The oil and gas industry is evolving, and refinery planning software is playing a crucial role in optimizing operations, reducing costs, and improving efficiency. Traditional methods relied on manual planning and outdated systems, leading to downtime, inefficiencies, and increased risks. Today, modern AI-driven refinery optimization software provides real-time data, predictive analytics, and automated decision-making, helping refineries stay competitive.
What You’ll Learn in This Article
✔ What is refinery planning software? – Understand its purpose and importance
✔ The true cost of implementation – Breakdown of initial and ongoing expenses
✔ Key benefits of modern refinery software – How it improves efficiency and reduces waste
✔ Comparison: Traditional vs. modern solutions – Why automation is the future
Understanding Refinery Planning Software
Refinery planning software is a game-changer in the oil and gas industry, transforming how refineries manage crude selection, optimize processes, and maximize profitability. Traditionally, refineries relied on manual planning methods and historical data, which often led to inefficiencies and increased costs. Today, modern refinery optimization software leverages predictive analytics, AI, and machine learning to streamline operations and improve decision-making.
🔹 How Does Refinery Planning Software Work?
At its core, refinery planning software integrates real-time operational data, economic models, and market forecasts to help refineries make better strategic decisions. It allows engineers to:
✔ Optimize crude oil selection based on yield and cost-effectiveness
✔ Predict refinery output with predictive analytics
✔ Minimize operational costs by reducing energy consumption and process inefficiencies
✔ Simulate different operational scenarios for better risk assessment
🔹 Benefits of Refinery Planning Software
Feature | Impact |
---|---|
AI-Driven Optimization | Reduces waste and energy costs ⚡ |
Real-Time Data Processing | Enables faster, data-backed decisions 📊 |
Scenario Forecasting | Enhances risk management and cost-benefit analysis 🔄 |
Regulatory Compliance Tracking | Ensures adherence to industry standards ✅ |
Costs Involved in Implementing Refinery Planning Software
Investing in refinery planning software can significantly enhance efficiency, reduce costs, and optimize operations. However, like any digital transformation in refineries, it comes with various financial considerations. Understanding these costs is crucial for refinery managers, process engineers, and financial analysts to ensure a positive return on investment (ROI).
🔹 Initial Investment Costs
Before a refinery can reap the benefits of refinery optimization software, it must account for upfront expenses. These costs can vary based on the complexity, scalability, and features of the software.
💰 Key Initial Costs:
✔ Software Licensing Fees – One-time purchase or subscription-based pricing models
✔ Infrastructure Upgrades – Ensuring compatibility with existing refinery management systems
✔ Hardware Requirements – Servers, cloud integration, and networking improvements
✔ Customization & Integration – Adapting the software to specific refinery operations
Cost Factor | Estimated Range | Impact |
---|---|---|
Software License | $50,000 – $500,000+ | Depends on features & scale 📈 |
IT Infrastructure | $20,000 – $200,000 | Hardware, networking, and cloud services 💻 |
Customization | $30,000 – $100,000+ | Industry-specific adjustments 🔧 |
Implementation Support | $10,000 – $50,000 | Vendor assistance & setup 🛠 |
🔹 Ongoing Operational & Maintenance Costs
Once the software is implemented, ongoing costs must be factored into the long-term budget.
🔄 Recurring Costs Include:
✔ Subscription & Licensing Renewals – If using a SaaS-based model
✔ Software Updates & Security Patches – Essential for performance and compliance
✔ IT Support & Troubleshooting – Ensuring continuous refinery process optimization
✔ User Training & Employee Upskilling – Educating staff on new tools and features
🔹 Hidden Costs to Consider:
- Integration Challenges – Some older refinery systems may not seamlessly connect with new software.
- Downtime & Transition Period – During implementation, temporary productivity loss may occur.
- Regulatory Compliance Adjustments – Software updates to align with changing environmental and safety standards.
🔹 ROI vs. Cost: Is It Worth It?
While the upfront and operational costs may seem substantial, the long-term benefits far outweigh the expenses.
📊 ROI Factors to Consider:
✔ Efficiency Gains – AI-driven predictive analytics for refineries reduces planning errors
✔ Cost Savings – Optimized crude selection and energy consumption lower expenses
✔ Regulatory Compliance – Reduces fines and enhances environmental safety
✔ Scalability – Future-proofing refinery operations for market volatility
Benefits of Modern Refinery Planning Software
Refinery operations are more complex than ever, requiring precise decision-making, cost efficiency, and regulatory compliance. This is where modern refinery planning software plays a vital role. By integrating predictive analytics, machine learning, and real-time data processing, refineries can optimize operations, minimize costs, and enhance productivity. But what specific advantages does this software offer? Let’s break it down.
🚀 Increased Efficiency & Productivity
One of the most significant benefits of refinery optimization software is its ability to streamline operations and maximize output. Traditional refinery planning often involves manual processes and spreadsheets, which can be slow and prone to errors. With AI-driven automation and predictive analytics, refineries can:
✔ Optimize crude oil selection based on market trends and refinery capabilities
✔ Reduce downtime by identifying maintenance needs before failures occur
✔ Speed up decision-making with real-time data insights
Example:
A major refinery in North America implemented digital transformation in refineries, reducing operational bottlenecks and increasing efficiency by 15% within the first year.
💰 Cost Reduction & Waste Minimization
Refineries operate on tight margins, so every dollar saved directly impacts profitability. Modern refinery planning software uses predictive analytics for refineries to:
✔ Minimize crude oil wastage by optimizing refining processes
✔ Reduce energy consumption, leading to lower utility costs
✔ Improve refinery throughput, ensuring maximum output with minimal resources
Cost Factor | Traditional Approach | Modern Software Impact |
---|---|---|
Energy Costs | High due to inefficiencies | Optimized for lower energy use ⚡ |
Material Wastage | Unavoidable losses | AI-driven reduction 🔍 |
Maintenance Costs | Reactive & costly repairs | Predictive maintenance 📊 |
Example:
A European refinery using AI-driven refinery planning software reported a 20% reduction in energy costs due to real-time process optimizations.
📊 Enhanced Decision-Making & Forecasting
The ability to forecast production outputs, costs, and market demands is crucial for any refinery. Modern crude oil refining software provides:
✔ AI-based simulations to test different production scenarios
✔ Real-time monitoring, helping managers make data-driven decisions
✔ Market trend analysis, allowing refineries to adjust output based on pricing fluctuations
Why This Matters:
Instead of relying on outdated historical data, refineries can predict future market changes and adjust strategies proactively.
⚖ Improved Compliance & Risk Management
The oil and gas industry is heavily regulated, and non-compliance can result in severe fines and operational shutdowns. Refinery planning software ensures:
✔ Automated compliance tracking for environmental and safety regulations
✔ Detailed reporting features, reducing manual auditing efforts
✔ Risk assessment models to identify potential hazards before they become costly issues
Case Study: Modernizing an Aging Refinery with Automation
Background
In 2012, a major West Coast oil refinery faced a growing challenge: maintaining its 290,000 barrels-per-day production capacity with aging equipment. With over 1,100 miles of pipelines and a distributed control system, nearly half of the refinery’s 185 programmable logic controllers (PLCs) were outdated, increasing downtime, safety risks, and operational inefficiencies. The refinery needed a future-ready infrastructure to enhance reliability, improve diagnostics, and reduce maintenance disruptions.
Challenges
- Aging PLCs offered limited diagnostic capabilities, making network failures difficult to trace.
- Unscheduled downtime led to hours of lost productivity and increased safety risks.
- No centralized system for managing and tracking configuration changes.
- Reliance on IT support for troubleshooting prolonged outages and delayed repairs.
Solution
The refinery partnered with Rockwell Automation to upgrade its control system in a phased approach, ensuring continuous operation. The solution included:
✔ PLC Migration – Replacing legacy controllers with Allen-Bradley ControlLogix for enhanced integration and visibility.
✔ Advanced Diagnostics – New I/O modules for real-time failure detection and network monitoring.
✔ Network Optimization – EtherNet/IP network switches provided remote access for efficient troubleshooting.
✔ Change Management Software – A centralized repository for tracking modifications, improving security and compliance.
Results
- Downtime reduced from hours to minutes with faster network troubleshooting.
- Improved safety with remote diagnostics and real-time monitoring.
- Enhanced configuration control through secure, centralized change management.
- The refinery is on track to complete the full PLC migration within five years.
Source
Comparing Traditional vs. Modern Refinery Planning Solutions
Here’s a comprehensive comparison between traditional and modern refinery planning solutions:
Aspect | Traditional Refinery Planning | Modern Refinery Planning |
---|---|---|
Process Management | Follows a linear and rigid structure, where each step is sequential and dependent on the previous one. This rigidity can lead to inefficiencies when disruptions occur, as adjustments require revisiting each stage in order. | Embraces an agile approach, allowing for flexible and dynamic management. Agile processes can quickly respond to disruptions, shifting demand, and new market conditions, ensuring a more responsive and efficient operation. |
Inventory Management | Relies on stockpiling, maintaining large inventory reserves to anticipate demand. This can lead to overstocking, increased storage costs, and potential waste if demand predictions are inaccurate. | Utilizes Just-in-Time (JIT) inventory management, where goods are produced or ordered only as needed. This reduces excess inventory, optimizes warehouse space, lowers operational costs, and ensures efficient use of capital. |
Technology Utilization | Depends on manual processes, such as spreadsheets and paper records, which can be slow, error-prone, and lack real-time tracking capabilities. This makes it challenging to optimize activities or respond swiftly to issues. | Leverages automated and integrated systems, including RFID technology, cloud computing, and advanced software solutions. These technologies enable real-time tracking, data-driven decision-making, and enhanced coordination across operations. |
Customer Focus | Focuses primarily on fulfilling orders with limited interaction with the end customer. Feedback mechanisms are minimal, leading to slower adjustments to changing customer needs or preferences. | Prioritizes high engagement and feedback loops, gathering insights through various channels to understand customer preferences better, anticipate demand, and improve the overall experience. This allows for rapid adaptation to consumer needs. |
Data Integration | Operates in silos, with limited data sharing between departments, leading to fragmented information and delayed decision-making. | Features integrated systems that provide a holistic view of operations, facilitating seamless data flow and enabling informed decision-making. |
Flexibility and Scalability | Characterized by inflexibility, making it challenging to adapt to market changes or scale operations efficiently. | Designed for scalability and adaptability, allowing refineries to adjust operations in response to market dynamics and expand as needed. |
Risk Management | Employs a reactive approach, addressing issues as they arise, which can lead to delays and increased costs. | Adopts a proactive stance, utilizing predictive analytics and real-time monitoring to anticipate and mitigate potential risks before they impact operations. |
Conclusion
Investing in modern refinery planning software is a strategic move for refineries looking to enhance efficiency, reduce costs, and stay competitive. While initial expenses can be significant, the long-term benefits, including cost savings, improved decision-making, and regulatory compliance, make it a worthwhile investment.
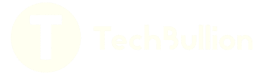