With the continuous development of modern industry, lubricants play a vital role in various types of mechanical equipment and engineering. Whether in the fields of automobiles, aerospace or mechanical manufacturing, lubricants can effectively reduce friction, extend the service life of equipment and improve operating efficiency. However, the packaging of lubricants is crucial to their effectiveness, safety of use and long-term effectiveness. As a traditional and efficient packaging solution, tin cans have been widely used in the packaging of industrial lubricants due to their excellent pressure resistance and corrosion resistance. This article will explore in depth how tin cans can provide reliable packaging solutions for industrial lubricants and analyze the important role played by tin can manufacturers in this process.
Pressure resistance of tin cans
Industrial lubricants usually need to work in high temperature and high pressure environments, especially in mechanical equipment and engines. The packaging of lubricants must have good pressure resistance to prevent damage or leakage during transportation and storage. Tin cans have significant advantages in this regard. As a metal packaging material, tin cans have strong structural strength and pressure resistance, which can effectively resist external pressure and ensure the integrity of the packaging. Even when subjected to external force impact during transportation and handling, tin cans can maintain their sealing and stability to ensure that the lubricant is not contaminated.
For lubricant applications that need to withstand greater pressure, tin can manufacturers pay special attention to enhancing the pressure resistance of tin cans during the design process, using high-strength metal materials and precision manufacturing processes to further improve their pressure resistance. This pressure resistance makes tin cans very popular in industrial lubricant packaging, ensuring that lubricants will not fail due to packaging damage during long-term storage and transportation.
Anti-corrosion properties of tin cans
The chemical composition of lubricants is usually corrosive, especially for some high-viscosity, high-chemically active lubricants or special-purpose lubricants, the corrosion resistance of packaging materials is crucial. Tin cans have very good corrosion resistance due to their metallic properties, which makes them an ideal choice for industrial lubricant packaging. The inner wall of the tin can is often coated with a protective coating that can effectively isolate the direct contact between the lubricant and the metal, thereby preventing the lubricant from corroding the tin can.
In addition, tin can manufacturers usually customize the inner coating according to the characteristics of different lubricants to adapt to lubricants of various chemical compositions. Whether the lubricant is acidic, alkaline or contains other special ingredients, tin cans can provide sufficient anti-corrosion protection to ensure that the quality of the lubricant is not affected and extend the service life of the lubricant.
Sealing and safety of tin cans
Long-term storage of lubricants requires that the packaging has a high degree of sealing to prevent the entry of air, moisture and external contaminants, and ensure the stability of the chemical composition of the lubricant. The sealing design of tin cans is very superior. Through high-precision packaging technology, it can prevent any form of leakage, avoid the volatilization of lubricants or contamination by external impurities. For lubricant products that need to be stored for a long time, tin cans provide excellent safety protection.
In the packaging of some dangerous goods, tin cans can also prevent pressure fluctuations caused by temperature changes and avoid packaging ruptures due to excessive pressure. This sealing not only ensures the quality of the lubricant, but also ensures safety during use and avoids the possible harm caused by lubricant leakage.
Recyclability and environmental advantages of tin cans
With the increasingly stringent environmental regulations, the recycling and reuse of industrial packaging materials have become the focus of attention of enterprises and consumers. As a metal packaging material, tin cans have excellent recyclability, which makes them more environmentally friendly than other packaging materials. Tin cans can be put back into use through simple recycling after use, reducing resource waste and environmental pollution.
Tin can manufacturers usually ensure that their products meet environmental standards and use coatings and materials that meet environmental requirements. In addition, compared with other plastic or glass packaging, the production process of tin cans consumes less energy and generates less waste during the manufacturing process, which meets the requirements of modern industrial environmental protection.
Wide application of tin cans in industrial lubricants
Due to their superior physical and chemical properties, tin cans are widely used in industrial lubricant packaging. Especially in the automotive industry, aerospace and high-precision mechanical equipment, lubricants need to be used frequently under extreme working conditions, and the stability and reliability of tin cans as packaging materials have been fully verified. Whether it is lubricating oil, grease or special industrial lubricant, tin cans can provide long-term and stable protection to ensure the high efficiency of lubricants during use.
In addition, when designing products, tin can manufacturers will provide customized tin can solutions according to the needs of different fields. Through the diversified design of size, shape and packaging method, the special needs of different industries for lubricant packaging are met, and the applicability of tin cans in the field of industrial lubricants is improved.
Conclusion
In general, as a packaging solution for industrial lubricants, tin cans have become the preferred material for lubricant packaging due to their advantages such as pressure resistance, corrosion resistance, strong sealing and recyclability. Tin can manufacturers have continuously optimized the production process and improved the performance of tin cans, making them show unique advantages in the packaging of various industrial lubricants. As the requirements for lubricant packaging in the industrial field continue to increase, the application of tin cans in this field will continue to play an important role and become an ideal choice to ensure the quality, safety and environmental protection of lubricants.
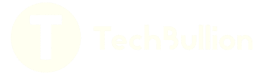