Understanding the science of adhesion in industrial applications is crucial for enhancing manufacturing processes and ensuring product integrity. This knowledge allows industries to select the right adhesive types and application techniques, optimizing efficiency and performance.
In today’s industrial environment, adhesives provide reliable bonding solutions across sectors. Their application ranges from simple assemblies to complex components, underscoring their versatility. The adhesive application process involves detailed steps and best practices designed to optimize efficiency and performance. Mastering these techniques ensures product longevity and reliability.
Introduction to Industrial Adhesive Applications
Adhesives offer solutions that mechanical fasteners cannot match, bonding diverse materials like metals, plastics, and composites. Industries such as automotive, electronics, and aerospace rely heavily on adhesives. These industries demand high-strength bonds that withstand environmental stressors and operational wear over time.
The evolution of adhesives has led to innovations catering to industrial needs. Specialized adhesives enable manufacturers to achieve desired performance characteristics while maintaining cost-effectiveness. Staying updated with these advancements allows industries to leverage adhesives’ full potential.
Understanding adhesive applications allows for effective implementation within processes. This knowledge boosts productivity and ensures compliance with industry standards. Proper application enhances product durability and reduces production downtime, critical for maintaining a competitive edge.
Quality control measures play a vital role in industrial adhesive applications. Regular testing and monitoring ensure bonds meet specifications and perform reliably under stress. Implementation of standardized procedures, coupled with detailed documentation, helps maintain consistency across production batches while facilitating troubleshooting when issues arise.
Types of Adhesives
Adhesives come in various formulations, each designed for specific applications. Water-based adhesives are popular for their environmental friendliness and ease of use, ideal for porous substrates. Hot melt adhesives offer quick bonding and flexibility, suitable for high-speed production lines.
Custom adhesives meet unique industrial requirements, offering solutions where standard adhesives fall short. These formulations provide enhanced resistance to chemicals or extreme temperatures, catering to specialized applications. Selecting the appropriate type based on operational needs ensures optimal results.
Choosing the right adhesive impacts initial bond strength and long-term durability. Factors such as curing time, bond strength, and substrate compatibility must be considered. Familiarity with these variables allows informed decisions aligning with production goals.
Factors Influencing Adhesive Application
Successful adhesive application hinges on several key factors. Surface preparation is paramount; contaminants like dust or moisture can impede bonding. Ensuring clean surfaces is essential for strong adhesion.
Environmental conditions play a crucial role in bonding. Temperature fluctuations or high humidity levels can affect adhesive properties. Controlling these variables helps maintain consistent bond quality.
The choice of application method influences bonding effectiveness. Techniques like spraying or roll-coating must be selected based on material compatibility. Adapting methods ensures adhesives perform as intended under diverse conditions.
Step-by-Step Application Process
The journey from raw material preparation to final product assembly involves critical steps for optimal bonding. Surface cleaning removes contaminants before adhesive application begins.
Once surfaces are prepared, adhesive is applied using techniques tailored to material properties. Consistent application thickness ensures uniform bonding. Attention to detail avoids pitfalls like air entrapment or uneven distribution.
Curing follows application, facilitating chemical reactions necessary for bond formation. Adhering to recommended curing times guarantees maximum bond strength while minimizing defects.
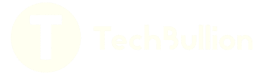