain a crucial component of long-term success.
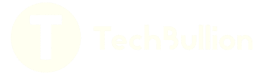